Corrosion Monitoring Systems for Metal: Techniques and Applications
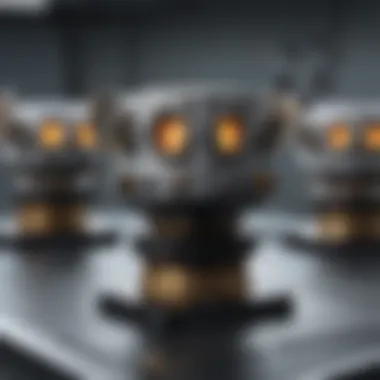
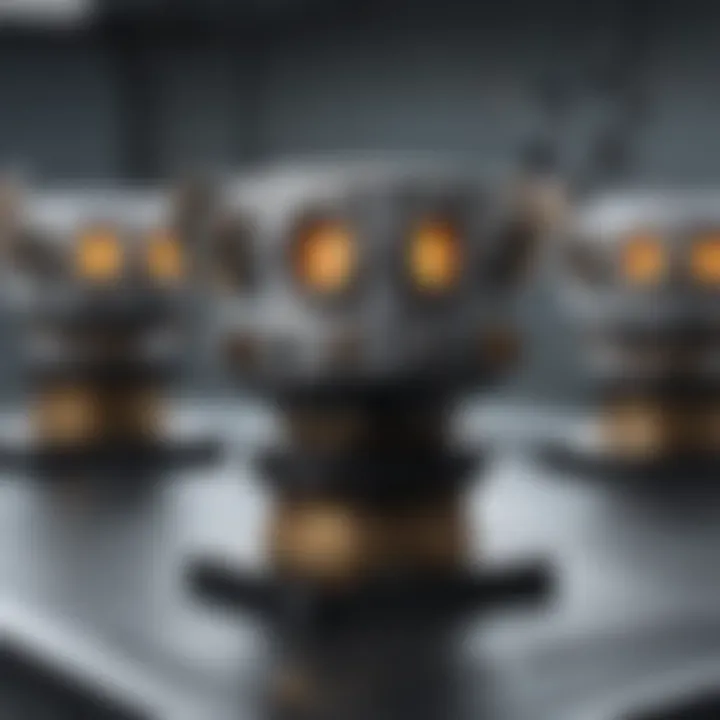
Intro
Corrosion is a pervasive issue that affects countless industries, ranging from oil and gas to construction. With metal structures being the backbone of much of our modern infrastructure, understanding how to monitor and manage corrosion is crucial. Corrosion monitoring systems offer valuable insights, allowing stakeholders to assess and mitigate the risks associated with material degradation.
In this article, we will explore the various techniques and applications of corrosion monitoring systems specifically designed for metal samples. Weβll delve into the methods employed to evaluate corrosion processes, discuss the types of sensors available, and examine the significance of continuous monitoring in industries that depend on the durability of metal structures. Furthermore, we will review traditional approaches alongside emerging technologies, highlighting how advancements in data analytics are transforming corrosion management strategies.
Through this comprehensive overview, students, researchers, and professionals engaged in scientific and industrial fields will gain a deeper understanding of effective corrosion management and the importance of integrating new methodologies for enhanced accuracy in monitoring.
Prelims to Corrosion Monitoring
Corrosion monitoring is an essential aspect of maintaining the integrity of metal structures across various industries. It acts as an early-warning system, alerting to the presence of corrosion and potentially saving significant costs from repairs and replacements. By integrating advanced monitoring techniques, organizations can mitigate risks associated with corrosion and make informed maintenance decisions. The significance of corrosion monitoring becomes more pronounced when considering that it can prolong the lifespan of equipment, improve safety standards, and ultimately enhance productivity in sectors ranging from oil and gas to infrastructure.
Understanding Corrosion
To grasp the necessity of monitoring systems, one must first comprehend what corrosion really is. At its core, corrosion is the gradual degradation of materials, primarily metals, caused by chemical reactions in their environment. This process can occur in various forms, such as rusting of iron, oxidation of aluminum, and even the degradation of protective coatings. Itβs like a slow poison that eats away at the metal, often going unnoticed until it reaches a critical point. Factors contributing to corrosion include moisture, temperature, acidity, and the presence of salts or other chemicals.
A classic example is a shipβs hull being exposed to seawater; the constant interaction with saltwater leads to galvanic corrosion, which can result in severe structural failures if not monitored actively. Thus, understanding corrosion in its various forms is not just vital for academic purposes but also for practical applications that directly impact industries reliant on ferrous and non-ferrous metals.
Importance of Monitoring Corrosion
Monitoring corrosion is not merely a good practice; itβs a necessity, especially in environments that pose heightened risks. The older adage, "an ounce of prevention is worth a pound of cure," rings true in this context. Early detection of corrosion can avert disastersβboth environmental and economic. Additionally, it enables targeted maintenance activities, thereby minimizing downtime and extending the lifespan of assets.
Several key benefits arise from rigorous corrosion monitoring:
- Safety Assurance: Regular monitoring can identify potential failure points, significantly reducing accidents and injuries.
- Cost Efficiency: By preventing corrosion damage, organizations can save on extensive repair costs or even replacement of metal components.
- Regulatory Compliance: Many industries are under stringent regulations regarding material integrity. Effective monitoring helps meet these requirements.
- Sustainability: Ensuring that materials have longer life cycles contributes positively to environmental conservation by reducing waste.
Scope of the Article
In this article, we aim to provide an in-depth look at corrosion monitoring systems for metal samples. We will explore various techniques employed in corrosion assessment, ranging from classic methods to cutting-edge technologies. The article will also delve into data analytics' role in interpreting the data gathered from monitoring systems, which is crucial for decision-making processes.
Our discussion will cover important aspects like:
- Types of corrosion and how they affect materials.
- Various monitoring techniques, including electrochemical methods and visual inspections.
- Advances in sensor technologies and their application.
- The interplay between data analytics and corrosion monitoring.
- Industry regulations to ensure safe practices.
By the end of this article, readers will have a comprehensive understanding of corrosion monitoring systems and their importance in modern applications.
"Corrosion doesnβt sleep, and neither should your monitoring systems." - Anonymous
Types of Corrosion
Corrosion is not a one-size-fits-all phenomenon. Understanding the different types of corrosion is crucial for anyone involved in metal work, engineering, or maintenance. Each type showcases unique characteristics and mechanisms that can significantly impact the lifespan and integrity of metal structures. Not only does identifying these types help in monitoring and prevention, but it also enables industries to tailor their prevention strategies effectively. In this section, we will examine four prominent types of corrosion: galvanic corrosion, pitting corrosion, stress corrosion cracking, and uniform corrosion.
Galvanic Corrosion
Galvanic corrosion occurs when two dissimilar metals come into contact in the presence of an electrolyte. This electrical connection can create a corrosion cell where one metal acts as an anode and the other as a cathode. For example, if copper and aluminum are paired in a moist environment, the aluminum often deteriorates faster due to its potential difference.
Benefits of Understanding Galvanic Corrosion:
- Allows for better material selection
- Guides the design of protective coatings
- Helps in the installation of electrical components
When working in environments where different metals are used, it becomes imperative to implement insulation techniques or employ sacrificial anodes to protect vulnerable metals. This type of corrosion stands as a reminder of how electrical and physical interactions can wreak havoc if not monitored.
Pitting Corrosion
Pitting corrosion is often dubbed "localized corrosion" because it leads to small pits or holes in metals, which can be extremely destructive yet hard to detect. This type often affects stainless steel and aluminum, where certain environmental conditions, such as chloride presence, may exacerbate the corrosion process.
Pitting can be likened to a silent assassin; it goes undetected for long periods while it quietly erodes the metal from within.
Considerations for Pitting Corrosion:
- Regular monitoring is essential
- Corrosion-resistant alloys may be required
- Understanding the environment is key in prevention
Stress Corrosion Cracking
Stress corrosion cracking (SCC) arises from a combination of tensile stress and a corrosive environment. Itβs especially prevalent in high-strength alloys like titanium and certain stainless steels. This can be quite a complex form of corrosion to predict and manage, as it can lead to sudden failure of components without observable signs of wear.
"Stress corrosion cracking is often a ticking time bomb that engineers must defuse with proactive measures."
Key Elements to Monitor for SCC:
- Environmental conditions like temperature and humidity
- Mechanical stresses in components
- Choice of alloy and material composition
Uniform Corrosion
Uniform corrosion is perhaps the most predictable and recognizable form of corrosion. Here, the metal deteriorates evenly over its surface, making it easier to anticipate loss in material thickness. Common in carbon steels and iron, factors such as exposure to oxygen, moisture, and pollutants contribute to this type of corrosion.
Considerations for Uniform Corrosion:
- Regular maintenance and monitoring can greatly reduce impact
- Coatings or inhibitors can be effective preventive measures
- Systematic inspections can help determine wear over time
A straightforward approach to managing uniform corrosion often involves routine checks, making it less daunting compared to more insidious forms like pitting and SCC.
Understanding these types of corrosion helps in deploying the appropriate monitoring systems and mitigation strategies. By knowing the enemy, we can better act to protect our metal structures.

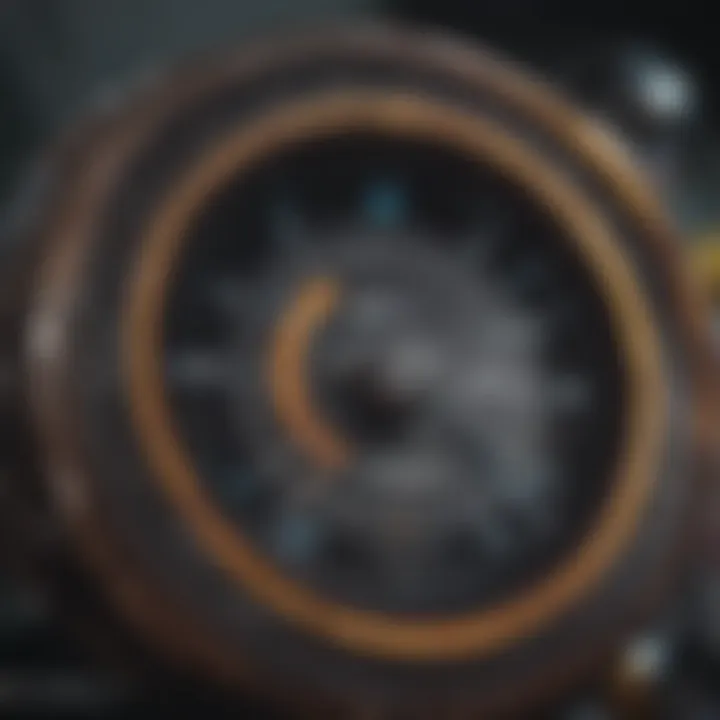
Corrosion Monitoring Techniques
Corrosion monitoring techniques serve as a cornerstone for the preservation of metal assets across various industries. These methodologies aim to preemptively identify and evaluate the corrosion processes that can lead to significant structural failures, financial losses, and safety hazards. In a world where reliance on metal structures is ubiquitous, the importance of these monitoring strategies cannot be overstated. Implementing more comprehensive corrosion monitoring practices allows organizations to maximize the lifespan of materials, ensure safety, and ultimately save costs.
Electrochemical Techniques
Electrochemical methods offer a remarkable way to evaluate corrosion dynamics in metal samples. They provide both real-time data and an extensive understanding of the electrochemical reactions at play. Let's delve into some specific electrochemical techniques:
Potentiodynamic Polarization
Potentiodynamic polarization is a hallmark in corrosion monitoring due to its ability to swiftly provide insights into the electrochemical behavior of metals. By gradually changing the electrode potential and observing the resultant current, one can generate an anodic or cathodic polarization curve. The key characteristic of this technique is its ability to determine the corrosion rate and identify passivation behavior of metals. It is popular among researchers due to its relatively straightforward methodology and quick results.
Advantages:
- Provides rapid results
- Can identify pitting corrosion and other localized corrosion types
- Allows for the evaluation of protective coatings
Disadvantages:
- Requires specialized equipment and skills
- Some intricacies in data interpretation may arise
Electrochemical Impedance Spectroscopy
Electrochemical impedance spectroscopy (EIS) explores the response of a corroding system to an alternating current, providing an intricate view of electrochemical processes. This technique stands out because it enables the examination of corrosion at different frequencies. A unique feature of EIS is that it can characterize the electrochemical processes without needing to immerse the metal fully, offering flexibility in settings where immersion is unfeasible.
Advantages:
- High sensitivity to changes in corrosion processes
- Non-destructive evaluation method
- Applicable in complex environments
Disadvantages:
- Complex data analysis required
- Can be time-consuming compared to other methods
Linear Polarization Resistance
Linear polarization resistance (LPR) is yet another pivotal electrochemical technique frequently used in corrosion monitoring. It involves measuring the current response to small changes in applied voltage, allowing for the calculation of the corrosion rate. One key characteristic of LPR is its simplicity and effectiveness for routine assessments, making it a favorable choice within various industries.
Advantages:
- Relatively quick and easy to perform
- Requires less sophisticated equipment than other methods
- Direct correlation to corrosion rate
Disadvantages:
- Less accurate for very high or very low corrosion rates
- Potential interference from various factors can complicate results
Visual Inspection and Nondestructive Testing
Visual inspection remains one of the most fundamental methods of corrosion monitoring despite technological advancements. With a trained eye, experienced personnel can identify early signs of corrosion, such as discoloration or surface irregularities. Coupled with nondestructive testing techniques such as ultrasonic testing, this method gains considerable value. These techniques together provide real-time feedback and can facilitate more targeted interventions, thus preventing serious damage before it becomes apparent.
Integrated Sensor Systems
Integrated sensor systems leverage multiple sensor types working harmoniously to provide comprehensive corrosion monitoring solutions. They combine various monitoring methodsβlike electrochemical techniques and visual inspectionsβinto a unified system that offers a broader perspective on the corrosion state of metal samples. These systems often come equipped with data analytics capabilities, enabling personnel to make data-driven decisions regarding maintenance and interventions, which promotes overall safety and efficiency in managing metallic structures.
Advances in Corrosion Sensors
Understanding the nuances of corrosion monitoring brings a wealth of benefits to industries reliant on metal structures. The advancement of corrosion sensors has been a game-changer, offering enhanced precision and efficacy. New technologies are constantly pushing the boundaries of what's possible, providing deeper insights and accelerating responses to corrosion challenges. These advancements not only help in preventing catastrophic failures but also in making informed decisions about maintenance and replacements.
Smart Sensors
Smart sensors are at the forefront of corrosion monitoring systems, representing a significant leap from traditional methods. These devices utilize intricate algorithms and connectivity features to offer real-time data regarding metal integrity.
- Key Benefits:
- Real-Time Monitoring: Constant data availability ensures timely interventions.
- Data Analytics Integration: Built-in analytics capabilities help in predictive modeling.
- Self-Calibration: Many smart sensors can adjust their parameters automatically, ensuring accuracy over time.
A prime example of such a sensor is the one used in a petrochemical facility, which constantly monitors the condition of pipelines subjected to corrosive environments. The data gathered helps engineers to implement maintenance only when necessary rather than adhering to rigid schedules. This represents both time-saving and cost-effective measures.
Wireless Monitoring Systems
The leap to wireless monitoring systems has transformed how corrosion assessments occur. Gone are the days when technicians had to be physically present at each monitoring site, often in challenging locations.
- Advantages of Wireless Systems:
- Remote Access: Data can be accessed from any location, which simplifies monitoring across geographically dispersed assets.
- Reduced Installation Costs: Without the need for extensive wiring, planning and implementation can be quicker and more economical.
- Scalability: New sensors can be added to the existing system without significant overhaul.
For instance, marine environments can be monitored through these wireless approaches, enabling data collection from submerged structures without risking human safety. By remotely analyzing data, stakeholders gain faster insights and can respond to emerging corrosion issues efficiently.
Nano-Sensor Technologies
Nano-sensor technologies represent the cutting edge of corrosion monitoring, utilizing materials and techniques at the nanoscale to achieve impressive sensitivity and specificity. These sensors can detect even minute changes in the corrosive environment.
- Key Features:
- High Sensitivity: Capable of detecting low concentrations of corrosive agents.
- Small Size: Enables integration into tight spaces where traditional sensors cannot fit.
- Versatility: Can be designed for various environments, from industrial applications to delicate frameworks in aerospace.
In practical terms, a nano-sensor could be embedded in a critical component of an aircraft, continuously monitoring for signs of corrosion. The ability to detect problems before they escalate is invaluable in fields where safety is paramount. This technology highlights how the integration of advanced materials can lead to safer and more reliable metal structures.
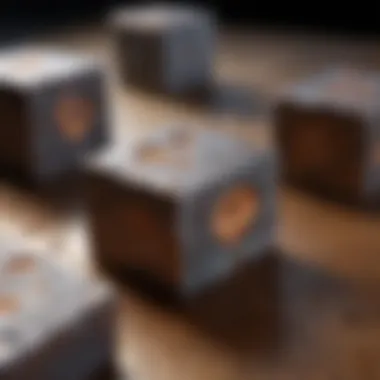
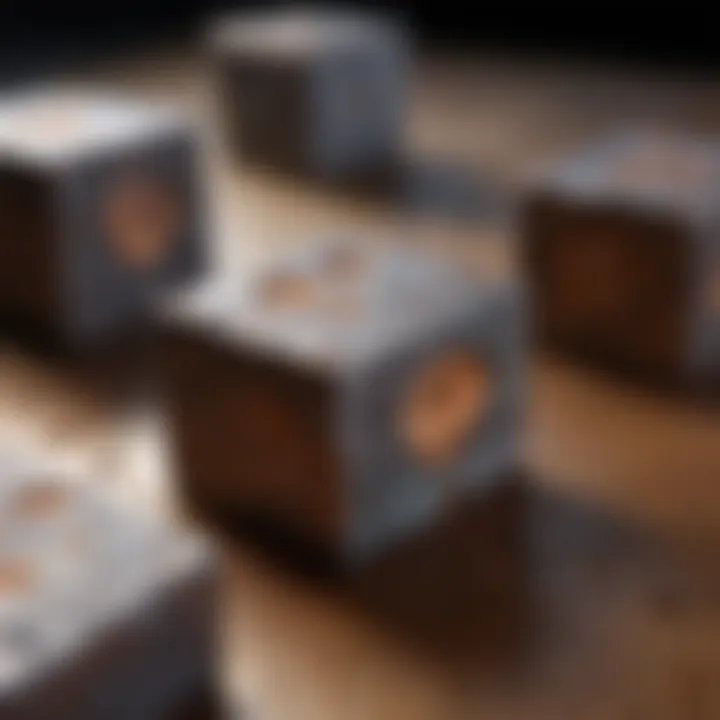
"With the emergence of smarter, faster, and more reliable corrosion sensors, industries are better equipped to face the complex challenges of corrosion, ensuring smooth operations and safety across sectors."
The convergence of these advancements in sensor technology significantly influences the effectiveness of corrosion management strategies, reducing downtime and conserving resources. As industries continue to innovate and adapt, the implications of these developments might well reshape preventive maintenance landscapes.
Role of Data Analytics in Corrosion Monitoring
In the realm of corrosion monitoring for metal samples, the integration of data analytics plays a critical role. By harnessing the power of sophisticated algorithms and computational methodologies, professionals can convert raw data into valuable insights. This not only aids in the timely detection of corrosion but also enhances predictive capabilities, allowing for improved decision-making across various industries. The importance of this topic cannot be overstated as it directly connects technological advancements to effective corrosion management strategies.
Data analytics adds a layer of intelligence to corrosion monitoring systems, enabling operators to identify trends and patterns that may otherwise go unnoticed. This capacity for deep analysis leads to better resource allocation, reduced downtime, and ultimately cost savings. Moreover, as industries strive for sustainability and efficiency, the application of data analytics stands as a beacon of improvement in managing metal integrity issues.
Data Collection Methods
For effective data analytics, the first step is marrying a variety of data collection methods. These methods ensure that the inputs are diverse and representative of the corrosion environment. Commonly employed methods include:
- Sensor Data: Utilizing electrochemical sensors or corrosion probes that can provide real-time data on corrosion rates.
- Environmental Monitoring: Collecting data on temperature, humidity, and electrolyte composition in the vicinity of metal samples.
- Historical Data: Gathering previous monitoring logs and maintenance records to analyze past corrosion trends.
- Visual Inspections: Documenting the visual condition of metal structures can enrich the dataset available for analysis.
By combining these diverse sources of information, professionals are able to craft a more comprehensive view of corrosion dynamics and its influencing factors.
Analyzing Corrosion Data
Once data is collected, the next crucial phase is analysis. This stage involves:
- Statistical Analysis: Employing statistical techniques to sift through the data for patterns, anomalies, and correlations.
- Visualizations: Creating graphs and charts that make it easier to interpret complex data sets and quickly convey findings.
- Machine Learning Models: Implementing machine learning algorithms that can predict corrosion trends based on historical and real-time data.
- Simulation Tools: Using computational models to simulate corrosion processes under various conditions, further enhancing understanding.
As a result, the synergy between data collection and rigorous analysis yields insights that not only indicate the state of the metal but also forecast potential future corrosion events.
Predictive Maintenance Strategies
The end goal of integrating data analytics into corrosion monitoring is to develop robust predictive maintenance strategies. This includes:
- Scheduled Maintenance vs. Condition Based Maintenance: Moving away from rigid schedules to flexible maintenance plans based on actual conditions.
- Risk Assessment: Identifying which assets are at the highest risk of failure and requiring immediate attention.
- Feedback Loops: Setting up systems that permit ongoing learning and adaptation of monitoring systems based on new data.
- Resource Optimization: Ensuring that maintenance teams focus their efforts where theyβre most needed, preventing waste of manpower and materials.
"Data analytics transforms passive corrosion management into a proactive approach, safeguarding both infrastructure and resources."
The future of corrosion management hinges on these predictive methodologies, allowing industrial players to mitigate risks proactively rather than reactively. By transforming the understanding of corrosion processes into actionable insights, the role of data analytics represents a significant leap forward in the field of corrosion monitoring.
Regulatory Standards and Compliance
Corrosion monitoring is not merely a technical task; it exists within a framework of standards and regulations that guide practices in different industries. Understanding these regulatory standards and compliance is essential for anyone involved in the design, implementation, and maintenance of corrosion monitoring systems. Failure to align with such standards can lead to dire consequences, from increased costs caused by premature equipment failures to catastrophic safety incidents. Hence, keeping up-to-date with regulations is paramount.
International Standards for Corrosion Monitoring
The international community has developed a set of comprehensives standards aiming to harmonize corrosion monitoring practices worldwide. Institutions such as ISO (International Organization for Standardization) and ASTM (American Society for Testing and Materials) have established guidelines that define best practices for evaluating and managing corrosion risks.
These standards provide clear methodologies for measuring corrosion rates, conducting inspections, and utilizing materials suitable for specific environments. For instance, ISO 8501 outlines the preparation of steel substrates before coating, ensuring that the surface is adequately free from contaminants that facilitate corrosion.
Furthermore, adhering to international standards offers several key benefits:
- Consistency: Enables a uniform approach to corrosion monitoring across various geographical regions, facilitating collaboration.
- Credibility: Enhancing the trustworthiness of results, making it easier to communicate findings to stakeholders.
- Efficiency: Streamlining processes through established procedures, reducing time and resource expenditure.
Overall, incorporating international standards into corrosion monitoring not only benefits individual organizations but also promotes safety and sustainability on a broader scale.
Industry Compliance Requirements
Each industry has its unique set of compliance requirements, shaped by regulatory bodies and specific operational risks related to corrosion. For example, industries such as oil and gas, construction, and maritime have stringent regulations in place due to the potential impact of corrosion on safety and asset longevity.
Consider the oil and gas sector, which is governed by standards from organizations like the API (American Petroleum Institute) and NACE International. These standards dictate regular monitoring of pipeline integrity, ensuring that operators take proactive steps in corrosion management. Non-compliance can lead to significant repercussions, including heavy fines, legal actions, and environmental disasters.
Essential compliance aspects include:
- Monitoring Frequency: Many industries dictate how often corrosion inspections and evaluations must occur.
- Reporting Requirements: Documentation must be maintained to demonstrate adherence to compliance, which may include detailed reports on monitoring findings and corrective actions taken.
- Material Specifications: Use of certified materials that can withstand corrosive environments is often a compliance requirement. This can mean sourcing from minimal compliant suppliers or undergoing rigorous material testing.
Compliance with these requirements not only helps in mitigating risks but also fosters a culture of accountability and continuous improvement. By taking these measures, organizations can navigate not only regulatory landscapes but also ensure the integrity and safety of their assets.
Applications of Corrosion Monitoring Systems
Understanding the applications of corrosion monitoring systems is crucial for sectors that heavily rely on metal components. These systems offer a proactive approach to assessing and managing corrosion, ultimately enhancing safety, reducing maintenance costs, and extending the life of assets.
In various industries, corrosion can lead to unexpected failures and financial losses. By leveraging corrosion monitoring, companies can make informed decisions based on accurate and real-time data. The technology not only identifies vulnerabilities but also helps in developing strategies for mitigation and repair. Let's delve deeper into specific sectors where these monitoring systems play a vital role.
Oil and Gas Industry
The oil and gas sector operates in some of the most demanding environments, where metal assets are susceptible to different types of corrosion. From pipelines to offshore platforms, the integrity of structures is pivotal for safety and operational efficiency.
- Real-time data: Corrosion monitoring systems provide real-time insights into the condition of assets, helping companies to address potential issues before they escalate into costly failures.
- Regulatory compliance: With stringent regulations around safety and environmental protection, effective corrosion management aids in compliance, avoiding hefty fines and legal troubles.
- Cost savings: Early detection of corrosion allows for targeted maintenance, which can be far less expensive than extensive overhauls or replacements.
In this sector, tools like electrochemical impedance spectroscopy and corrosion rate sensors have gained traction, facilitating continuous monitoring in challenging environments.
Marine Environments
Marine environments pose unique challenges for metals due to factors such as salinity, temperature variability, and biofouling. Ships, offshore platforms, and coastal structures often face rapid degradation from corrosion.
- Durability: Utilizing corrosion monitoring systems in these environments can significantly bolster the longevity of marine infrastructure. The systems can detect localized corrosion, allowing maintenance efforts to be precisely directed.
- Environmental conditions: Factors such as temperature and humidity can exacerbate corrosion processes. Integrated sensor systems can adapt to these changing conditions, offering an accurate picture of asset health over time.
- Performance optimization: By analyzing data collected through sensors, companies can optimize maintenance schedules, thus enhancing operational performance.
Marine applications often incorporate smart sensors that are specifically designed for harsh oceanic conditions, ensuring longevity and reliability in data collection.
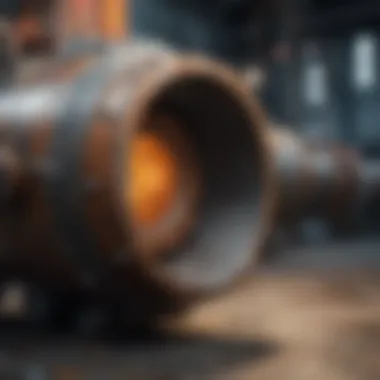
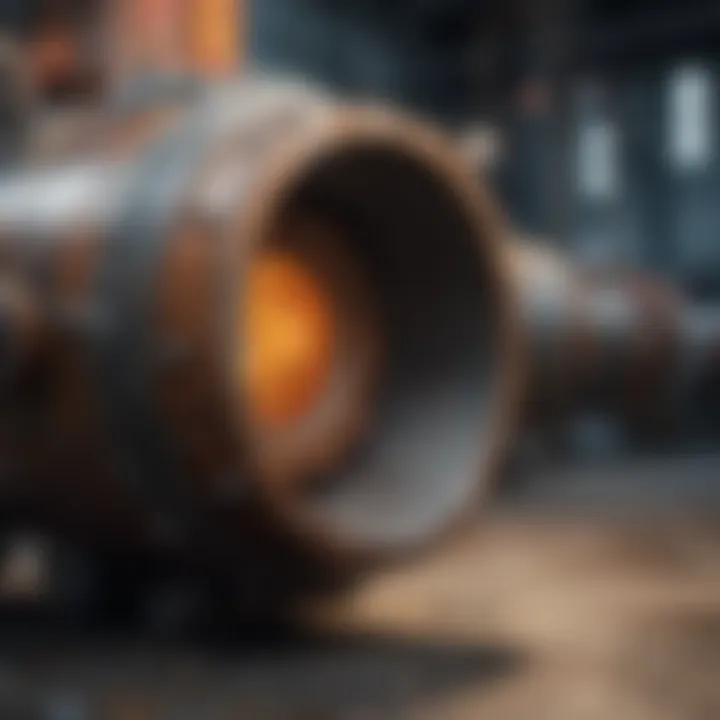
Infrastructure and Construction
In the construction sector, ensuring the durability of metal elements is fundamental to maintaining safety standards and longevity. Infrastructure such as bridges, buildings, and tunnels are paramount for public safety.
- Preventative measures: Implementing corrosion monitoring systems can preemptively highlight areas at risk, thus enabling repairs before they become serious. This proactive approach safeguards not only structural integrity but also human life.
- Resource allocation: Data collected can better inform maintenance budgets and strategies, emphasizing resource allocation where it's most needed. This results in a more efficient use of funds, which is critical in large-scale construction projects.
- Lifecycle management: By incorporating corrosion data into the broader management of a structure's lifecycle, stakeholders can more effectively evaluate refurbishment or replacement needs.
In this realm, nondestructive testing techniques and integrated sensor systems have become invaluable tools that contribute to safer and more sustainable construction practices.
Challenges in Corrosion Monitoring
Corrosion monitoring is no walk in the park. While the significance of keeping tabs on metal deterioration is clear, the challenges presented in this field can make it quite a conundrum. Factors influencing corrosion are many and varied, creating hurdles that professionals must navigate to ensure effective monitoring. This section aims to elucidate these challenges, discussing environmental factors, material limitations, and the complexities of integrating monitoring systems with existing infrastructure.
Environmental Factors
When it comes to corrosion monitoring, environmental factors play a huge role, like the weather on a picnic dayβeither it makes or breaks the event. High humidity, temperature fluctuations, and presence of corrosive elements in the air can all accelerate corrosion processes. For instance, industries located near oceans or in areas with high salt content in the air often find their metal structures at risk of rapid corrosion.
The impact of even minor changes in environmental conditions cannot be overstated. Factors such as:
- Chemical composition of the surrounding atmosphere
- Moisture levels
- Temperature variations
These elements can vary drastically and sometimes unpredictably, creating a need for monitoring systems that can adapt or respond accordingly. Professionals have to think on their feet, constantly adapting their strategies to match the whims of nature. This might involve investing in specialized sensors that can provide real-time data, ensuring that corrosive processes are identified before they lead to catastrophic failures.
Material Limitations
Material limitations are like the hidden rocks in a fishermanβs favorite spot; they can snag unwary anglers. Engineers and designers must contend with the fact that not all metals are created equal when it comes to corrosion resistance. Factors such as alloy type, coating, and even finishes can impact how quickly and effectively corrosion can be monitored.
For instance, while stainless steel offers better corrosion resistance than ordinary steel, it is not immune to localized corrosion such as pitting. Furthermore, coatings can deteriorate over time; therefore, the monitoring system must account for material degradation that can impact the reliability of measurements. Key considerations include:
- Selection of corrosion-resistant materials
- Regular assessment of coating integrity
- Understanding the corrosion behavior specific to each material
From this standpoint, monitoring systems must not only focus on tracking corrosion processes, but also on understanding how different materials behave under various conditions. Ensuring the integrity of the materials used in construction is essential to mitigate potential failures within structures that rely on metal integrity.
Integration with Existing Systems
Integrating corrosion monitoring systems with existing infrastructures can be as tricky as fitting a square peg into a round hole. Many facilities have legacy systems in place, which may not be compatible with newer monitoring technologies. This challenge poses several questions:
- How can new sensors coexist with older technology?
- What are the costs associated with retrofitting older equipment?
The goal here is to create a seamless flow of data without disrupting daily operations. Professionals may have to identify and deploy hybrid monitoring systems that capitalize on both old and new technology, thus preserving what works while upgrading to more advanced capabilities. This necessitates:
- Customizable solutions tailored to specific infrastructures
- Robust interfaces that can connect disparate systems
- Training programs for personnel to efficiently manage multiple systems
Future Directions in Corrosion Studies
Corrosion is an ever-present challenge across multiple fields, affecting everything from bridges to pipelines. Itβs crucial to keep an eye on emerging trends and technology that can revolutionize how we understand and manage corrosion. The future of corrosion studies not only aims to mitigate risks but also to optimize materials and methods to strengthen our infrastructure. As awareness grows, so does the importance of exploring advancements in technology that enhance corrosion monitoring systems. This section dives deep into specific technological developments, sustainability concerns, and cross-disciplinary approaches that hold promise for the future of this field.
Emerging Technologies
The landscape of corrosion monitoring is shifting with the introduction of several exciting emerging technologies. For instance, the application of machine learning in predicting corrosion patterns has taken off. By utilizing large datasets, these algorithms can identify trends and potentially foresee future corrosion incidents. This enables firms to act preemptively rather than simply reacting to damage once it occurs.
Additionally, advanced nanomaterials are paving the way for stronger and more corrosion-resistant structures. These materials, pushed by recent research, are being integrated into coatings that not only protect but actively heal. Some coatings can even respond to environmental changes, providing real-time feedback about the corrosion state.
"Emerging technologies are not just buzzwords; they represent a tangible shift in better understanding and managing corrosion."
Moreover, smart monitoring systems, which combine IoT devices with corrosion sensors, are becoming a norm. These systems facilitate continuous data collection that can be accessed remotely, combining convenience with advanced analytics. Construction teams can respond swiftly to potential issues, ultimately extending the lifespan of metal structures.
Sustainability Considerations
As environmental concerns escalate, the spotlight is on sustainability within the realm of corrosion management. Thereβs a noticeable shift towards recyclable materials and coatings that contain fewer harmful substances. The future will likely see a rise in bio-based inhibitors which help stave off corrosion with less environmental footprint.
Moreover, lifecycle assessments, which evaluate the environmental impacts of corrosion over time, are becoming integral to planning and developing metal structures. This evaluation leads to informed decision-making, ensuring that resources are used wisely while minimizing harm to the ecosystem.
Thoughtfully balancing economic and environmental factors can further enhance the resilience of structures. The focus on sustainability means that new standards and regulations might emerge, pushing industries to find innovative solutions that are both effective and eco-friendly.
Interdisciplinary Research Approaches
The convergence of various fields in research is proving to be an effective way to tackle corrosion issues. Interdisciplinary research approaches are gaining traction, breaking down traditional barriers. Collaboration among chemists, engineers, biologists, and data scientists can yield fascinating insights. Each discipline brings its unique solutions to the table, enriching the overall understanding and management of corrosion.
For example, integrating insights from materials science and environmental science can lead to innovative corrosion-resistant materials tailored for specific environments. Involvement of data scientists allows for the harnessing of big data, offering profound insights into corrosion behavior and helping in risk assessment.
Furthermore, universities and industries are joining forces to create programs focused on understanding corrosion in unique contexts. Such collaborative efforts will ensure that future corrosion studies remain relevant and impactful across multiple domains.
Finale
The examination of corrosion monitoring systems for metal samples has unveiled significant insights into how industries manage metal integrity. This final section underscores the importance of the key themes discussed throughout the article, as well as the urgent need for effective corrosion management strategies.
Summary of Key Points
Throughout the exploration of corrosion monitoring mechanisms, several core points have emerged:
- Diverse Techniques: From electrochemical methods to integrated sensor systems, the landscape of corrosion monitoring is broad and continues to evolve, presenting industries with numerous options tailored to specific needs.
- Data Analytics: The integration of data analytics into corrosion monitoring has revolutionized how information is processed and interpreted, enabling predictive maintenance and improved decision-making.
- Industry Applications: Sectors such as oil and gas, marine environments, and infrastructure rely heavily on corrosion monitoring to protect investments and ensure safety.
- Challenges and Innovations: Awareness of environmental and material limitations is critical, but ongoing technological advancements, like smart sensors and wireless systems, offer promising solutions to these challenges.
The Importance of Continued Research
As important as current strategies and technologies are, the pursuit of knowledge must continue unabated. The field of corrosion monitoring is ever-changing, and new challenges require fresh perspectives and innovative solutions.
- Emerging Technologies: Investing in research can lead to breakthroughs in nano-sensor technology and other advancements that may not yet be fully realized.
- Sustainability Considerations: With a world leaning towards greener practices, further studies into sustainable corrosion monitoring can bridge the gap between preservation and environmental stewardship.
- Interdisciplinary Approaches: Collaboration across disciplines can bring diverse insights, helping industries better adapt to evolving corrosion challenges.
"The only way to do great work is to love what you do." β Steve Jobs
For more insights, you can explore related articles on Britannica and stay connected through platforms like Reddit.