A Comprehensive Overview of Tai Eddy Current Testing
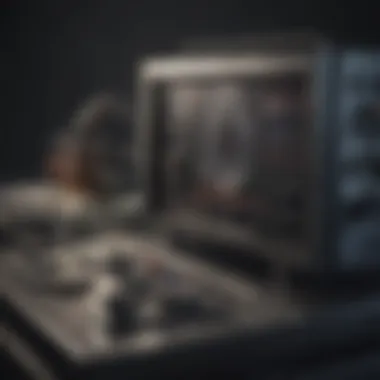

Intro
Tai Eddy Current Testing (ECT) is a widely used method in the realm of non-destructive testing. This technique is crucial for evaluating materials without causing any damage. Understanding its principles, applications, and limitations is essential for professionals in multiple industries. This overview aims to provide an insightful examination of Tai ECT, covering historical context, current applications, and future trends.
Research Overview
Summary of Key Findings
The research on Tai Eddy Current Testing has illuminated several core aspects. The fundamental principle of ECT lies in electromagnetic induction, where an alternating current generates a magnetic field. This field interacts with conductive materials, leading to eddy currents. The characteristics of these eddy currents reveal important information about material properties, like conductivity and thickness. Key findings include:
- High Sensitivity: ECT is capable of detecting small defects in conductive materials.
- Real-time Analysis: Results can be obtained quickly, enabling efficient inspections.
- Versatility of Applications: Used in industries such as aerospace, automotive, and power generation.
Research Objectives and Hypotheses
The primary objective of this research is to elucidate how Tai Eddy Current Testing enhances safety and reliability. The hypothesis posits that advancements in ECT technology, including improved sensors and software algorithms, will further expand its applicability in complex scenarios. Future explorations will emphasize:
- Understanding novel materials and their behavior under ECT.
- Examining the integration of ECT with other non-destructive techniques for enhanced outcomes.
Methodology
Study Design and Approach
This exploration of Tai Eddy Current Testing combines theoretical analysis and practical case studies. The approach includes:
- A comprehensive literature review on existing ECT technologies.
- Analyzing quantitative data from recent industry applications to identify trends and limitations.
Data Collection Techniques
Data collection employed various techniques:
- Field Studies: Gathering real-world data from companies utilizing Tai ECT.
- Interviews: Engaging with industry experts to gain insights into best practices.
- Experimental Testing: Conducting trials to assess the accuracy and efficiency of ECT under different conditions.
"Eddy Current Testing marks a turning point in non-destructive evaluation, offering precision and versatility."
Understanding these aspects of Tai Eddy Current Testing sets the stage for deeper discussions on its advantages and limitations, along with the technical details necessary for effective implementation.
Prelims to Eddy Current Testing
Eddy current testing is an essential technique in the domain of non-destructive testing (NDT). It offers a reliable means to detect defects in conductive materials without causing any harm to the test specimen. This method uses electromagnetic induction to create eddy currents, which in turn reveal information about the material's properties, structure, and integrity. Understanding its principles and relevance helps delineate the broader category of NDT, which is critical for ensuring safety and reliability in industries such as aerospace, automotive, and manufacturing.
Definition and Principles
Eddy current testing is based on the interaction between a changing magnetic field and a conductive material. When an alternating current passes through a coil, it generates an oscillating magnetic field. This field induces loops of electrical current, known as eddy currents, within the material being tested. The frequency and strength of these eddy currents vary based on several factors, including the material's conductivity, permeability, and the presence of any flaws.
The response of these eddy currents is measured and analyzed to determine the material's condition. Typically, this is done using instruments that compare the impedance of the coil with and without the material present. Any discrepancies can indicate variations caused by defects, such as cracks or inclusions. The sensitivity of the method makes it particularly effective for detecting small imperfections that could compromise structural integrity.
Historical Development
Eddy current testing has a rich history that spans several decades. The technique emerged in the early 20th century, with initial developments primarily focusing on the electric and magnetic principles proposed by pioneers such as Michael Faraday and Joseph Henry. Their discoveries laid the groundwork for understanding how electromagnetic induction could be leveraged.
Initially, usable applications of eddy current testing arose in laboratory settings. As technology advanced through the mid-20th century, its applications broadened significantly. The aerospace industry began to adopt the method for inspecting aircraft components during manufacturing and maintenance.
By the 1970s, advancements in electronics and computer modeling further enhanced eddy current testing methods. These technologies allowed for more sophisticated signal interpretation, making it easier for technicians to identify complex defects. Today, this testing method continues to evolve, integrating digital technologies and improved signal processing capabilities, which enhance both efficiency and accuracy.
Eddy current testing is now a critical tool in various industries, proving its utility by helping to uphold safety standards and quality assurance practices.
Understanding Tai Eddy Current Testing
Understanding Tai Eddy Current Testing is crucial for grasping the nuances of non-destructive testing (NDT) methods. This approach leverages electromagnetic principles to identify defects within conductive materials without causing any harm. The scope of Tai Eddy Current Testing goes beyond traditional applications, bringing forth innovative techniques and insights that are shaping various industries today.
Unique Features of Tai Testing
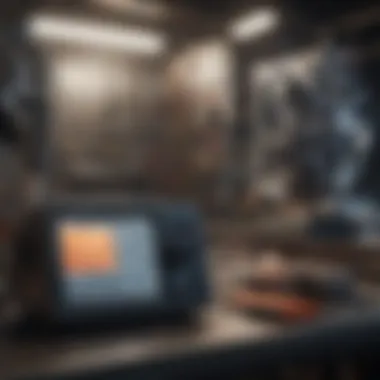
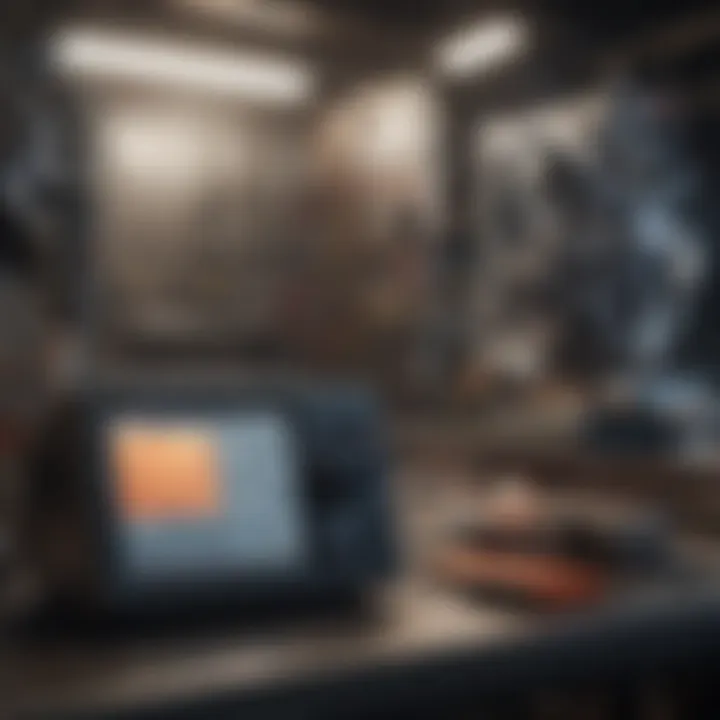
Tai Eddy Current Testing exhibits several unique features that make it particularly effective. One standout attribute is its ability to work with a variety of materials, such as metals and conductive polymers. This adaptability broadens its application spectrum significantly.
Another significant aspect is the rapid data acquisition process. Unlike some competing methods, Tai Testing offers real-time analysis. This allows for immediate decision-making, which is paramount in high-stakes environments like aerospace or energy sectors.
Additionally, Tai Testing systems often incorporate advanced algorithms for enhanced signal processing. This not only improves accuracy but also allows for the detection of smaller flaws that might go unnoticed by traditional methods.
"The ability to detect defects that are less than a millimeter in size is one of the most compelling features of Tai Eddy Current Testing."
Comparison with Traditional Methods
When compared to traditional NDT methods, Tai Eddy Current Testing provides distinct benefits. For instance, techniques like Ultrasonic Testing require direct contact and a coupling medium to be effective. In contrast, Tai Testing can function effectively without direct contact, reducing setup time and material costs.
Another point of differentiation is sensitivity. Traditional methods may struggle with certain types of materials or surface conditions. Tai Eddy Current Testing, however, can easily adjust to varying surface conditions, allowing for consistent results regardless of environmental variables.
Moreover, the speed of inspection is also significantly enhanced. Typical inspections can take considerable time with conventional methods. Tai Eddy Current Testing, with its rapid feedback, streamlines processes, leading to more efficient workflow in manufacturing and maintenance.
These aspects underscore the value of Tai Eddy Current Testing as a pivotal technique in the evolving landscape of NDT, offering substantial benefits in terms of speed, adaptability, and precision.
Technical Foundation of Tai Eddy Current Testing
In the context of Tai Eddy Current Testing, the technical foundation serves as the backbone of its implementation and efficacy. Understanding this foundation allows practitioners and researchers to appreciate how the techniques work and their relevance in various applications. This section aims to clarify key elements such as electromagnetic principles, instrument design, and advanced signal processing techniques that underpin Tai Eddy Current Testing.
Electromagnetic Principles
Eddy current testing is based on the principles of electromagnetism. When an alternating current flows through a coil, it produces a time-varying magnetic field. This field penetrates a conductive material placed near the coil and induces circular electrical currents, known as eddy currents, in that material. The density and distribution of these currents are influenced by several factors, including the material properties, geometry, and the frequency of the alternating current.
The interaction between the induced eddy currents and the magnetic field results in changes to the impedance of the coil, which is detected and analyzed. This principle is critical in evaluating the integrity of materials without causing any damage, making it suitable for non-destructive testing. Understanding these principles is essential for refining the processes involved and enhancing detection sensitivity.
Instrument Design and Functionality
The design of instruments used in Tai Eddy Current Testing is crucial for optimizing performance and accuracy. Typically, these instruments consist of sophisticated probes and electronic circuitry that convert changes in impedance into measurable signals. Probes can vary in shape and size, allowing for adaptation to different surfaces and geometries.
Instruments often include user interfaces that facilitate various settings, such as frequency and gain adjustments. These settings play an important role in targeting specific defects and enhancing sensitivity. Moreover, modern devices can be equipped with automated features, reducing the potential for human error. The ability to capture real-time data allows for immediate analysis, leading to efficient decision-making in industrial applications.
Signal Processing Techniques
After the eddy currents are induced and changes measured, advanced signal processing techniques are employed to extract relevant data from the raw signals. These techniques can include filtering, Fourier transforms, and statistical analysis, which help in identifying anomalies or defects in the material being tested.
For example, filtering techniques can remove background noise, improving the clarity of the signals. Additionally, advanced algorithms can help in characterizing the specific nature of defects, such as size, depth, and orientation. By utilizing these signal processing methods, testers can achieve a higher level of accuracy in defect detection, which is vital across various sectors like aerospace, automotive, and energy.
The technical foundation of Tai Eddy Current Testing is essential not just for direct analysis but also for advancing techniques that enhance reliability and performance across multiple industries.
Understanding and harnessing these technical foundations empower professionals to carry out more effective inspections, ensuring safety and quality in engineering applications.
Applications of Tai Eddy Current Testing
Tai Eddy Current Testing has grown to be an essential technique in various industrial sectors. The method's unique properties allow it to be applied effectively in fields such as aerospace, automotive, energy, and manufacturing. By providing insights into material integrity, this testing form supports quality assurance and enhances safety measures. The integration of Tai Eddy Current Testing will be evaluated through its specific relevance in these industries, along with the benefits and challenges associated with its application.
Aerospace Industry
The aerospace industry demands the highest standards of safety and reliability, making non-destructive testing methods imperative. Tai Eddy Current Testing is critical here, allowing for the detection of surface and near-surface flaws in metallic materials commonly used in aircraft structures. For instance, it can identify cracks, corrosion, and other degradation signs that could lead to catastrophic failures.
The method's ability to test complex shapes and structures further enhances its value. Using probes designed for intricate geometries, it provides thorough examinations without requiring dismantling or exposing the components to damage. This means that inspections can occur more frequently, greatly improving maintenance schedules and compliance with safety regulations.
Automotive Sector
In the automotive sector, Tai Eddy Current Testing has become vital for ensuring quality controls during the manufacturing process. Production involves numerous critical components, such as engine parts and chassis, where flaws can lead to serious performance issues or safety hazards.
The efficiency of Tai Eddy Current Testing allows for fast inspection, reducing production downtime. Its sensitivity to small defects helps manufacturers maintain high quality, avoiding costly recalls. Furthermore, as vehicles evolve towards hybrid and electric designs, ensuring the integrity of new materials becomes increasingly important, positioning Tai Eddy Current Testing as a future-proof solution.
Energy Sector
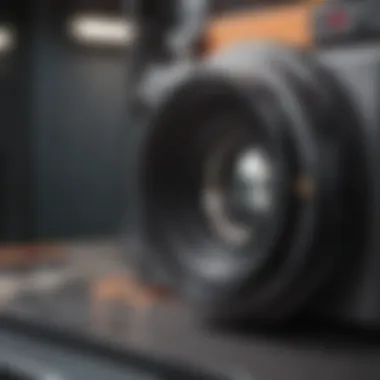
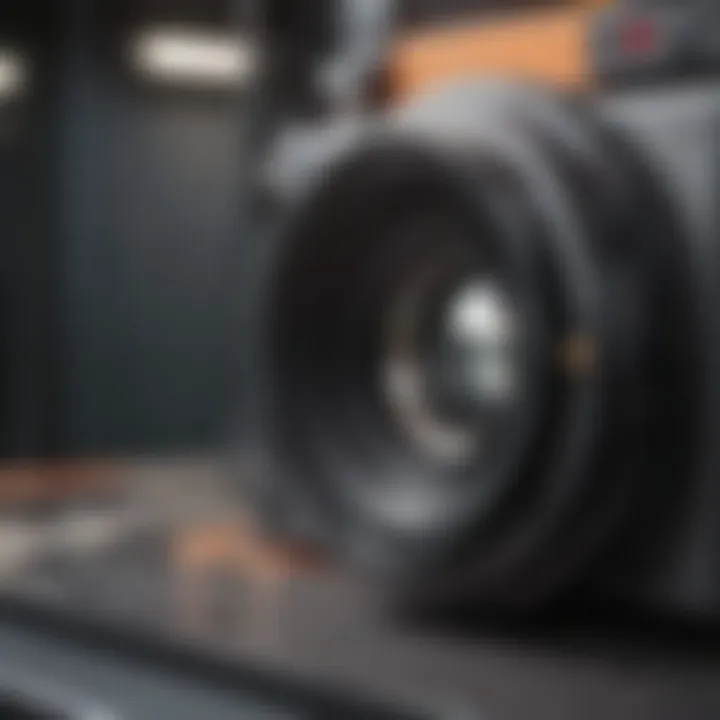
The energy sector relies on dependable equipment, especially in oil, gas, and renewable energy. Tai Eddy Current Testing can detect defects in welds, tubing, and various components of critical infrastructure. Given the harsh environments in which this equipment operates, the ability to perform reliable inspections without interrupting operations is crucial.
Moreover, with the increasing push for sustainable energy sources, the demand for new technologies, such as wind turbines and solar panels, rises. Tai Eddy Current Testing provides an effective method to assess these new materialsโ durability and performance, ensuring hardware's long-term reliability as the industry evolves.
Manufacturing and Quality Control
In manufacturing, maintaining stringent quality control standards is necessary to compete effectively. Tai Eddy Current Testing is instrumental in inspecting materials that undergo extensive processing. Its non-destructive nature means that products can be evaluated without affecting their performance or usability.
This testing method enhances the quality assurance processes by providing immediate feedback on defects. It allows manufacturers to make timely decisions, reducing waste and costs. By fostering a culture of quality, Tai Eddy Current Testing supports continuous improvement initiatives across manufacturing processes.
"The application of Tai Eddy Current Testing is increasingly crucial as industries prioritize safety, quality, and efficiency in their operations."
Advantages of Tai Eddy Current Testing
Tai Eddy Current Testing offers several significant advantages, making it a valuable tool in non-destructive testing applications. Understanding these advantages is essential for technicians and engineers to make informed decisions about inspection methods. Here, we will explore the key benefits and considerations that highlight why Tai Eddy Current Testing is preferred in various industries.
Non-Destructive Nature
One of the most critical features of Tai Eddy Current Testing is its non-destructive capability. This means that the testing process does not harm or alter the material being inspected. It allows for the ongoing monitoring of components throughout their lifecycle without causing damage.
This characteristic is especially important in industries like aerospace and automotive, where the integrity of components is paramount. By ensuring that materials can be inspected repeatedly without compromising their function, organizations can uphold quality standards without incurring additional replacement costs. Additionally, non-destructive testing minimizes downtime, allowing for quick inspections that align with production schedules.
High Sensitivity to Defects
Tai Eddy Current Testing excels in identifying surface and near-surface defects. The sensitivity of this method enables the detection of small cracks, corrosion, and other imperfections that might not be visible to the naked eye. This high level of sensitivity is primarily due to the electromagnetic principles that underlie eddy current testing.
In particular, Tai Testing is adept at detecting variations in electrical conductivity and magnetic permeability. This ability is crucial when dealing with critical components where even minor defects can lead to significant safety risks. For instance, in the aerospace sector, catching a small crack in an aircraft's fuselage could prevent catastrophic failures during flight, thus emphasizing the method's practical relevance and reliability.
Speed and Efficiency
Another notable advantage of Tai Eddy Current Testing is its speed and efficiency. The process typically involves rapid scan rates and instantaneous data analysis. Operators can conduct tests more quickly than many traditional inspection methods, leading to shorter inspection cycles. This efficiency is particularly beneficial in production environments where time is a crucial factor.
Furthermore, the equipment used for Tai Testing has become increasingly portable and user-friendly. Modern devices allow technicians to carry out inspections in the field or at various production stages with ease. As a result, businesses can enhance their operational productivity while ensuring high-quality output. The quicker feedback from inspections allows for faster decision-making and potentially reduces the costs associated with extended downtimes or repairs.
"In the realm of non-destructive testing, the advantages of speed, sensitivity, and non-destructive nature make Tai Eddy Current Testing a preferred option for many industries."
In summary, the advantages of Tai Eddy Current Testing are evident. Its non-destructive approach preserves material integrity, high sensitivity ensures early detection of defects, and its speed contributes to operational efficiency. Collectively, these factors enhance the appeal of Tai Testing in various industrial applications.
Limitations and Challenges
Understanding the limitations and challenges associated with Tai Eddy Current Testing is crucial for practitioners and researchers. Despite its advantages, there are specific factors that can hinder its effectiveness and applicability across various scenarios. These limitations primarily arise from material constraints, surface conditions, and the necessary skill set for operators. By delving into these topics, one can appreciate the complexities involved in optimizing this testing method while also recognizing where it may fall short.
Material Limitations
One of the most significant factors influencing the efficacy of Tai Eddy Current Testing lies in the material properties of the items being tested. Not all materials yield reliable test results. This method predominantly applies to conductive materials such as metals but encounters challenges with non-conductive materials. Additionally, variations in conductivity, permeability, and length can also affect detection capabilities. For example, aluminum and copper exhibit different eddy current responses.
A thorough understanding of these material characteristics is essential to ensure the accurate interpretation of results.
Surface Condition Influence
The surface condition of the material being tested can greatly influence the results obtained from Tai Eddy Current Testing. Surface roughness, contamination, or the presence of coatings can hinder the flow of eddy currents, leading to inaccurate readouts. Inspectors must be aware that imperfections and contaminants might obscure defect detection. Consequently, a meticulous cleaning of surfaces is often required prior to testing. A proper assessment of surface conditions aids in effectively determining whether the testing environment is suitable for reliable analysis.
Skill and Training Requirements
Another critical aspect to consider is the necessity for specialized skills and training in conducting Tai Eddy Current Testing. Although the technology has evolved, the need for qualified personnel remains. Effective analysis depends on the operatorโs understanding of both the equipment and the underlying physics of eddy currents. Misinterpretation of data can lead to incorrect conclusions regarding the integrity of the material being tested. Hence, it becomes evident that rigorous training and ongoing education are paramount in ensuring precision in this testing method.
"Investment in training is an investment in the quality of inspection and the safety of operations."
By addressing these limitations and challenges, professionals can strategize to enhance the reliability and applicability of Tai Eddy Current Testing. While the limitations can pose obstacles, understanding them allows for the implementation of effective measures to mitigate their impact.
Comparative Analysis with Other NDT Techniques
Eddy current testing is an important method in the realm of non-destructive testing (NDT). This section aims to provide a comparative analysis with other prevalent NDT methods. Understanding these differences is vital for practitioners making informed choices on testing techniques. Each method has its unique applications, benefits, and limitations. This discussion will focus on three prominent methodsโultrasonic testing, magnetic particle testing, and radiographic testing.
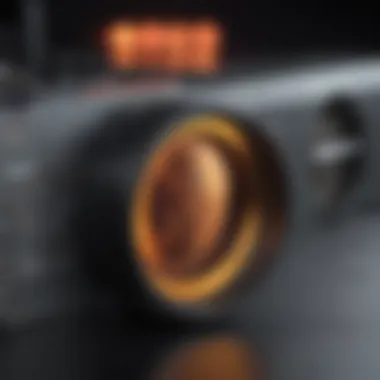

Ultrasonic Testing
Ultrasonic testing utilizes high-frequency sound waves to detect flaws in materials. By sending these waves through the material, technicians measure the time it takes for the waves to return after reflecting off a discontinuity. This technique is advantageous in detecting internal defects and measuring thickness.
Key Benefits of Ultrasonic Testing:
- High penetration capability
- Ability to provide quantitative data
- Suitable for a wide range of materials
However, ultrasonic testing requires a skilled technician to interpret the results accurately. Additionally, more surface preparation may be needed compared to eddy current testing. The sensitivity of ultrasonic testing to surface conditions can limit its effectiveness.
Magnetic Particle Testing
Magnetic particle testing is another non-destructive technique that is particularly effective on ferromagnetic materials. This method involves magnetizing the material and applying iron particles. When a defect is present, the particles accumulate at the flaw, making it visible.
Strengths of Magnetic Particle Testing:
- Cost-effective and straightforward
- Quick detection of surface and near-surface defects
- Does not require significant training for the technician
Yet, it is limited to certain materials and geometries. It also cannot detect subsurface defects, which are crucial in several applications. When comparing with Tai Eddy Current Testing, itโs clear that eddy current can identify subsurface flaws, which enhances its applicability across various industries.
Radiographic Testing
Radiographic testing employs X-rays or gamma rays to inspect the internal structure of a component. The radiation passes through the material and onto a film or detector. Different densities show variations in material integrity. This method is valuable for assessing welds or identifying internal defects.
Advantages of Radiographic Testing:
- Provides a permanent record of tests
- High sensitivity for detecting small defects
- Can assess complex geometries and thick materials
Despite these strengths, radiographic testing does have safety concerns due to the use of radiation. The accountability for safety measures may also add an operational burden. Moreover, interpretation requires highly trained specialists, similar to the requirements of ultrasonic testing.
Ending
Future Directions in Tai Eddy Current Testing
The future of Tai Eddy Current Testing promises transformative advancements that can enhance the field of non-destructive testing. As industries evolve, so too must the techniques used to ensure safety and integrity. Understanding these future directions is vital for researchers and practitioners, as they can directly influence the development of the technology and its applications in various sectors.
Technological Innovations
Recent years have seen notable technological innovations in the realm of Tai Eddy Current Testing. Advanced data analytics and artificial intelligence are playing crucial roles in refining testing processes. These innovations allow for improved accuracy in identifying defects and interpreting results. Furthermore, automating some aspects of testing reduces human error and increases efficiency. Smart sensors and IoT integration are also being explored, enabling real-time monitoring and data collection. This shift not only enhances precision but also allows for predictive maintenance, ultimately optimizing operational costs across industries.
Cross-Industry Applications
The versatility of Tai Eddy Current Testing lends itself to a broad range of applications across different sectors. In aerospace, it helps to ensure safety in critical components by detecting fatigue cracks in materials. The automotive industry benefits too, using this technology for quality control checks on parts to minimize recalls. In the energy sector, such as nuclear and renewable energy plants, maintaining the integrity of components is paramount. The knowledge gained from these applications shows that Tai Eddy Current Testing can adapt to meet the specific needs of each industry.
Regulatory and Standards Evolution
As the field of Tai Eddy Current Testing evolves, so do the relevant regulatory frameworks and standards. Organizations are increasingly recognizing the importance of optimizing testing methods to meet safety and quality benchmarks. For practitioners, staying updated with evolving standards is crucial. It involves understanding the changes in regulations that impact testing protocols. With continuously emerging technologies and methodologies, new standards are likely to encompass best practices for using Tai Eddy Current Testing efficiently and effectively, ensuring compliance and enhancing industry confidence in non-destructive testing outcomes.
"The future of technology will define the standards by which we measure safety and quality in all industries."
Future directions in Tai Eddy Current Testing are shaped by innovations, diverse applications, and evolving regulations. The ability to adapt and improve is essential for professionals in this field. As awareness increases and technology advances, Tai Eddy Current Testing will undoubtedly solidify its role as a vital tool for quality assurance in various industries.
Epilogue
In this article, the discussion surrounding Tai Eddy Current Testing is essential for understanding its growing role in non-destructive testing (NDT). The conclusion serves to tie together the various aspects explored throughout the document, emphasizing both the importance and applications of Tai Eddy Current Testing in contemporary industries.
Summary of Key Points
Tai Eddy Current Testing offers several benefits and unique features:
- Non-destructive nature: This method does not harm the material being tested, making it suitable for critical components in sectors like aerospace and automotive.
- High sensitivity to defects: It can detect surface and near-surface defects, essential for ensuring safety and reliability in various applications.
- Speed and efficiency: The testing process is generally quicker than many traditional methods, facilitating high-throughput environments such as manufacturing.
The technical foundation of this method, including its electromagnetic principles and sophisticated instrument design, supports these advantages. Moreover, the analysis of its limitations and challenges helps in understanding the context in which it can be effectively utilized.
Final Thoughts on Future Implications
Looking ahead, Tai Eddy Current Testing is poised for several advancements. The ongoing technological innovations are likely to enhance the sensitivity and accuracy of testing, thus broadening its applicability. Furthermore, as industries evolve, the demand for efficient and reliable testing methods will increase. This will drive cross-industry applications, allowing Tai Eddy Current Testing to be implemented in novel sectors.
Additionally, regulatory and standards evolution will play a critical role in shaping its future. As new industries adopt these testing methodologies, ensure compliance with the latest safety and quality standards will become more complex. Keeping abreast of these changes will be vital for professionals in the field, whether they are researchers, educators, or practitioners in industry.