Ultrasonic Spray Coating: Principles and Applications
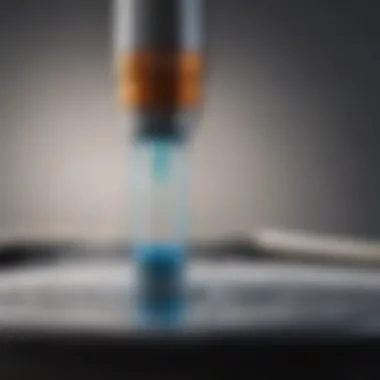
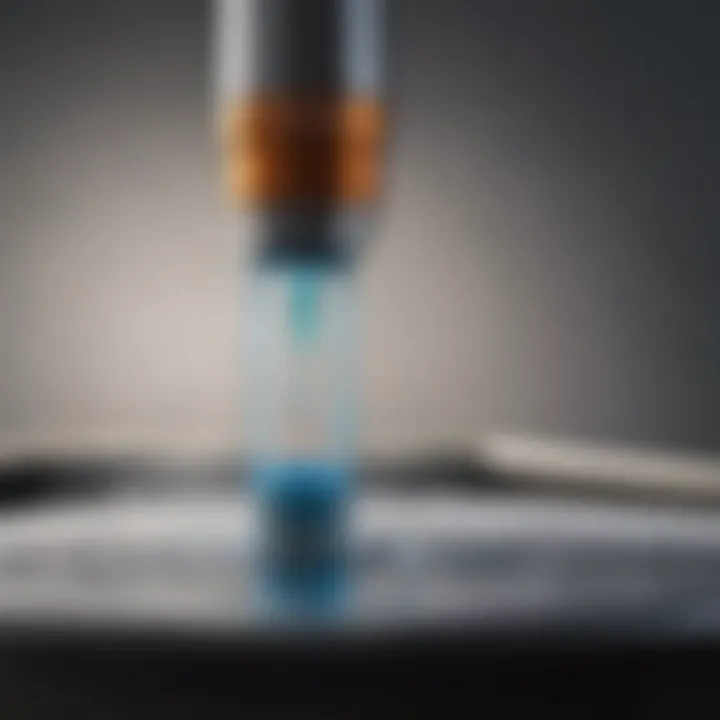
Intro
Ultrasonic spray coating is gaining attention in various industries due to its remarkable precision and efficiency in applying coatings. This innovative technique leverages ultrasonic energy to produce a fine mist of liquid, which offers several advantages over traditional spraying methods. Both academics and industry professionals recognize the growing significance of this technology in ensuring consistent and high-quality coatings. As we delve into the mechanics, applications, and future directions of ultrasonic spray coating, it becomes clear that understanding its principles is crucial for optimizing oneβs workflow and improving product performance.
Research Overview
Summary of Key Findings
Through comprehensive analysis, it has been observed that ultrasonic spray coating offers superior uniformity and thickness control in applied layers. This method reduces material waste significantly and allows for the effective coating of complex geometries that are otherwise challenging for conventional techniques. The process consumes less energy, highlighting its sustainability compared to traditional solvent-based spraying methods.
Key findings include:
- Enhanced precision in coating thickness and distribution
- Increased efficiency, leading to reduced operational costs
- Broad compatibility with various materials, including polymers, metals, and ceramics
- Potential for application in sectors like pharmaceuticals, electronics, and automotive industries
Research Objectives and Hypotheses
The main objective of this article is to elucidate the principles and functionality of ultrasonic spray coating. It aims to highlight not only the mechanics behind the process but also the practical applications across diverse industries. A hypothesized outcome of focusing on this technology is the recognition of its transformative potential, leading to wider adoption. Researchers and professionals involved in coating technologies will benefit from this in-depth exploration, seeking new methods to enhance their production processes.
Methodology
Study Design and Approach
This article employs a literature review approach, examining existing studies and industry reports on ultrasonic spray coating. By synthesizing the knowledge from various scholarly articles and technical papers, the article aims to provide a well-rounded overview of its principles and applications. The structure facilitates an understanding of the evolving landscape of this coating technology and its implications.
Data Collection Techniques
Data was collected using a variety of resources, including:
- Peer-reviewed journal articles
- Industry reports
- Technical specifications from manufacturers of ultrasonic spray equipment
- Online discussions and forums like those found on reddit.com, where industry practitioners share experiences
Understanding Ultrasonic Spray Coating
Ultrasonic spray coating is a method that has gained considerable attention across various industries due to its unique operational mechanisms and advantages. Understanding this technique is crucial for both academics and professionals who aim to apply it effectively in their fields. The process combines principles of ultrasonics and spray technology to create fine coatings on surfaces. This can lead to improved product performance and quality.
Definition and Overview
Ultrasonic spray coating refers to a liquid application process that uses ultrasonic waves to atomize a liquid into fine droplets. These droplets are then deposited onto a substrate, allowing for a uniform coating. The application combines both ultrasonic atomization and spray technology, providing significant benefits such as reduced overspray and better material utilization.
Key characteristics of ultrasonic spray coating include:
- Atomization: The ultrasonic waves create high-frequency vibrations that break the liquid into uniform droplets.
- Control: The process allows for the precise control of droplet size and distribution, leading to consistent coating thickness.
- Versatility: It can be used with various materials, including liquids and suspensions.
Historical Development
The concept of ultrasonic spray coating did not emerge overnight. It was the result of several advancements in spray technology and ultrasonics. Early experiments with ultrasonics date back to the early 20th century, primarily in the fields of sonar and medical imaging. In the latter half of the 20th century, researchers began to explore the potential of applying these principles to industrial processes.
The practical application of ultrasonic spray coating technology began gaining traction in the late 1980s and early 1990s. It was during this time that industries recognized the need for more efficient and precise coating techniques. Subsequently, various industries, including electronics and healthcare, started adopting ultrasonic spray coating for its significant advantages over traditional methods such as conventional spraying or dipping.
In recent years, advancements in ultrasonic technology have further enhanced its applicability, contributing to its growing popularity in the coating sector. As a result, ultrasonic spray coating continues to evolve, driving innovations in materials and application processes, and shaping the future of manufacturing.
Operating Principles of Ultrasonic Spray Coating
Understanding the operating principles of ultrasonic spray coating is crucial for those involved in its application and research. This section delves into how ultrasonic spray coating functions on a fundamental level, the technologies employed, and their implications in enhancing efficiency and precision in various applications.
Ultrasonic Atomization
Ultrasonic atomization is a key component in the ultrasonic spray coating process. It involves the conversion of liquid materials into fine droplets through ultrasonic vibrations. When a liquid is subjected to ultrasonic waves, it experiences rapid changes in pressure, leading to the formation of tiny droplets. This method is highly efficient and enables a uniform distribution of coating material on various substrates.
The size of the droplets is critical in determining the quality of the coating. Smaller droplets provide better surface coverage and adherence. Ultrasonic atomizers can achieve droplets as tiny as a few micrometers, which is significantly smaller than conventional spray methods. As a result, the coatings produced are often more uniform and of higher quality compared to those achieved by other spraying techniques.
Droplet Formation Mechanism
The droplet formation mechanism is intricately tied to the principles of ultrasonic spray coating. The process begins when the ultrasonic transducer generates high-frequency sound waves, which travel through the liquid. This causes rapid oscillations that lead to cavitation bubbles forming within the liquid.
When these cavitation bubbles collapse, they create mini shock waves that exert pressure on the surrounding liquid. This pressure causes the liquid to break apart into droplets. The size and distribution of these droplets are influenced by several factors, including the viscosity of the liquid, frequency of the ultrasonic waves, and the amplitude of oscillations. Understanding these variables is essential for optimizing the coating application, especially in specialized fields like biomedical or electronics industries.
Effects of Frequency and Amplitude
The frequency and amplitude of the ultrasonic waves play significant roles in the performance of ultrasonic spray coating. The frequency typically refers to the number of vibrations per second and can range from tens of kilohertz to several megahertz. Higher frequencies generally produce smaller droplets. However, they require more power and may not be suitable for all materials.
Amplitude, on the other hand, indicates the intensity of the ultrasonic vibrations. A higher amplitude correlates with a greater energy transfer to the liquid, resulting in more aggressive atomization and potentially larger droplets. Therefore, striking the right balance between frequency and amplitude is essential. Adjustment of these parameters can lead to significant differences in coating quality and application effectiveness.
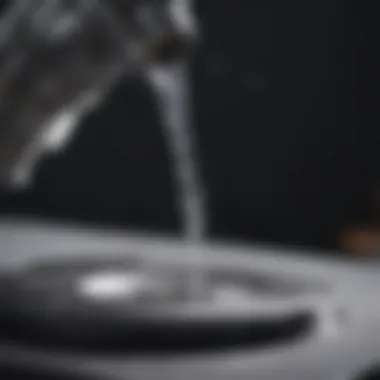
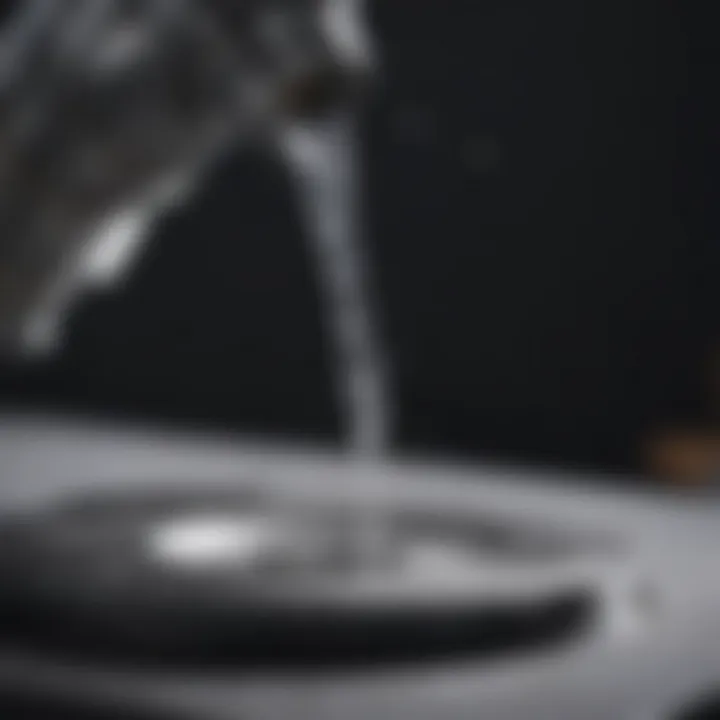
In summary, the operational principles behind ultrasonic spray coating are complex yet fascinating. By comprehending ultrasonic atomization, droplet formation, and the effects of frequency and amplitude, one can better appreciate the advantages of this technology and its relevance across various industries.
"Understanding the mechanics of ultrasonic spray coating can unlock new possibilities in material applications, leading to improved performance and efficiency."
This knowledge not only enhances the understanding of existing processes but also opens avenues for future innovations.
Materials Used in Ultrasonic Spray Coating
The choice of materials in ultrasonic spray coating is crucial for achieving the desired coating properties and performance. It encompasses both the liquid materials used for atomization and the solid powders or suspensions that might be incorporated into the process. This section discusses the different types of materials employed in ultrasonic spray coating, their significance, and the implications of their use in varying applications.
Liquid Materials
Liquid materials form the foundation of the ultrasonic spray coating process. They serve as the primary substances that are atomized and applied to surfaces. These can include solutions, suspensions, and emulsions formulated from various polymers, solvents, and additives. Each of these properties influences the behavior of the droplets as they are sprayed.
- Polymers: Common liquid materials consist of thermoplastics and thermosetting polymers. Choices here can enhance adhesion, flexibility, and tensile strength of the coatings.
- Solvents: Solvent selection is essential, as it affects the viscosity and volatility of the liquid. A well-chosen solvent facilitates the atomization process and ensures proper drying time.
- Additives: Additives can modify properties such as flow, adhesion, and surface tension. Incorporating these ensures the coating meets specific performance criteria.
In essence, the right combination of liquid materials leads to improved efficiency in the coating process, enabling uniform application and optimized performance of the coated surface.
Solid Powders and Suspensions
Solid powders and suspensions can also play a key role in ultrasonic spray coating. Their incorporation into liquid materials leads to unique properties and enhances the functionality of the coatings. These solid additives can be metals, ceramics, or specialized composite materials.
- Metals: The use of metal powders in coatings can enhance electrical conductivity and create functional surfaces. Applications might be found in electronics or automotive industries.
- Ceramics: Ceramic powders are employed when high resistance to wear and corrosion is necessary. For example, they are extensively used in aerospace and biomedical applications.
- Composites: Adding composite materials can provide a balance of properties, combining the strengths of various materials to fulfill specific task criteria.
Such inclusions can improve performance but also require precise control during the coating process to ensure the right distribution of the solid components.
Material Compatibility
Material compatibility is important when discussing ultrasonic spray coatings. It examines how different materials interact with one another during the coating process. Poor compatibility can lead to various issues like delamination, ineffective adhesion, or inconsistent coating quality.
- Chemistry: Understanding the chemical properties of each material is fundamental. Interaction between the liquid and solid materials must be optimized to ensure desired performance outcomes.
- Temperature Stability: Some materials may have limits to the temperatures they can endure. If the coating process exceeds these limits, it can result in degradation or changes in properties.
- Application Method: Compatibility also concerns the method of application. Certain materials may require precise nozzle configurations or specific ultrasonic frequencies to function effectively.
Successful ultrasonic spray coating is dependent on an intricate understanding of how these various materials will interact both during and after the application. By considering these elements, manufacturers can achieve advanced functional coatings suitable for a wide array of applications.
Equipment and Setup for Ultrasonic Spray Coating
The efficiency and effectiveness of ultrasonic spray coating heavily rely on the equipment and setup utilized in the process. Precise configuration and integration of various components are crucial for achieving the desired outcomes in coating applications. Each part of the setup must work together seamlessly to ensure optimal performance, consistency, and repeatability in coating applications.
Spray Nozzle Configuration
Spray nozzles are essential components of ultrasonic spray coating systems. They play a critical role in the atomization process. The nozzle configuration determines how the coating material is delivered to the substrate surface.
Different types of nozzles can affect the droplet size and spray pattern, which directly influences the coating uniformity. Options include direct and indirect spray nozzles, which provide varying levels of control over spray characteristics. For instance, a dual-fan nozzle might facilitate a broader spray, allowing for the coating of larger areas with minimal overlapping, leading to efficiency in material usage.
It is also important to consider factors like nozzle diameter, length, and positioning to optimize the atomization energy and ensure proper interaction with the ultrasonic waves. Keep these configuration aspects in mind when designing your ultrasonic spray application.
Fluid Delivery System
The fluid delivery system is another crucial element in the setup for ultrasonic spray coating. This system must accurately transport liquid materials from a reservoir to the spray nozzle without introducing air bubbles or contaminants.
Typically, these systems employ peristaltic pumps or syringe pumps to maintain a consistent flow rate and pressure. Proper fluid delivery ensures that the right amount of material reaches the nozzle at the correct viscosity, helping optimize the spray's performance. Viscosity plays a significant role in droplet formation and spray consistency; thus, the delivery system must accommodate variations in fluid properties.
Additionally, consideration should be given to the materials used in the delivery system to avoid chemical reactions with the coating materials. Compatibility between the fluid delivery components and the materials being sprayed must be ensured to prevent clogs and other flow disruptions.
Control and Monitoring Systems
Control and monitoring systems are the backbone of effective ultrasonic spray coating operations. These systems enable real-time adjustments and ensure process parameters remain within the desired ranges.
Advanced ultrasonic spray coating setups often use computer-aided control systems that allow for precise modulation of parameters such as spray timing, amplitude, and frequency. By monitoring variables continuously, these systems help maintain optimal processing conditions and enable prompt corrective action should deviations occur.
Key features to look for in control systems include:
- Visual display for evaluating various parameters.
- Data logging functions for analyzing performance over time.
- Remote operability to facilitate adjustments without interrupting the coating process.
Process Optimization in Ultrasonic Spray Coating
Process optimization is crucial in ultrasonic spray coating to maximize efficiency, quality, and cost-effectiveness. This section investigates various strategies and techniques to enhance the ultrasonic spray coating process. By optimizing the parameters involved, it is possible to achieve superior results that benefit manufacturers across different sectors. The effectiveness of spraying operations hinges on consistently achieving the right coating, ensuring reliability in performance.
Parameter Adjustment Techniques
To reach optimal performance in ultrasonic spray coating, precise parameter adjustment techniques are essential. Key parameters include ultrasonic frequency, fluid viscosity, and feed rate, among others.
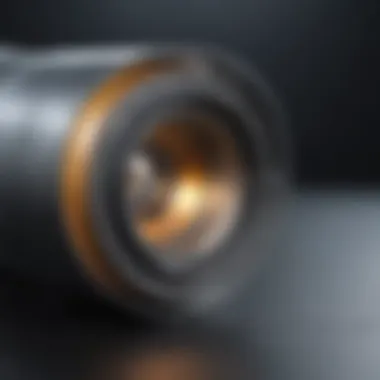
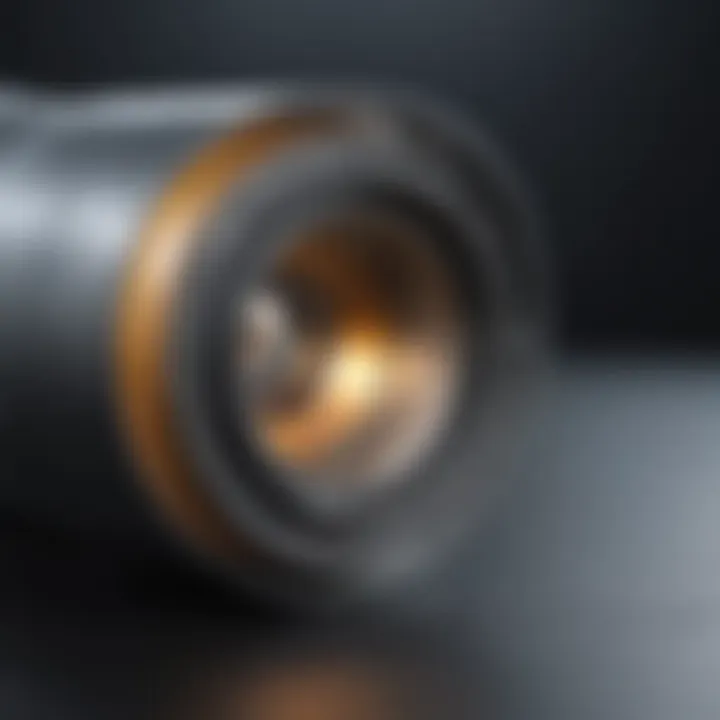
- Ultrasonic Frequency: Adjusting the frequency can influence the droplet size and distribution. A higher frequency often leads to smaller, more uniform droplets, which can enhance the quality of the coating.
- Fluid Viscosity: The viscosity of the liquid material being sprayed needs careful consideration. Higher viscosity fluids may require increased energy or temperature to achieve proper atomization.
- Feed Rate: Managing the feed rate is vital for achieving a consistent coating thickness. A steady feed rate minimizes fluctuation in coating consistency.
Properly calibrated parameters allow for tailored coatings specific to the application, balancing performance with the operational limits of the equipment used.
Quality Control Measures
Maintaining high standards in quality control is indispensable in the ultrasonic spray coating process. Regular monitoring and adjustments are needed to ensure that the coatings meet intended specifications. This can include:
- Visual Inspection: Conducting visual checks ensures that there are no defects or inconsistencies in the coating layer. This is often the first line of defense.
- Thickness Measurement: Utilizing tools such as ultrasonic thickness gauges can help assess whether the coating meets the required specifications.
- Durability Testing: Coatings should be subjected to stress tests to confirm their durability under operating conditions.
Implementing these quality control measures not only enhances the final product but also minimizes waste and rework, ultimately preserving resource allocation.
Statistical Process Control
Statistical Process Control (SPC) is a method that applies statistical techniques to monitor and control the spray coating process. SPC can identify variances in production, track trends, and ensure consistent output. Key components of SPC include:
- Control Charts: These charts help visualize data over time, making it easier to detect deviations from the process mean.
- Process Capability Analysis: This analysis evaluates how well a process can produce output within specified limits, identifying areas needing improvement.
- Data Collection: Gathering data from the process is vital for analysis, allowing operators to make informed decisions based on empirical evidence.
By integrating SPC into the ultrasonic spray coating process, organizations can achieve higher levels of precision and predictability. This leads to improved output quality and fosters a data-driven approach to optimization.
Proper optimization not only leads to smoother operations but also enhances the overall longevity and performance of the coatings applied.
Applications of Ultrasonic Spray Coating
The applications of ultrasonic spray coating play a crucial role in various industries by offering innovative solutions to complex problems. This section delves into the specific domains where ultrasonic spray coating is applied, highlighting its capabilities and advantages. From enhancing product functionality to improving manufacturing processes, understanding these applications helps in recognizing the relevance of this technology. Below are the primary fields where ultrasonic spray coating shows significant impact.
Biomedical Applications
In the biomedical field, ultrasonic spray coating has emerged as a revolutionary technique. It is used in creating thin films for drug delivery systems, enabling uniform coating of pharmaceutical compounds. By employing this method, a precise dosage can be achieved on medical devices, such as stents and implants. The ability to control droplet size enhances drug absorption and biocompatibility, making treatments more effective. Additionally, coatings applied via ultrasonic spraying can prevent biofilm formation on surfaces, significantly improving device longevity and performance.
The advantages of using ultrasonic spray coating in biomedical applications include:
- Uniformity: Ensures consistent thickness across surfaces.
- Versatility: Compatible with a range of materials and drug compounds.
- Efficiency: Reduces waste and optimizes production time.
Overall, this technology holds promise for advancing biomedical engineering and enhancing patient outcomes.
Electronics and Semiconductor Industries
In the electronics sector, ultrasonic spray coating is vital for manufacturing high-performance components. Its precision in applying coating materials makes it suitable for creating conformal coatings on printed circuit boards and semiconductor devices. These coatings provide protection from moisture, corrosion, and other environmental factors, ensuring reliability and duration of electronic products.
Furthermore, ultrasonic spraying allows for the integration of functional materials, such as conductive inks and dielectric layers. The ability to customize thickness and material properties enables advancements in the miniaturization and efficiency of electronic components. The significant benefits include:
- Enhanced Protection: Shields sensitive components from external threats.
- Cost-Effectiveness: Minimizes material waste while maximizing coverage.
- Improved Performance: Facilitates the production of high-quality electronic devices.
Thus, ultrasonic spray coating transforms how electronic products are developed and manufactured, driving innovation in the industry.
Automotive and Aerospace Applications
The automotive and aerospace industries also significantly benefit from ultrasonic spray coating. In automotive manufacturing, this technique is employed for applying protective coatings on parts such as engines, undercarriages, and body panels. The even application of coatings helps in preventing rust and corrosion, improving vehicle durability and aesthetics.
In aerospace, weight reduction is crucial, and ultrasonic spray coating contributes by allowing the use of lightweight materials without compromising protection. It is used for applying thermal barrier coatings on engine components and for surface modifications that enhance aerodynamic performance.
Key points regarding these applications include:
- Durability: Coatings enhance lifespan and performance of vehicle components.
- Weight Efficiency: Ensures that lightweight materials can be employed effectively.
- Precision: Tailored applications based on performance requirements and specifications.
Overall, ultrasonic spray coating stands out as a solution capable of meeting the demanding requirements of both automotive and aerospace manufacturing, leading to safer and more efficient vehicles and aircraft.
Advantages of Ultrasonic Spray Coating
The utilization of ultrasonic spray coating presents distinct advantages that significantly impact various industries. Understanding these benefits is crucial for leveraging this technology effectively. The main advantages include efficiency and precision, reduction of material waste, and enhanced coating uniformity. Each of these elements plays a vital role in motivating enterprises to adopt ultrasonic spray coating methods over traditional techniques.
Efficiency and Precision
Ultrasonic spray coating is known for its high efficiency and precision. The ultrasonic atomization process allows for finer droplet sizes, which ensures better coverage of the target surface. This technology enables coatings to be applied uniformly, reducing the likelihood of imperfections. Additionally, the precision of the spray patterns can be adjusted, which means specific areas can be treated without unnecessary over-spray.
This level of control is particularly valuable in industries such as electronics and biotechnology, where coating accuracy is paramount. In these scenarios, even slight variances in coverage can result in significant performance differences.
Reduction of Material Waste
One of the most significant advantages of ultrasonic spray coating is the reduction of material waste. In traditional spraying methods, a considerable amount of material is lost to over-spray or poorly directed sprays. However, with ultrasonic technologies, the efficiency of material usage is improved dramatically. Because the droplet formation is finely tuned, less material is needed for the same amount of coverage.
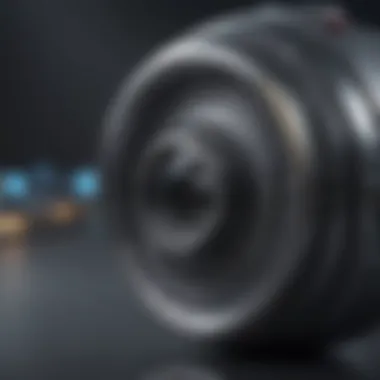
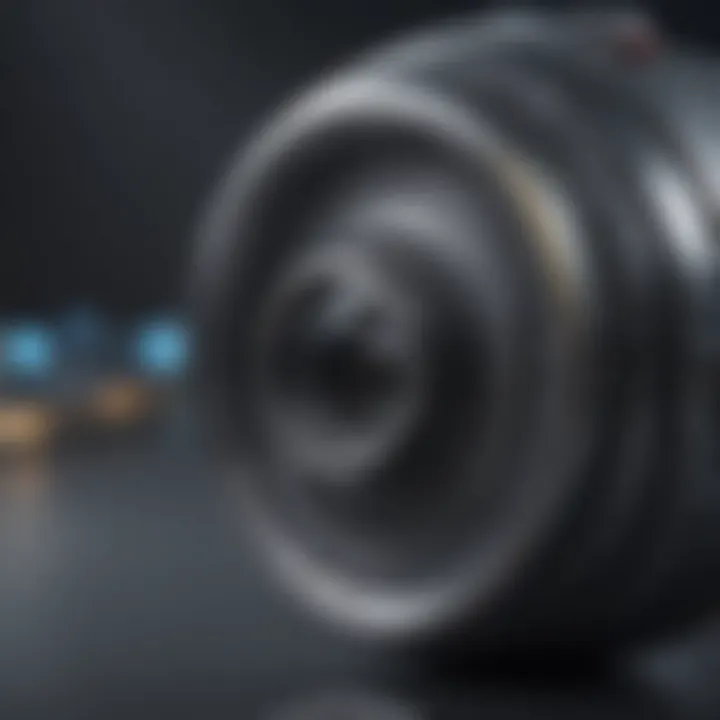
Moreover, processes that are less wasteful not only reduce costs but also have a positive environmental impact. Fewer resources lead to reduced waste output, contributing to more sustainable manufacturing practices.
Enhanced Coating Uniformity
Coating uniformity is another critical advantage of ultrasonic spray coating. The method produces consistent droplet sizes and uniform coverage, which is essential for the integrity of the coating. Variations in thickness can lead to problems such as uneven wear or performance inconsistencies, particularly in technical applications.
By ensuring a uniform coating, potential defects are minimized. This improves the longevity and performance of the coated products. Enhanced uniformity also allows for better adhesion and finish quality, which is highly valued in applications ranging from automotive parts to medical devices.
"Ultrasonic spray coating significantly enhances production efficiency while maintaining quality standards across the board."
In closing, the advantages of ultrasonic spray coating cannot be understated. The blend of efficiency, material conservation, and uniformity present compelling reasons for industries to adopt this technology. These factors solidify ultrasonic spray coating as a viable option for businesses aiming for innovation and sustainability in their production methods.
Challenges and Limitations
In the exploration of ultrasonic spray coating, understanding the challenges and limitations is crucial. While this technology offers significant benefits, it is not without its hurdles. Each challenge presents a unique consideration that industries must navigate to fully leverage the advantages of ultrasonic spray coating. Addressing these challenges ensures optimal performance and maximizes the technology's potential impact.
Equipment Costs and Maintenance
Ultrasonic spray coating requires specialized equipment, which often entails a high initial investment. The cost of ultrasonic spray systems can be considerable compared to traditional coating methods. Besides the purchase price, maintenance of these systems can also incur ongoing expenses. Maintaining equipment is necessary to achieve consistent coating results. Regular checks and services are crucial to ensure that ultrasonic nozzles and fluid delivery systems operate effectively. Failure to properly maintain these systems might lead to decreased performance or even total breakdown. These factors make cost considerations a significant part of implementing ultrasonic spray coating.
Operator Training Requirements
Another challenge involves the operator training requirements. Ultrasonic spray coating systems necessitate skilled operators who understand the nuances of the technology. Training sessions must cover the equipment's operation, the science behind atomization, and the adjustment of parameters for optimal performance. Without a knowledgeable operator, the risk of improper application increases, resulting in inconsistent coating quality and potential material waste. This creates an added layer of complexity for organizations looking to adopt this technology, as they must invest in personnel training alongside equipment costs.
Material Limitations
Lastly, one must consider the material limitations associated with ultrasonic spray coating. While this method is versatile, it is not suitable for every type of material. Certain materials may not atomize effectively or may require specific conditions to maintain proper consistency during spray application. Some fluids may also exhibit behaviors that challenge proper droplet formation, leading to uneven coating. Therefore, industry professionals must carefully assess the compatibility of materials with ultrasonic spray technology to avoid suboptimal results.
Understanding these challenges is critical for successful implementation in various industries.
Future Directions in Ultrasonic Spray Coating Research
Research in ultrasonic spray coating is continuously evolving. Understanding its future directions is important. The advancements in this technology can significantly affect various industries. The focus on emerging technologies, potential developments in materials, and innovative applications will shape the landscape.
Emerging Technologies
Emerging technologies play a pivotal role in the growth of ultrasonic spray coating. One such technology is the integration of artificial intelligence into the control systems. AI can enhance spray pattern analysis and real-time feedback mechanisms, leading to improved coating quality and efficiency.
Another key area is the development of advanced ultrasonic transducers. Innovations here can increase the effectiveness of atomization. With better transducer designs, the process can be optimized for different materials, including tricky viscous liquids. This can broaden the application range of ultrasonic spray coating, making it suitable for more complex scenarios.
Potential Developments in Materials
Materials development is equally crucial for the future of ultrasonic spray coating. The creation of new coating materials that exhibit superior performance can drive this technology forward. For instance, bio-based materials are gaining interest. They could open new pathways in industries such as biomedical fields, where sustainability is becoming a priority.
Furthermore, tailoring the properties of current materials can lead to significant improvements. This includes modifying viscosity and surface tension characteristics. By focusing on material compatibility with the process, manufacturers can achieve finer control over the end results. Thus, research on material innovations must continue vigorously.
Innovative Applications on the Horizon
The potential for innovative applications of ultrasonic spray coating is vast. One notable area is in the electronics industry, particularly with the rise of flexible and wearable technology. Ultrasonic spray coating can provide effective and uniform coatings on thin substrates, which is essential for these applications.
In addition, there is promise in protective coatings for automotive and aerospace sectors. Delivering coatings that are lighter yet still protective and durable is an ongoing challenge. Ultrasonic spray coating might offer solutions here, allowing for the precise application of these desirable materials.
"The future of ultrasonic spray coating holds immense promise, as innovative technologies and materials drive new applications across industries."
These future directions in ultrasonic spray coating need focused research efforts. As awareness and understanding grow, industries stand to benefit substantially from developments in this technology.
Ending
The conclusion of this article serves as a pivotal moment to synthesize the various aspects discussed regarding ultrasonic spray coating. This method stands at the intersection of technology and efficiency. It offers significant advantages in precision application across diverse industries. In the realms of biomedical applications, electronics, and automotive sectors, its ability to reduce material waste while enhancing coating uniformity is particularly noteworthy.
Summary of Key Points
The journey through ultrasonic spray coating reveals several key points:
- Operational Mechanisms: Understanding how ultrasonic atomization works is fundamental. The frequency and amplitude play crucial roles in droplet formation, determining the effectiveness of the spray.
- Material Compatibility: A diverse range of materials can be used, but compatibility must be considered. Knowing which liquids and powders suit this method is essential for successful application.
- Applications Across Industries: Biomedical, electronics, and automotive applications demonstrate the versatility of ultrasonic spray coating. Each sector benefits uniquely from this technology.
- Efficiency and Waste Reduction: The precision of this coating method minimizes waste, which is increasingly important in todayβs environmentally conscious landscape.
- Future Directions: The article outlines emerging technologies and potential material developments, showing that research in this area is far from stagnant.
The Importance of Further Research
Further research in ultrasonic spray coating is vital for several reasons. First, advancing the existing technology can lead to improved processes that optimize performance. As more findings emerge, industries can adapt to incorporate enhanced methods into their production lines. Second, exploring potential materials can open new avenues for applications previously deemed incompatible or unviable. Keeping abreast of these developments ensures that professionals remain ahead in a rapidly evolving field. Lastly, the interdisciplinary nature of ultrasonic spray coating calls for collaboration across engineering, materials science, and other fields. This rich interplay can drive innovation, ensuring that ultrasonic spray coating gains broader acceptance and integration in new and established industries.
Continued exploration in this domain not only sharpens competitive edges for businesses but also fosters sustainable practices by reducing waste and improving efficiency.
Key Texts and Studies
Several key texts stand out in the field of ultrasonic spray coating. For instance, technical papers published in journals like the Journal of Coatings Technology and Research or Surface and Coatings Technology provide in-depth methodologies and experimental findings. These sources often introduce foundational concepts that inform current practices and advancements in the field, allowing researchers to build on established knowledge. Other notable studies include:
- Ultrasonic Spray Coating Techniques: A comprehensive analysis that discusses various techniques applied in ultrasonic spray technologies.
- Material Performance in Ultrasonic Coatings: This text explores how different materials behave under ultrasonic spray conditions, offering insights on optimizing performance.
- Efficiency Metrics in Industrial Applications: This book chapters illuminate efficiency improvements introduced by ultrasonic spray coating in diverse industries like automotive and electronics.
By understanding these texts, professionals and researchers can enhance their comprehension of the mechanisms at play and the latest innovations.