Understanding Plasma Etch Chambers in Modern Tech

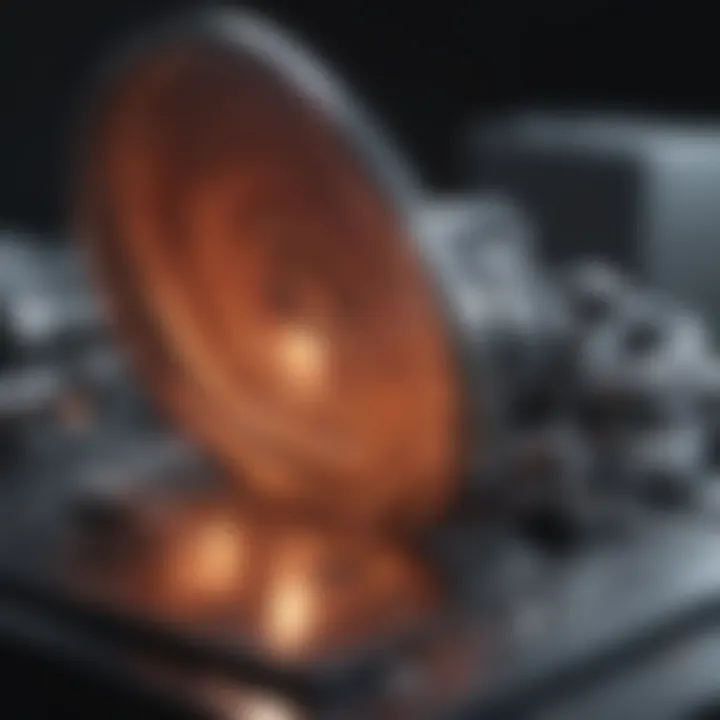
Intro
In the rapidly evolving field of technology, the plasma etch chamber stands as a critical component in semiconductor manufacturing and other materials processing domains. This article intends to dissect the operational principles behind plasma etching and to elaborate on the mechanics and configurations pertinent to etch chambers. The significance of understanding these components lies not only in their application to industry but also in their impact on research and development.
The essence of plasma etching is rooted in its ability to precisely manipulate materials at the microscopic level. This technique is fundamentally important in producing microelectronics and advanced materials. As we delve further, important topics such as various chamber designs, the plasma generation process, and the specific applications in todayβs technological landscape will be thoroughly examined.
Moreover, challenges and advancements related to plasma etching technology will be explored to provide a holistic view of this intricate field. This thoughtful exploration aims to equip students, researchers, and professionals with a comprehensive understanding of plasma etch chambers and their relevance in modern technology.
Research Overview
Summary of Key Findings
The plasma etch chamber technology has shown significant advancements over the years. Key findings in this domain include:
- Enhanced precision in material removal processes.
- Development of new etching gases and chemistries that improve efficiency.
- Exploration of novel chamber designs that optimize throughput.
- Integration of real-time monitoring systems for process control.
These findings underline the need for continued innovation and research to improve existing technologies.
Research Objectives and Hypotheses
The objectives of this research are to:
- Investigate the fundamental principles of plasma etching.
- Examine current configurations and operational mechanisms of plasma etch chambers.
- Identify and analyze specific applications in semiconductor manufacturing.
The underlying hypotheses include the expectations that advancements in technology will lead to improved etching methods and broader application ranges, ultimately influencing the efficiency of manufacturing processes in the semiconductor industry.
Methodology
Study Design and Approach
This study employs a qualitative approach, leveraging insights from existing literature and practical applications of plasma etching. It focuses on gathering in-depth analysis of techniques, identifying trends, and recognizing challenges faced by industry professionals.
Data Collection Techniques
Data was collected from various sources, including:
- Academic journals and articles related to semiconductor manufacturing.
- Industry reports detailing advancements in plasma etching technologies.
- Interviews with professionals and researchers active in this field.
- Online forums such as Reddit, where discussions on technological challenges are prevalent.
This multi-faceted approach ensures a well-rounded understanding of plasma etch chambers and their importance in modern technology.
Foreword to Plasma Etch Technology
Plasma etch technology plays a critical role in the realms of semiconductor manufacturing and materials processing. As devices shrink in size and increase in complexity, the demand for precise etching methods has never been more vital. Plasma etching offers unique advantages over traditional methods, including improved resolution and the ability to work with a variety of materials. Assessing its mechanisms and applications provides essential insights into how modern technologies are engineered.
Plasma etch technology enables high precision patterning on substrates, using reactive gases in a plasma state to selectively remove material. Its operational parameters can be finely tuned, such as pressure, power, and gas composition, to achieve desired outcomes for various industry applications. The ability to control the etch profile and feature size allows for the realization of intricate designs, particularly in semiconductor devices where dimensions can reach nanometers.
A significant benefit of this technology lies in its adaptability. Different gases used in plasma etching can be tailored to etch specific materials, affecting both selectivity and etch rates. This flexibility is crucial as the semiconductor industry continuously evolves to meet the demands for faster, smaller, and more efficient devices.
As this article unfolds, it will delve into the principles behind plasma generation, the specific components of plasma etch chambers, and the diverse applications made possible through this technology. Understanding these elements will illuminate the importance of plasma etching in modern manufacturing processes, shedding light on both the technological advancements and challenges encountered in its application.
Defining Plasma Etching
Plasma etching is a specialized technique employed to remove layers from the surface of materials using plasma. Unlike traditional etching processes that rely primarily on chemical or mechanical means, plasma etching utilizes a gas phase that is ionized to create a mixture of ions, electrons, and neutral particles. This ionized state enables reactions that effectively etch away materials with precision.
Plasma etching can take place in various pressure environments, contributing to its versatility. This process involves generating a plasma from a specific gasβtypically fluorine, chlorine, or oxygenβwithin a vacuum chamber. The resultant ions and reactive species then bombard the substrate surface, leading to material removal without damaging underlying layers.
The definition of plasma etching extends beyond mere material removal; it encompasses the strategies employed to control the etch selectivity and profile, making it an essential technique for applications in semiconductor device fabrication, microelectronics, and more.
Historical Context and Evolution
The evolution of plasma etching technology began in the latter half of the 20th century, closely paralleling advancements in semiconductor manufacturing. Initially, photolithography dominated, but as integrated circuits became more complex, the limitations of conventional etching techniques were increasingly apparent.
In the 1970s, plasma etching emerged as a solution to these challenges. Early implementations utilized simple direct-current powered systems for etching silicon dioxide and silicon nitride. As the technology advanced, researchers explored radio-frequency and microwave plasma systems, which allowed for greater control over the plasma properties and enhanced etch rates.
Today, plasma etching continues to evolve, responding to the burgeoning demands of new materials and smaller dimensions in electronic components. The refinement of chamber designs, power delivery systems, and gas compositions has significantly improved the precision and efficiency of this technology, facilitating transformative innovations across various industries. Efforts to integrate plasma etching with emerging technologies further showcase its potential as a foundational method in the materials processing landscape.
Principles of Plasma Generation
The principles of plasma generation play a critical role in understanding how plasma etch chambers work. Plasma, the fourth state of matter, consists of ionized gas that exhibits unique properties. These principles underpin the operation of plasma etch chambers, which are essential for various applications, particularly in semiconductor manufacturing. A solid grasp of how plasma is generated can aid in optimizing etching processes, enhancing precision, and improving material removal.
Understanding Plasma State
Plasma exists when a gas is energized to the point where ionization occurs. In simple terms, it is composed of positively charged ions and free electrons. This ionization process gives plasma its distinct properties, such as conductivity and responsiveness to electromagnetic fields. The balance between ions and electrons influences the etching performance, making it vital to achieve the correct conditions within the chamber.
The state of plasma can be controlled by adjusting factors like pressure and temperature. This means that achieving a stable plasma is not only advantageous but necessary for effective material processing.
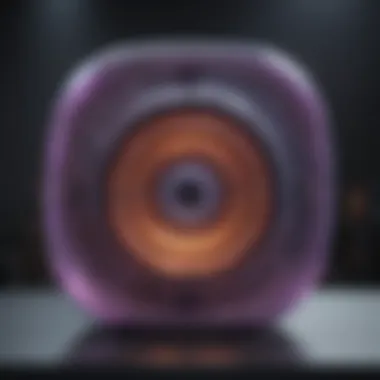
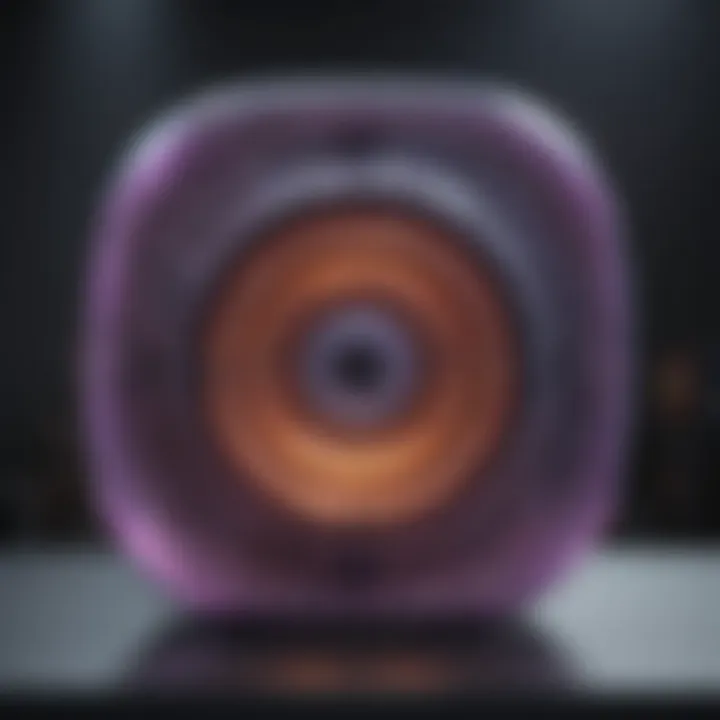
Techniques for Plasma Creation
The generation of plasma can be accomplished through various techniques. Each of these techniques has unique characteristics that influence their effectiveness in different etching applications.
Discharge
DC Discharge is one of the oldest methods for plasma generation. When a direct current is applied across two electrodes, it creates a continuous flow of electrons. This method is appreciated for its simplicity and effectiveness in creating a stable plasma state. The primary characteristic of DC Discharge is its ability to produce a uniform plasma across a relatively large area.
However, while this method is widely used, it does have its downsides. One limitation is the difficulty in maintaining control over the ion energy, which can lead to inconsistent etching results. Nevertheless, DC Discharge remains a popular choice due to its straightforward implementation and reliability in specific applications.
RF Excitation
RF Excitation uses radio frequency energy to generate plasma. This technique is advantageous because it allows for better control over the energy levels and the distribution of ions. One key characteristic of RF Excitation is its ability to operate at lower pressure levels, which can lead to improved etch uniformity.
Moreover, RF systems can be designed to balance ion bombardment and chemical etching, allowing for a finer control over the etch rate. However, the complexity and costs associated with RF systems can be a drawback for researchers and manufacturers. In the context of plasma etching, the RF Excitation method is very beneficial despite these challenges.
Microwave Plasma
Microwave Plasma is an innovative technique that utilizes microwave radiation to ionize gases. The key feature of this method is its high efficiency in generating a dense plasma. It can achieve higher plasma densities even at lower gas pressures, which is extremely beneficial for many etching processes.
The unique advantage of Microwave Plasma is its ability to uniformly distribute energy throughout the chamber. This means more consistent results over time, which is crucial for applications in semiconductor fabrication. However, the machinery needed for generating microwave plasma can be expensive, and careful tuning is required to optimize results. Nonetheless, its advantages make it a valuable option in modern plasma etching applications.
"Understanding the different techniques of plasma generation enhances our ability to manipulate processes within the etch chamber effectively."
The choice of plasma generation technique can significantly affect the efficiency and quality of etching. Through careful evaluation of each methodβs advantages and disadvantages, manufacturers can select the most suitable technique that aligns with their operational goals.
Components of a Plasma Etch Chamber
Understanding the components of a plasma etch chamber is crucial, as each element plays a significant role in the etching process. The effectiveness and efficiency of plasma etching depend heavily on the interaction between these components. Their design influences parameters such as uniformity of etch, rate of processing, and the overall versatility of the technology. Each aspect contributes to achieving high precision in semiconductor fabrication and various material processing applications.
Chamber Design and Structure
The design and structure of a plasma etch chamber directly impact the operational capabilities of the system. Typically, these chambers are vacuum-sealed to maintain low pressures necessary for plasma generation. A standard chamber is cylindrical, allowing for an even distribution of the plasma across the substrate surface. The material used to construct these chambers is often stainless steel or other robust materials that can withstand the reactive gases utilized during the etching process.
Considerations for chamber design include:
- Size: Needs to accommodate the substrates being processed.
- Port Layout: Efficient alignment for gas delivery, substrate handling, and monitoring systems.
A well-designed chamber aids in uniform etching, minimizes contamination, and enhances throughput.
Electrode Configuration
The configuration of electrodes within the plasma chamber is vital for plasma generation and control. Typically, a plasma etch chamber consists of two electrodes: a lower electrode known as the substrate holder and a powered upper electrode, which supplies the necessary energy to sustain ionization of the gas.
Different configurations offer various benefits:
- Parallel Plate Geometry: Simple and effective, ideal for uniform processing in large substrates.
- Inductive Coupling: Allows for high-density plasma and is beneficial for advanced materials requiring precision.
- Capacitively Coupled: Used mainly for thin films, allowing better control over ion energies and densities.
The choice of configuration can determine the etching attributes, affecting both selectivity and profile angle of the etched features.
Gas Delivery System
The gas delivery system is an essential component that directly influences the plasma chemistry and the etching process itself. It typically consists of mass flow controllers, gas lines, and a gas mixing system. Precise control over gas composition and flow rates enables the optimization of etching characteristics.
Key elements of a gas delivery system include:
- Mass Flow Controllers: Ensures accurate measurement and delivery of reactant and carrier gases, critical for reproducibility.
- Gas Mixing Equipment: Enables specific combinations of gases, allowing tailored reactions based on material properties.
- Purge System: To maintain cleanliness and prevent contamination between different processing runs.
This system's proper management is essential for achieving desired etch rates, selectivity, and surface quality in the final product.
"The interaction between gas delivery and chamber properties is fundamental to achieving the desired outcomes in plasma etching. Without proper control, results can vary widely."
Process Parameters in Plasma Etching
The effectiveness of plasma etching is heavily influenced by various process parameters. These parameters must be carefully adjusted to ensure optimal etching efficiency and material removal rates. Understanding these elements is crucial for improving the overall performance of plasma etch chambers. The main process parameters that impact the etching process include pressure and temperature control, power input and frequency, as well as gas composition and flow rates. A thorough exploration of these factors can shed light on their profound effects on etching outcomes and ultimately, on the quality of the final products.
Pressure and Temperature Control
Pressure and temperature are integral in influencing the behavior of plasma. The pressure inside the plasma etch chamber affects the ion density and energy, which consequently determines how effectively materials can be etched. Generally, lower pressures lead to higher ion energy, enhancing etch rates but can also result in reduced selectivity. Conversely, higher pressures tend to lower ion energy, resulting in slower etching, but they can increase the process's uniformity.
Temperature control is equally important. It impacts the chemical reactions that occur within the chamber. Elevated temperatures can accelerate the rates of these reactions, but too much heat may damage sensitive materials.
Power Input and Frequency
The power input is a significant factor in plasma etching. It dictates ion energy and affects the density of the plasma. Higher power allows for better ionization, which can result in faster etching rates. However, excess power may also lead to overheating or uneven etching. Thus, optimizing power input is essential to balance efficiency and material preservation.
Frequency of the applied power wave also matters. Different applications may require different frequencies to achieve desired etching characteristics. For example, Radio Frequency (RF) is widely used because it allows for better control over the plasma characteristics, thus improving the uniformity of the etch process.
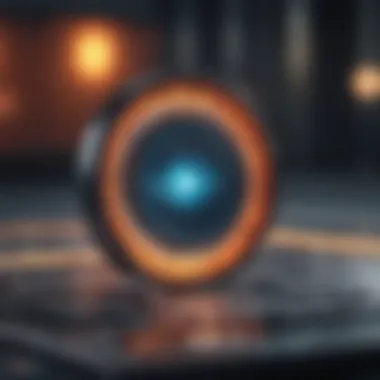
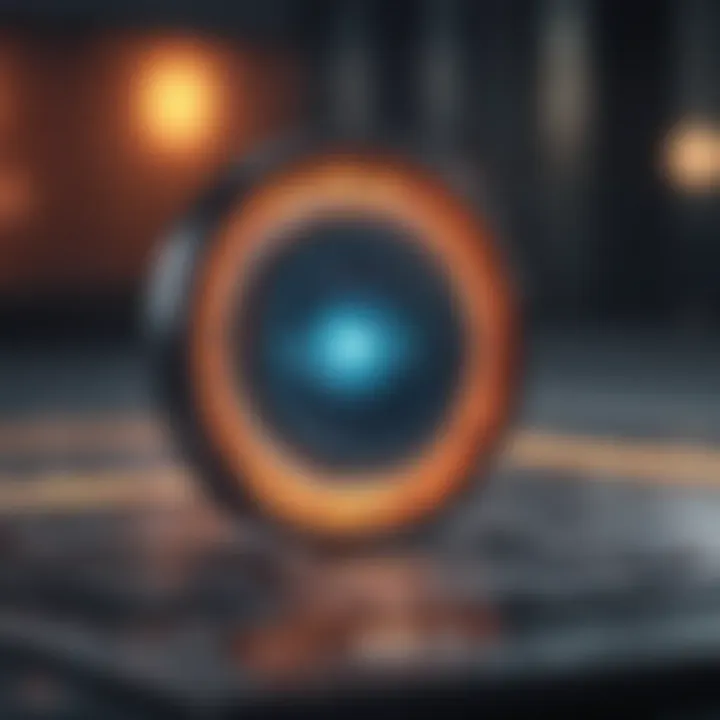
Gas Composition and Flow Rates
Gas composition directly influences the chemical environment of the plasma. The type of gases used can affect both the etching mechanism and the selectivity of the process. Common gases include fluorine-based compounds like SF6 and CF4, which are well-known for their effective etching properties on silicon-based materials. The concentration of these gases must be finely tuned as well.
Flow rates determine how quickly the gases are replenished in the chamber. If the flow rate is too high, it can dilute the active species too much, leading to inefficient etching. On the other hand, too low a flow rate may result in insufficient removal of reaction byproducts, causing contamination and affecting process efficiency. Striking the right balance in gas composition and flow rates can significantly improve the overall productivity of the etching process.
Mechanisms of Material Removal
Understanding the mechanisms of material removal is critical in the field of plasma etching. These mechanisms dictate how materials are selectively removed from substrates in a controlled manner. Knowing how effective these processes are will help researchers and engineers enhance existing technologies while developing new ones. The two primary mechanisms are ion bombardment and chemical reactions. Each plays a distinct role and offers specific advantages and considerations.
Ion Bombardment
Ion bombardment is a fundamental mechanism in plasma etching. During this process, ions generated in the plasma interact with the material surface. This can effectively lead to the physical removal of material at the atomic level. The main advantage of ion bombardment is its ability to achieve precise and anisotropic etching. Anisotropic etching refers to the removal of the material primarily in one direction, which is essential in applications like semiconductor fabrication.
Factors that influence ion bombardment include energy levels of the ions and the mass of the ions used. High-energy ions are generally more effective at overcoming surface binding forces, thereby enhancing the etching rate. Another important consideration is the angle of incidence; ions striking the surface at steep angles can lead to increased material removal. However, excessive bombardment can also damage the underlying materials, leading to defects and affecting device performance.
Chemical Reactions
Chemical reactions are another crucial mechanism by which material is removed in plasma etching. In this process, reactive species formed in the plasma engage with the material substrate to create volatile byproducts. These byproducts are then evacuated from the chamber, resulting in material removal. The specificity of chemical reactions allows for higher selectivity towards certain materials, which is particularly advantageous in multi-layered substrates.
The selection of gases introduced into the plasma chamber can significantly influence the etching outcome. For example, using chlorine-based gases in conjunction with silicon substrates can yield higher etch rates compared to other gas types. Moreover, understanding the reaction kinetics is vital for optimizing processes to achieve desirable etching profiles, which can affect the overall efficiency and fidelity of the manufacturing process.
"Ion bombardment and chemical reactions are two distinct yet complementary mechanisms that drive the efficacy of plasma etching in modern technology."
Both ion bombardment and chemical reactions illustrate the complex interplay of physical and chemical processes that enable precise material removal. This understanding is essential not only for improving manufacturing techniques but also for innovating applications in areas like microfabrication and surface modification. Recognizing these mechanisms is integral to advancing the field of plasma etching.
Applications of Plasma Etch Technology
The applications of plasma etch technology play a pivotal role in advancing various sectors, most notably in semiconductor fabrication and microfabrication. Plasma etching is essential for the production of smaller and more efficient electronic components, which are fundamental in modern technology. As devices shrink in size, the need for precise material removal increases. The advantages of plasma etching include its ability to create high-resolution patterns and its suitability for various materials.
Additionally, plasma etching offers significant benefits like scalability and versatility. It allows manufacturers to operate under different conditions, adapting to the specific requirements of various applications. For example, fine-tuning the gas composition or adjusting the pressure can yield different etching results. Thus, understanding the breadth and depth of plasma etch applications is vital for both researchers and professionals in the field.
Semiconductor Fabrication
Semiconductor fabrication is perhaps the most critical application of plasma etch technology. In this domain, plasma etching is utilized to create intricate patterns needed for integrated circuits. The precision of the etching process directly affects the performance and reliability of semiconductor devices. Plasma etching can retain fine features on silicon wafers, enabling the production of tightly packed components essential for modern electronics.
Moreover, the process supports the formation of shallow trench isolation (STI) and contact holes, which are necessary for electrical connections within chips. As the demand for more complex designs continues to rise, mastering plasma etching techniques becomes crucial for semiconductor manufacturers.
Microfabrication Techniques
Microfabrication techniques benefit significantly from plasma etching. This technology allows for the production of microelectromechanical systems (MEMS) and microfluidic devices. In these applications, control over the etching depth and profile is vital. Plasma etching provides a layer of precision that is necessary for creating microstructures with intricate geometries.
Recent advancements in this field show that plasma etching is not limited to silicon substrates but can also be applied to polymers and metals. This versatility opens new avenues for device design and manufacturing, such as in biomedical devices and sensor applications. As microfabrication continues to evolve, plasma etch technology will remain at the forefront of innovation.
Surface Modification and Cleaning
Surface modification and cleaning are additional critical applications of plasma etching. This process aids in enhancing surface properties, which is particularly useful in applications like coating adhesion and wettability. The ability to modify surfaces at a microscopic level enables improved performance for materials used in various industries, including aerospace, automotive, and electronics.
Plasma cleaning removes contaminants that may affect the performance or reliability of materials. It is a dry process, making it environmentally friendly compared to traditional wet cleaning methods. Furthermore, the precision of plasma etching allows for localized modifications, which can be essential in selective surface treatment applications.
"Plasma etching not only serves to pattern materials but also enables advancements in surface science, critical for future technology development."
In summary, the applications of plasma etch technology encompass a wide range of processes fundamental to modern manufacturing techniques, especially in sectors that rely on precision at the micro and nano scales.
Challenges in Plasma Etching
Understanding the challenges in plasma etching is essential for optimizing processes and achieving desired outcomes. This section highlights critical issues faced during plasma etching, giving insight into factors that influence performance and overall effectiveness. Properly addressing these challenges can lead to better process control, improved product quality, and enhanced production efficiency.
Selectivity Issues
Selectivity is a key parameter in plasma etching processes. It refers to the ability to preferentially etch one material over another. High selectivity is vital in semiconductor manufacturing, where different materials need to be processed without undesired effects on adjacent layers.
Several factors impact selectivity:
- Material Properties: Different materials respond uniquely to plasma exposure. Their chemical composition and physical properties can affect the etching rate.
- Etching Conditions: Parameters such as pressure, temperature, and gas composition play a crucial role in achieving desired selectivity. Fine-tuning these conditions can lead to more favorable results.
- Plasma Characteristics: The energy and density of plasma can also affect how materials are removed. Understanding plasma behavior is critical for addressing selectivity issues.
Overall, achieving high selectivity is a balance between various influencing factors, and ongoing research is focused on improving this aspect of plasma etching.
Etch Rate Control
Controlling the etch rate is another significant challenge in the plasma etching process. The etch rate determines how quickly material is removed during the etching process, influencing both the efficiency and the precision of the manufacturing process.
Factors that impact etch rate include:
- Power Input: The amount of power supplied to the plasma can directly influence the etch rate. Higher power typically results in faster etching but may lead to reduced selectivity.
- Gas Composition: The choice and mixture of gases used in the etching process alter chemical reactions that occur, thereby affecting the etch rate.
- Temperature Control: Maintaining optimal temperature is crucial. Variances can lead to inconsistent etch rates which affect material properties.
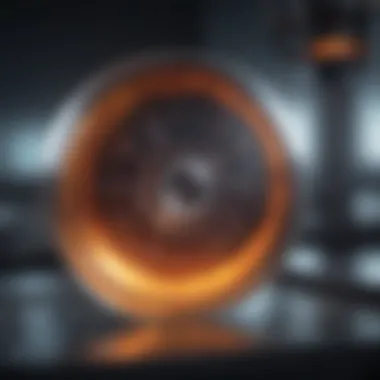
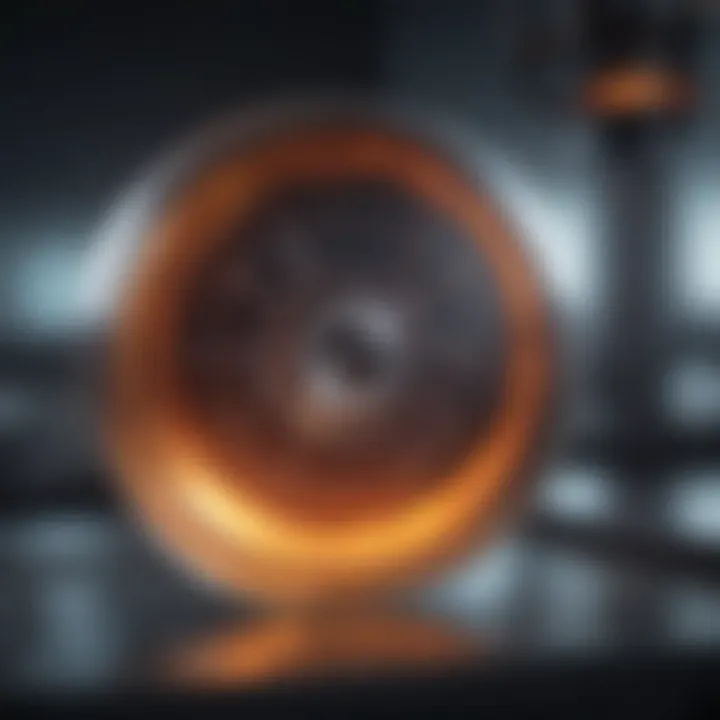
Achieving a stable and controllable etch rate is necessary for reliable production of semiconductor devices and other applications.
Material Compatibility
Material compatibility encompasses the need to consider how different materials react during the plasma etching process. Not all materials can be etched without affecting neighboring layers or structures.
Important considerations for material compatibility:
- Reactivity: Some materials may react with the plasma or etching gases, resulting in unwanted etch byproducts, which can compromise the quality of the process.
- Thermal Sensitivity: Certain materials may be sensitive to heat. If temperature rises excessively during plasma treatment, it could lead to material deformation or degradation.
- Dissimilar Materials: When etching multi-layer structures, selectivity issues arise, as one layer may react differently than another, complicating the process.
Material compatibility issues underline the necessity for thorough material analysis prior to the etching process, ensuring operational success and optimal performance.
"Plasma etching is a vital step in modern semiconductor manufacturing. Addressing its challenges leads to innovation and improved efficiency."
As the demand for advanced fabrication continues to rise, understanding and overcoming these challenges will be crucial for future advancements in plasma etching technology.
Recent Advancements in Plasma Technology
Recent advancements in plasma technology play a crucial role in enhancing the capabilities of plasma etch chambers. These developments have profound effects on efficiency, precision, and versatility in various applications. The innovations focus on refining how chambers are designed and utilized, allowing for improved material processing and fabrication techniques.
Innovations in Chamber Design
Recent innovations in the design of plasma etch chambers have significantly impacted their performance. Modern designs prioritize enhanced uniformity in plasma distribution. This uniformity is crucial as it directly affects etch quality across the substrate surface. Moreover, new materials such as ceramics and advanced alloys are being incorporated into the chamber construction. These materials provide better resistance to corrosive gases and extreme conditions.
Some notable advancements in chamber design include:
- Multi-zone Temperature Control: This allows for better management of thermal profiles during the etching process. Maintaining optimal temperatures helps in achieving uniform etching rates.
- Advanced Gas Delivery Systems: Innovations in gas mixing and delivery create more precise control over chemical reactions within the plasma chamber, leading to enhanced material removal rates and improved selectivity.
- Dynamic Loadlock Systems: These systems improve productivity by reducing the time between processing steps, allowing for more rapid transitions between different parts of the etching process.
These design enhancements not only improve performance but also reduce maintenance costs and downtime. They present a step forward in making etching processes more reliable and efficient.
Emerging Applications
Emerging applications of plasma etching technology reflect its growing relevance in various fields. The versatility of plasma etching enables it to cater to needs in both established and evolving markets. Some key areas where advancements are driving new applications include:
- Nanoelectronics: As devices shrink in size, precise etching at the nanoscale is crucial. Plasma etching technologies are increasingly adapted for fabricating nano-scale components and structures, which are essential for future electronic devices.
- Biomaterials: Plasma technology is gaining traction in modifying biomaterials, enhancing their properties for medical implants and devices. Controlled surface modifications help improve biocompatibility.
- Telecommunications Equipment: The demand for high-performance communication devices has spurred developments that optimize plasma etching processes for the production of intricate microwave circuits.
The continued research into these applications suggests a promising horizon for plasma etch technology, particularly as industries seek to miniaturize components and improve functionality.
The innovations in chamber design and applications illustrate the dynamic nature of plasma etch technology, positioning it as a vital tool in modern manufacturing and materials processing.
Future Trends in Plasma Etching
The landscape of plasma etching is rapidly evolving, as various industries push for enhanced performance and efficiency in semiconductor manufacturing. Future trends will greatly focus on sustainability and advanced integration with emerging technologies. These elements are not merely additional considerations but rather essential aspects for enhancing the plasma etch process and its overall impact on technology.
Sustainability Considerations
Sustainability has emerged as a pivotal factor in the advancement of plasma etching. The semiconductor industry is under increasing pressure to reduce its environmental footprint. Plasma etching processes are often energy-intensive and may use hazardous gases. Thus, research in this area is looking towards solutions that can minimize energy consumption and the use of harmful materials.
Some strategies under exploration include:
- Energy Efficiency: Developing methods that require less energy during the etching process can drastically reduce overall operational costs and environmental impact.
- Green Chemistry: Utilizing alternative gases that are less harmful can enhance safety and sustainability. This movement towards safer materials is often referred to as green chemistry.
- Recycling and Waste Management: Improving the waste management processes associated with gases and materials used in plasma etching is vital to minimizing environmental damage.
Companies and research institutions are actively fostering these changes, recognizing their importance in achieving a more sustainable production model.
Integration with Emerging Technologies
The integration of plasma etching with emerging technologies is also crucial for future advancements. As industries evolve, the demand for more sophisticated and versatile etching solutions increases. The incorporation of artificial intelligence, machine learning, and automation can vastly improve the precision and efficiency of plasma etching processes.
Several integration efforts are ongoing, such as:
- Artificial Intelligence: AI can analyze data from etching processes, helping to optimize parameters like power and gas flow for better quality control and yield.
- Augmented Reality: AR tools can enhance operator training and maintenance, allowing for real-time insights into chamber performance and issues.
- Smart Manufacturing: The move towards Industry 4.0 emphasizes interconnected systems and processes. Integrating plasma etching into digitized manufacturing ecosystems can improve overall productivity and reduce operational risks.
As plasma etch technology continues to adapt to these trends, it holds the potential for substantial advancements in the quality and functionality of semiconductors, aligning with the demands of modern technology landscapes.
"The transition towards sustainable and integrated technologies within plasma etching is essential for the future of modern manufacturing."
Overall, the path ahead for plasma etching reveals a focus on not just technical improvements but also ethical responsibility and innovation. As these trends unfold, the implications for industries will be profound.
Culmination
The conclusion of this article consolidates the extensive exploration of plasma etch chambers and their multifaceted roles in modern technology. Plasma etching is not merely a technique; it is a cornerstone of semiconductor manufacturing and materials processing. Understanding this technology's principles and applications showcases its immense impact on various industries. The intricate balance of different operational parameters, like pressure, temperature, and gas composition, plays a crucial role in achieving desired outcomes in etching processes.
Summation of Key Points
- Core Mechanisms: The mechanisms of ion bombardment and chemical reactions are essential in effective material removal. Knowing these processes enhances the precision of etching in fabrication.
- Applications Across Fields: From semiconductor fabrication to microfabrication, the applications of plasma etch technology underline its versatility. Specific sectors that benefit include electronics, biology, and materials science.
- Challenges and Innovations: The challenges in selectivity, etch rate control, and material compatibility are ongoing concerns. However, advancements in chamber design and the integration of new technologies present pathways for resolving these issues.
- Future Trends: Attention to sustainability and the integration of emerging technologies highlight the future trajectory of plasma etching. These aspects suggest a roadmap for development in this crucial field.
Call for Continued Research
The advancement of plasma etch technology hinges on continuous research and development. As industries evolve, so should the methods and equipment used in plasma etching.
- Investigation into Selectivity: Further study is necessary to enhance selectivity between different materials. Innovations in gas compositions and chamber designs could yield significant breakthroughs.
- Exploration of Eco-Friendly Solutions: A stronger focus on sustainable practices, such as reducing gas emissions and energy consumption, is essential for long-term viability in manufacturing.
- Integrative Approaches: Research should encourage collaboration among disciplines, blending insights from physics, chemistry, and engineering to enhance plasma etch technologies.
Ultimately, the future of plasma etching is bright, provided there is a commitment to understanding and overcoming its inherent challenges. The ongoing journey not only promises improvements in semiconductor manufacturing but also ferments innovation across numerous scientific and industrial fields.