The Role of Mechanical Engineers in Mining
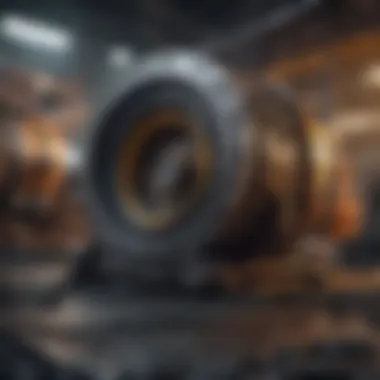
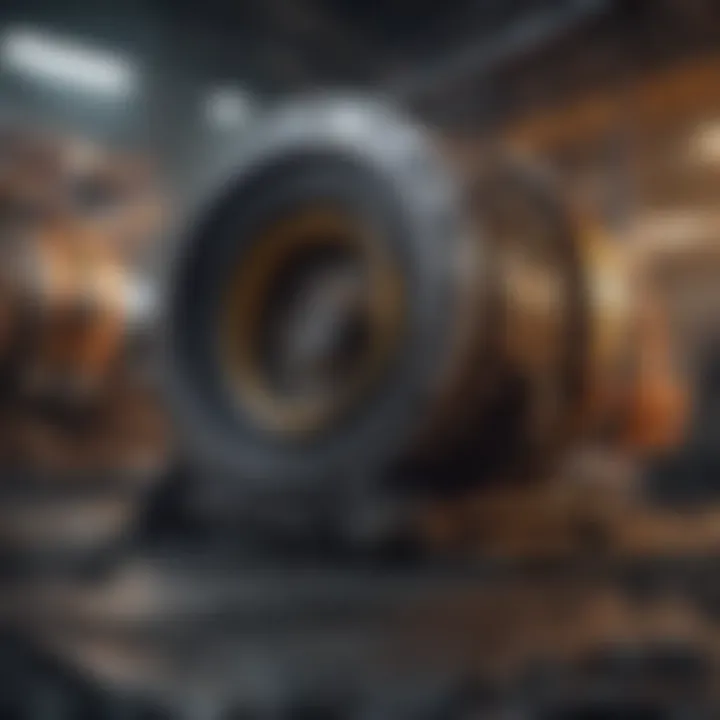
Intro
Mechanical engineers play a vital role in the mining industry. Their work influences every aspect, from equipment design to maintenance strategies, directly affecting efficiency and safety. As mining operations evolve, the need for innovation becomes increasingly important. Mechanical engineers bridge the gap between traditional engineering and modern technological advancements. This article provides insights into their crucial contributions and the challenges they face in this dynamic field.
Research Overview
A comprehensive understanding of mechanical engineering in mining involves examining various factors. We look at key areas such as equipment design, maintenance, and safety practices.
Summary of Key Findings
- Equipment Design: Mechanical engineers develop machines and tools necessary for mining operations. Their designs focus on durability and efficiency.
- Maintenance Strategies: Regular maintenance is critical to ensure equipment operates smoothly. Mechanical engineers implement strategies that minimize downtime and repair costs.
- Safety Protocols: Safety is paramount in the mining sector. Engineers design systems to protect workers and the environment.
Research Objectives and Hypotheses
The main objective of this research is to explore the multifaceted roles of mechanical engineers in mining. It investigates the following hypotheses:
- Mechanical engineers significantly enhance mining efficiency through innovative designs.
- Effective maintenance strategies developed by engineers reduce overall operational costs.
- Engineersβ contributions to safety protocols lead to fewer accidents in mines.
Methodology
Understanding the role of mechanical engineers involves a structured approach.
Study Design and Approach
This examination employs a mixed-method approach, incorporating both qualitative and quantitative data. We focus on case studies from various mining operations worldwide.
Data Collection Techniques
Data is collected through multiple channels:
- Interviews: Engaging with engineers provides firsthand insights into challenges and best practices.
- Surveys: Gathering surveys from mining companies helps quantify the impact of engineering innovations.
- Field Studies: Observing operations in real-time showcases the application of engineering principles.
"The integration of engineering and new technologies has revolutionized mining practices globally," says an industry expert.
These methodologies ensure a comprehensive view of mechanical engineering's role in enhancing mining processes. The insights derived from this research guide future strategies aimed at improving efficiency and safety in the mining industry.
Prelims to Mechanical Engineering in Mining
The intersection of mechanical engineering and the mining industry is a pivotal area that shapes the efficiency and safety of mining operations. This section introduces the essential roles mechanical engineers play in mining environments.
Understanding mechanical engineering in mining provides insights into how engineers enhance equipment functionality, improve safety measures, and streamline processes. Mechanical engineers apply principles of physics and material science to develop sophisticated machinery used in extracting minerals. By navigating power systems, structural analyses, and thermodynamics, these engineers ensure that mining operations are not only effective but also sustainable.
Investing in effectively trained mechanical engineers can lead to innovations that push the industry forward. They create equipment tailored to specific mining conditions, contributing directly to the operational success of a mining site. This focus on mechanical design not only improves efficiency but also reduces downtime, as well-designed machines require less maintenance.
Moreover, the collaboration of mechanical engineers with mining professionals fosters a multidisciplinary approach, optimizing processes that lead to safer work environments. Engineers contribute significantly to risk assessment and safety compliance, minimizing accidents through engineered solutions.
Overview of Mining Engineering
Mining engineering is a specialized field that combines principles of engineering, geology, and environmental science. It focuses on the extraction of minerals from the Earth efficiently and sustainably. Mining engineers are tasked with planning, designing, and overseeing the entire mining process. They also ensure compliance with health and safety regulations, highlighting the importance of careful project management.
Notably, the field encompasses various types of mining, such as underground, surface, and open-pit mining. Each method has unique challenges, and mechanical engineers are instrumental in developing and implementing suitable technologies that enable efficient extraction.
Key Responsibilities:
- Ensuring safety and compliance with regulations
- Planning and designing mining structures
- Developing advanced extraction techniques
- Assessing ore quality and environmental impact
Historical Development of Mining Engineering Disciplines
The evolution of mining engineering can be traced back thousands of years. Early mining efforts focused primarily on the extraction of precious metals and necessary minerals. With the Industrial Revolution in the 18th and 19th centuries, mining techniques advanced significantly. Innovations such as steam engines and mechanized tools transformed traditional methods, enhancing both productivity and safety.
As the demand for minerals increased during these eras, the engineering discipline evolved. Organizations began to recognize the necessity for specialized training programs. This led to the establishment of formal engineering education, where students learned the principles that govern extraction, structures, and processes.
In modern times, mining engineering has integrated more advanced technologies and methodologies. With the rise of automation, computer-aided design, and environmental considerations, the profession has continued to adapt to changing circumstances.
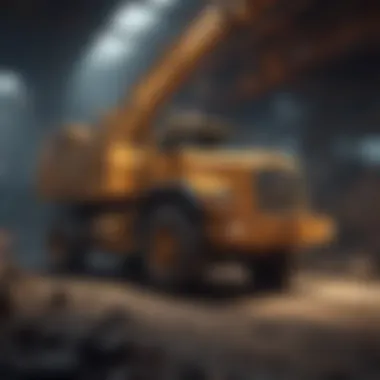
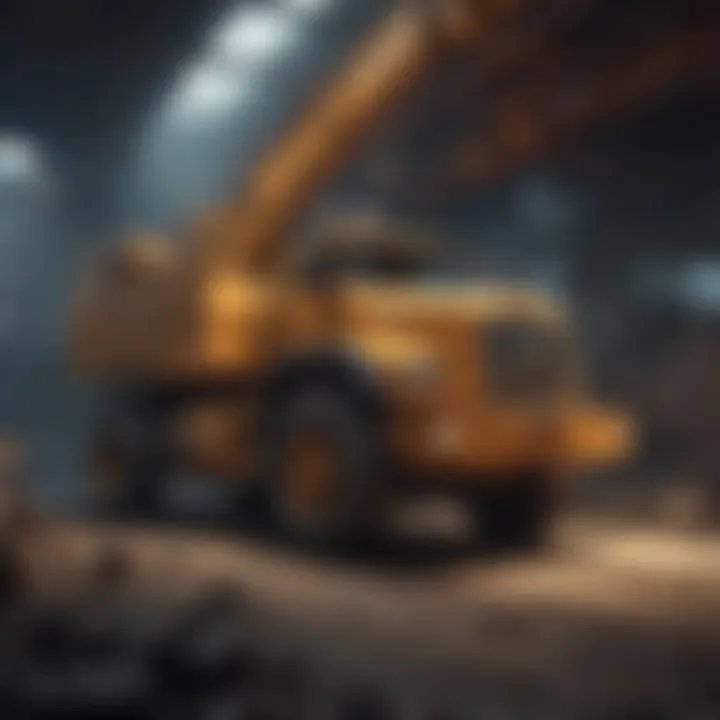
"The development of mining engineering disciplines reflects a continuous quest for improvement and adaptability in response to market needs and technological advancements."
Today, mechanical engineers within the mining sector play a crucial role in ensuring that the industry meets both economic and environmental challenges. Their skill sets have expanded to include knowledge in automation, data analytics, and sustainability practices, making them invaluable to modern mining operations.
Fundamental Principles of Mechanical Engineering
The domain of mechanical engineering offers a foundation critical to addressing the multifaceted demands of mining operations. Understanding the fundamental principles of this discipline is essential for mechanical engineers aiming to innovate and improve existing practices within mining. These principles are not merely academic; they translate into practical applications that enhance efficiency, safety, and sustainability in mining operations.
Core Mechanical Engineering Concepts
Mechanical engineering encompasses various concepts that shape the framework of practice in the mining industry. Among these, statics, dynamics, fluid mechanics, and thermodynamics stand out as key components. Each of these areas contributes to the design, operation, and maintenance of machinery and equipment found in mines.
- Statics deals with forces acting on stationary bodies, providing insights needed for structural integrity in equipment like cranes and excavators.
- Dynamics, on the other hand, encompasses the analysis of forces on moving bodies. This concept is paramount when designing machinery that operates under varying conditions, ensuring reliability and effective performance.
- Fluid mechanics is vital for understanding the behavior of liquids and gases in mining processes, influencing the design of pumps, pipes, and ventilation systems used in mines.
- Thermodynamics relates to energy transfer and heat, playing a significant role in processes such as mineral processing and heating systems used in mining industries.
Applying these core concepts can lead to significant advancements in equipment design and operational efficiency, which can ultimately contribute to cost reduction and increased productivity in mining activities.
Material Science in Mining Applications
Material science is another fundamental aspect of mechanical engineering, particularly relevant in mining due to the harsh environments encountered. This field studies the properties and applications of materials, impacting several areas such as equipment durability and safety.
- Engineers must understand the mechanical properties of materials that withstand extreme conditions. This includes the ability to resist wear, corrosion, and heat generated during mining operations.
- Advanced materials, such as high-strength alloys or composites, offer better performance and longevity in demanding mining environments. Engineers often select materials based on specific performance criteria relevant to their operational contexts.
- Sustainability in material selection is also key. Using materials that minimize environmental impact while ensuring safety and performance is becoming increasingly important in modern mining practices.
Adopting a material science perspective enables mechanical engineers to design equipment that is not only functional but also resilient, thus enhancing overall operational safety and efficiency.
"A deep understanding of material properties empowers engineers to make informed decisions, significantly impacting the efficacy of mining operations."
Key Responsibilities of Mechanical Engineers in Mining
Mechanical engineers play a pivotal role within the mining industry. Their responsibilities encompass various elements that are vital to the operational success and safety of mining activities. Each responsibility not only involves technical skills but also an understanding of the specific challenges miners face, as well as the need for innovative solutions. Below are the key areas where mechanical engineers exert their influence.
Equipment Design and Development
The design and development of mining equipment are at the forefront of a mechanical engineer's responsibilities. Engineers must ensure that the equipment meets rigorous operational standards while also considering the harsh environmental conditions prevalent in mining sites. They work on the following aspects:
- Innovative Designs: Developing new machinery or improving existing ones to enhance efficiency and productivity.
- Safety Standards: Ensuring all designs comply with safety regulations and practices. This includes stress analysis, durability testing, and ease of maintenance.
- Cost-Effectiveness: Designing equipment that reduces operational costs without compromising quality. This may involve selecting materials that are both lightweight and durable.
Maintenance and Reliability Engineering
Maintenance is another key area where mechanical engineers contribute significantly. The reliability of mining operations heavily relies on the maintenance routines instituted by these engineers. Important functions include:
- Preventive Maintenance: Establishing schedules and protocols to minimize downtime and extend equipment lifespan.
- Failure Analysis: Investigating equipment failures to determine root causes and implementing corrective actions.
- Reliability Programs: Developing comprehensive reliability strategies to optimize performance and prevent future equipment issues.
"The integrity of mining operations is largely determined by the efficiency of the mechanical engineering practices involved in equipment maintenance and reliability."
Process Optimization
Lastly, mechanical engineers are integral to process optimization within mining operations. Their focus is on streamlining operations and increasing productivity while reducing waste. The key strategies include:
- Workflow Assessment: Analyzing workflows to identify bottlenecks in production and suggesting improvements.
- Technology Integration: Implementing new technologies, such as automation and data analytics, to enhance operations.
- Resource Management: Ensuring that materials and human resources are utilized efficiently to avoid unnecessary expenditure or waste.
In summary, the role of mechanical engineers in mining is multifaceted, where they are challenged to balance innovative design, robust maintenance strategies, and optimized processing. Their contributions are essential for sustainable and efficient mining practices, driving both safety and operational success.
Technological Innovations Impacting Mining Engineering
The integration of technology within mining engineering is reshaping the landscape of the industry. These innovations provide numerous benefits, including enhanced efficiency, improved safety, and optimized resource management. As mechanical engineers adapt to these advancements, they are finding new ways to address both operational demands and sustainability goals. Embracing technological innovations is no longer optional; it is essential to remain competitive and effective in the mining sector.
Automation and Robotics in Mining
Automation plays a significant role in mining operations today. Implementing automated systems and robotics can streamline processes that are traditionally labor-intensive. For instance, automated drilling and hauling equipment reduces the need for human intervention in risky environments. This not only increases efficiency but also enhances worker safety by minimizing exposure to hazardous conditions.
Moreover, robotic solutions can operate in remote areas where human workers cannot or should not venture. By using drones for surveying and monitoring, mines can gather data quickly and accurately. The shift toward automation also allows for real-time data acquisition, informing immediate decision-making processes. Consequently, automation drastically reduces downtime and operational costs over time.
Advanced Material Technologies
Material science plays a crucial role in developing innovative solutions for mining. Advanced materials have improved the durability and efficiency of mining equipment. For instance, lightweight composites and high-strength steels result in machinery that is both strong and energy-efficient. These materials help improve performance while reducing the wear and tear associated with heavy mining operations.
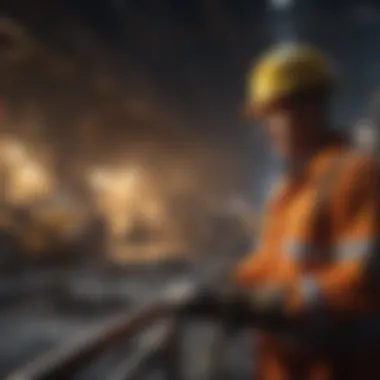
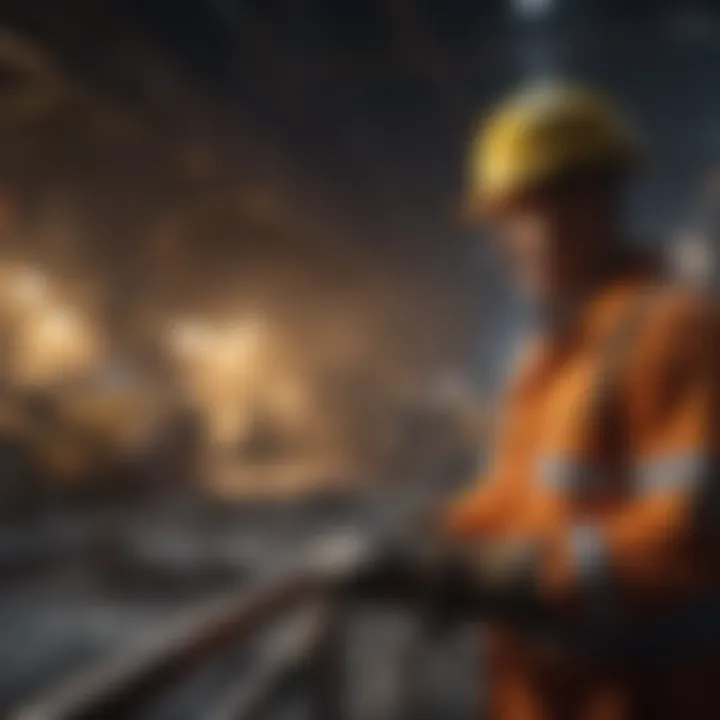
Furthermore, advancements in material technologies enable engineers to design equipment that withstands extreme conditions, such as high temperatures and corrosive environments. The lifecycle of machinery is extended, leading to cost savings in replacement and maintenance. Enhanced material technologies ensure that machinery meets operational demands while adhering to sustainability standards.
Data Analytics and Predictive Maintenance
The application of data analytics in mining engineering cannot be overstated. By collecting and analyzing data from equipment and operations, mechanical engineers can gain valuable insights into performance and efficiency. Predictive maintenance is one approach enabled by data analytics. Through monitoring machinery and predicting failures before they occur, companies can avoid costly downtimes.
This proactive approach relies on sensors and IoT technology to track equipment health in real-time. It shifts the maintenance strategy from reactive to predictive, allowing for scheduled repairs that do not disrupt operations. Optimizing maintenance schedules based on data analytics reduces costs and enhances overall operational efficiency. The effective use of data not only benefits individual mines but also contributes positively to the mining industry's environmental footprint by reducing waste and improving resource use.
Safety and Compliance in Mining Operations
Safety and compliance are integral pillars in the mining industry. The nature of mining work involves high-risk environments, where mechanical engineers play a significant role in ensuring that operations do not only run efficiently but safely. In this section, we will explore various aspects of safety measures implemented in mining operations and how compliance with regulations safeguards not just the workers but also the equipment and the environment.
One of the primary benefits of a robust safety and compliance framework is the reduction of accidents and injuries. These frameworks establish standard operating procedures that guide engineers and workers in identifying hazards and implementing corrective measures. Ensuring compliance with these standards not only protects personnel but also enhances the operational performance of the machinery and equipment. Striking a balance between safety protocols and operational efficiency is critical in maintaining productivity while safeguarding human lives.
Moreover, compliance is not just about following rules; it includes a commitment to continuous improvement and adaptation. The dynamic nature of the mining sector necessitates that mechanical engineers stay updated with changing regulations and industry best practices. This can often involve engaging in training programs and staying informed through professional associations and regulatory bodies. Such adherence to evolving standards demonstrates a companyβs dedication to its workforce and builds trust within the community.
βA safe workplace is not only a right, but it can also increase operational efficiency and productivity.β
Regulatory Frameworks Governing Mining Safety
Several regulatory frameworks govern the safety standards within the mining industry. Key among these is the Occupational Safety and Health Administration (OSHA) in the United States. OSHA sets forth regulations that cover nearly every aspect of mining safety, from operation procedures to emergency response protocols. Mechanical engineers must familiarize themselves with these guidelines to ensure that their designs and practices align with statutory requirements.
Compliance with the Mine Safety and Health Administration (MSHA) is equally crucial. MSHA oversees the safety of mining operations in the United States, focusing on preventing accidents and occupational illnesses. Mechanical engineers often work hand-in-hand with safety officers to ensure mining equipment meets MSHAβs rigorous safety standards. This involves regular inspections, maintenance protocols, and the integration of safety technologies into design processes to mitigate risks.
In other countries, bodies such as the Health and Safety Executive (HSE) in the UK and similar organizations globally enforce their own regulations. Mechanical engineers must assess local laws comprehensively, consider the implications these regulations have on design and operational processes, and adapt to each regulatory environment accordingly.
Risk Management Strategies
Risk management is a critical element in mining operations, and mechanical engineers implement strategies to identify, assess, and mitigate risks. The process begins with conducting thorough risk assessments prior to commencing any project. This involves analyzing potential hazards associated with machinery, operational procedures, and environmental factors. By identifying these risks early on, engineers can develop strategies to minimize or eliminate them altogether, fostering a culture of safety.
Effective risk management also requires regular monitoring and auditing of safety practices and equipment performance. With advances in data analytics, mechanical engineers can utilize predictive maintenance strategies to foresee potential failures before they occur. This proactive approach reduces downtime, prolongs equipment life, and ensures a safer working environment.
Moreover, creating safety training programs is essential. These programs equip workers with the knowledge and skills required to operate heavy machinery safely and respond effectively during emergencies. Encouraging open communication and reporting of unsafe practices ensures that all personnel feel empowered to contribute to a safer worksite.
Environmental Considerations and Sustainability
The importance of environmental considerations and sustainability in mining cannot be overstated. As societies become more aware of the environmental repercussions of resource extraction, professionals in the mining industry, particularly mechanical engineers, are challenged to adopt more sustainable practices. This section outlines the need for engineers to incorporate sustainability into their operations and highlights various aspects of this issue.
Sustainable Mining Practices
Sustainable mining practices prioritize the stewardship of resources while minimizing the impacts on the environment. Mechanical engineers play a pivotal role in this transformation. They are involved in several initiatives such as:
- Efficient resource utilization: Engineers design equipment that conserves energy and reduces material waste. This can include optimizing the dimensions and operation of machinery to lower energy consumption.
- Recycling and waste management: Implementing systems for recycling materials and managing waste effectively is crucial. Mechanical engineers can develop processes that reduce waste production and enhance recycling capabilities within mining operations.
- Use of alternative energy: The mining industry is gradually shifting towards renewable energy sources, like solar and wind, to power operations. Mechanical engineers must adapt technologies to harness these resources effectively.
- Innovative extraction technologies: New extraction methods, such as in-situ leaching, may offer environmentally friendly alternatives to traditional mining techniques. Mechanical engineers facilitate the design and implementation of these methods to minimize ecological disruptions.
These practices contribute to sustainability goals while ensuring operational productivity and safety.
Impact of Mining on Ecosystems
Mining activities can significantly alter ecosystems, presenting both challenges and opportunities for mechanical engineers. Understanding the environmental impact is crucial.
- Habitat destruction: Surface mining often leads to habitat loss and fragmentation. Mechanical engineers must consider these effects when designing equipment and mining processes to mitigate disturbances.
- Water pollution: Mining operations can contaminate local water sources through the runoff of chemicals. Engineers need to integrate systems for water treatment and protection into their designs, ensuring that water bodies remain unaffected.
- Soil degradation: The removal of vegetation and soil can lead to erosion and loss of soil nutrients. Mechanical engineers must explore ways to restore soil health, possibly through the incorporation of vegetation and controlled land use practices.
"Sustainable practices in mining not only protect biodiversity but also sustain long-term mineral supply, essential for global development."
Understanding the impact of mining on ecosystems helps shape responsible practices that protect environment while still enabling the necessary extraction of resources.
Education and Skills Development for Aspiring Engineers
Education plays a crucial role in shaping the future of mechanical engineers in the mining sector. It equips individuals with the theoretical knowledge and practical skills necessary to thrive in a complex and evolving industry. Aspiring engineers must prioritize their educational journey, ensuring they have a strong foundation in both engineering principles and mining practices. This section addresses the significance of relevant academic pathways and the essential skills needed to succeed.
Relevant Academic Pathways
Several academic pathways lead to a career in mining engineering. A bachelorβs degree in mechanical engineering is typically the first step. Universities often offer specialized programs tailored to the mining sector. Some examples include:
- Mining Engineering: Focuses on extracting resources efficiently and safely.
- Mechanical Engineering: Covers principles applicable in mining machinery and equipment.
- Materials Science: Examines the properties of materials used in mining constructs.
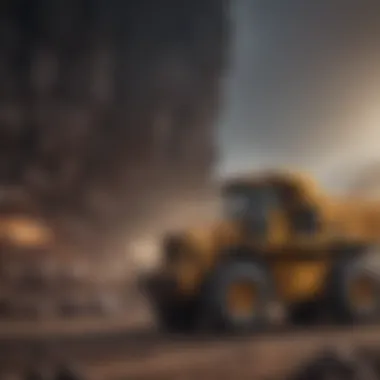
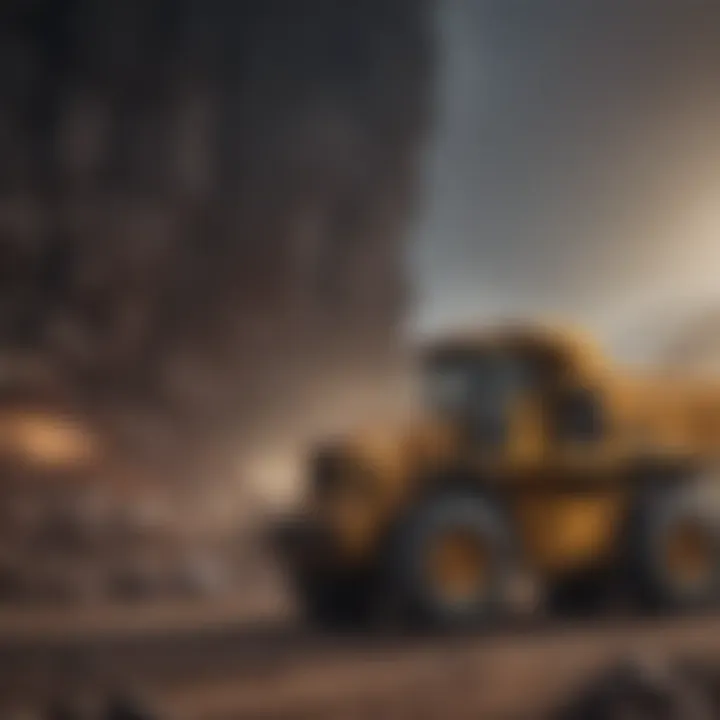
Graduate degrees can further enhance job prospects. Masterβs programs in mining engineering or business management with a focus on mining can cultivate leadership skills. Internships during educational training provide practical experience that employers value highly. Employers look favorably on candidates demonstrating hands-on understanding of mining operations.
Keys Skills for Success in Mining Engineering
Beyond formal education, certain skills are paramount for mechanical engineers in mining:
- Technical Proficiency: Engineers must understand machinery dynamics and processes. This skill also encompasses proficiency in industry-specific software tools.
- Problem-Solving Abilities: They often need to troubleshoot issues in real-time and offer effective solutions.
- Communication Skills: Collaborating with multi-disciplinary teams requires clear and precise communication, especially in safety-critical environments.
- Analytical Thinking: Engineers must interpret data to optimize processes and ensure compliance with safety regulations.
- Adaptability: The mining sector is influenced by various external factors; therefore, engineers must quickly adapt to changing technologies and methodologies.
"Education is the most powerful weapon which you can use to change the world."
This quote underlines the significance of education, especially in a field as vital as mining. A strong educational background paired with the right skills can facilitate career advancement and contribute to the industry's overall success.
Challenges Facing Mechanical Engineers in Mining
The mining sector is complex and continuously evolving, presenting several challenges for mechanical engineers. Understanding these challenges is critical for multiple reasons. Firstly, acknowledging the obstacles faced by engineers allows for the development of effective strategies to mitigate them. This not only enhances productivity but also ensures a safer and more sustainable mining operation. Moreover, addressing these challenges is vital for the advancement of technology and systems within mining, benefiting the sector as a whole.
Economic Pressures and Volatility
Economic pressures significantly impact the mining industry, influencing decisions at every level of operation. Fluctuations in commodity prices create an environment of uncertainty, often leading to project delays and budget cuts. Mechanical engineers must navigate this landscape by finding cost-effective solutions to equipment design and maintenance. The ability to adapt quickly while still ensuring the reliability of machinery is crucial.
In periods of low prices, companies may prioritize immediate cost savings over long-term investments in innovation. This can result in a stagnant technological environment, with older systems remaining in operation longer than ideal. Engineers often find themselves tasked with extending the lifecycle of existing equipment, necessitating a deeper understanding of both mechanical systems and economic forecasting.
Moreover, resource allocation becomes constrained, leading to potential compromises in safety and operational efficiency. The balance between cost-cutting measures and necessary expenditures for safety equipment and maintenance can create ethical dilemmas. Mechanical engineers play a vital role in advocating for robust safety features, even amidst financial pressures.
Technological Adaptation Challenges
With technology advancing rapidly, mechanical engineers are tasked with integrating these innovations into existing mining operations. However, this adaptation is not without its challenges. The gap between cutting-edge technology and current systems can be substantial. Engineers need to assess the compatibility of new technologies with older equipment, which can be complex and costly.
Training personnel is another significant challenge. As new machinery and systems are introduced, there is often a steep learning curve involved. Mechanical engineers are pivotal in developing training programs that ensure all team members are skilled and knowledgeable about new technologies. Failure to do so may result in accidents, inefficiencies, or the inability to fully exploit the capabilities of new machinery.
Additionally, resistance to change is a common barrier. Staff may be accustomed to certain procedures and wary of altering methods that could potentially disrupt workflow. It is the engineer's responsibility to demonstrate the benefits of new technologies through data-driven analysis, showcasing how these tools can improve safety and productivity.
Global Supply Chain Disruptions
The interconnected nature of the global supply chain presents unique challenges for mechanical engineers in mining. Factors such as political instability, natural disasters, and a pandemic can all disrupt the flow of essential materials and parts required for mining operations. When supply chains are disrupted, engineers must develop contingency plans to ensure that projects do not halt, which could result in lost revenue and productivity.
Stockpiling essential components becomes a practical solution during uncertain times, but it also requires careful economic forecasting to avoid excess inventory. Mechanical engineers must work closely with supply chain specialists to assess risks and develop strategies for sourcing critical parts from alternative suppliers or regions. This task demands not only mechanical expertise but also a strong grasp of global economics.
Moreover, delays in obtaining equipment can push back project timelines, necessitating adjustments in project management. Engineers are often called upon to propose alternate solutions to mitigate delays, which requires innovative thinking and an understanding of both engineering and operational strategy.
Ultimately, the challenges faced by mechanical engineers in the mining industry highlight the crucial interplay between technology, safety, and economic considerations. Acknowledging and addressing these issues is key to advancing the sector.
Future Trends in Mining Engineering
The future of mining engineering hinges on the adoption of innovative technologies and sustainable practices. As the global demand for minerals and resources increases, mechanical engineers must adapt to new challenges and opportunities. This section explores the emerging technologies shaping the industry, the role of artificial intelligence, and the evolving strategies for resource management.
Emerging Technologies and Their Impact
Technological advancements are transforming the mining sector. Innovations are streamlining operations, enhancing safety, and increasing efficiency. For instance, techniques such as drone technology, geospatial mapping, and 3D printing are gaining traction.
- Drones provide real-time data for monitoring and surveying mining sites. This reduces the need for manual inspections, minimizing risks.
- Geospatial mapping allows for precise resource estimation, leading to better project planning.
- 3D printing is emerging as a method for creating parts and tools directly on-site, reducing downtime.
Mechanical engineers must stay abreast of these trends to leverage their benefits effectively. By integrating such technologies, mines can operate more economically and sustainably.
The Role of Artificial Intelligence
Artificial intelligence (AI) is a game-changer in mining engineering. It offers numerous applications, from predictive maintenance to autonomous machinery.
- Predictive maintenance utilizes AI algorithms to analyze equipment data. This can forecast failures before they occur, reducing unexpected downtimes.
- Autonomous mining vehicles enhance safety by reducing human intervention in hazardous environments. These vehicles can operate continuously without fatigue, leading to increased productivity.
Understanding and implementing AI effectively can position mechanical engineers as leaders in the field. The benefits extend beyond productivity; they contribute to safer and more efficient mining practices.
Future of Resource Management
Resource management is critical for the sustainability of the mining industry. As resources become scarcer, engineers must focus on optimizing their use.
- Recycling and reusing materials is essential. Mechanical engineers can design processes that recover valuable elements from waste streams.
- Resource efficiency involves using less energy and water in mining processes. Innovations in machine design, including more efficient engines and systems, can contribute to this goal.
"Innovation is not the product of logical thought, but of imaginative thought." - Albert Einstein
Engagement with these trends will require continuous learning and adaptation. As technology evolves, so too must the skill set and approach of the mechanical engineers working within the mining sector.