Innovative Flexible Heat Pipes: Engineering & Uses
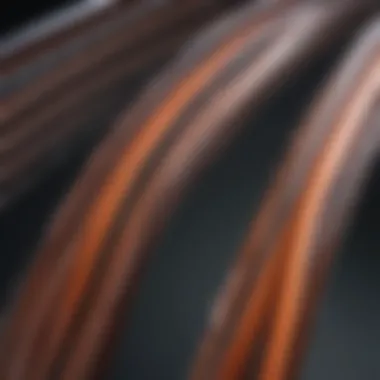
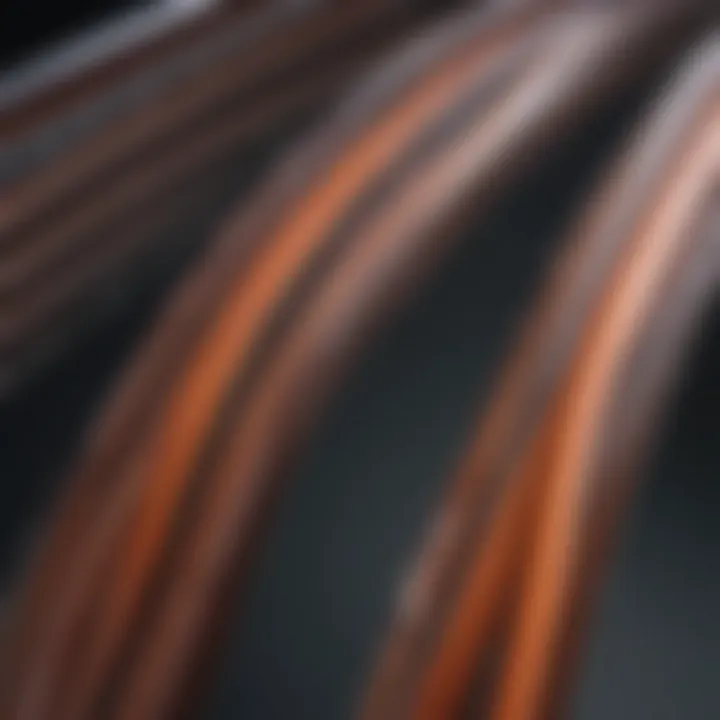
Intro
Flexible heat pipes represent a significant innovation in thermal management technology. Unlike traditional rigid heat pipes, their adaptable nature allows for innovative designs and applications. This technology has implications across various industries, including electronics, aerospace, and renewable energy. Understanding how these systems work and the materials behind them is crucial for advancing practical uses.
The engineering principles are foundational to grasping the capabilities of flexible heat pipes. These principles are based on thermodynamics and fluid mechanics, establishing how heat transfer occurs efficiently. Material composition also plays an essential role. Manufacturers leverage materials such as copper, aluminum, and advanced composites to enhance performance. The process of making flexible heat pipes involves precision engineering, ensuring that they can bend and flex while maintaining functionality.
This article will explore the advancements made in the field of heat pipes, focusing on their versatile applications, advantages, and potential limitations. By delving into current research trends and future directions, readers can gain a comprehensive view of how flexible heat pipes can shape the landscape of thermal management solutions.
Preamble to Heat Pipes
Heat pipes are specialized thermal devices designed for efficient heat transfer. Their significance lies in their ability to move heat from one location to another with minimal thermal resistance. In this article, we explore the fundamental aspects of heat pipes, emphasizing how this technology drives advancements in thermal management solutions.
Definition and Functionality
A heat pipe can be defined as a sealed container that facilitates heat transfer through the phase change of a working fluid. The functionality of a heat pipe revolves around its core design, which involves an evaporator section, a condenser section, and a working fluid that circulates between these sections. The liquid in the evaporator absorbs heat and transforms into vapor. This vapor then travels to the condenser, where it releases heat and returns to the liquid state. The cycle continues, allowing for continuous heat transfer. The efficiency of heat pipes is a great advantage, as they can conduct more heat than solid thermal conductors like copper or aluminum, making them invaluable in applications where space and efficiency are crucial.
Historical Development
The concept of heat pipes is not recent; it dates back to the 1960s. Originally, they were developed for use in aerospace applications due to their excellent thermal management capabilities. NASA employed heat pipes in spacecraft to control temperatures in external equipment, demonstrating the technology's effectiveness. Over the decades, the design and materials have evolved. Today, heat pipes are ubiquitous across various industries including electronics cooling and renewable energy systems, reflecting their adaptability and reliability over time.
Fundamental Operating Principles
The operational principles of heat pipes are rooted in thermodynamics. The heat transfer process involves two main phases: the vaporization of the working fluid and its subsequent condensation. This phase change is integral, as it allows for effective thermal energy transfer. The wick structure within a heat pipe plays a crucial role by facilitating the return flow of the condensed liquid back to the evaporator. Different wick designs, including porous materials and grooves, can significantly influence the heat pipeβs efficiency. Factors like temperature gradient, working fluid choice, and the geometry of the pipe also contribute to the overall performance.
"Heat pipes represent one of the most efficient methods for thermal management, significantly impacting the design of thermal systems in modern technology."
A thorough understanding of these principles is essential for engineering applications, whether in space vehicles or electronic devices. The specialization and versatility of heat pipes illustrate their importance in the broader context of thermal management. As we move forward, exploring flexible heat pipes will reveal even more exciting advancements disrupting traditional thermal management processes.
Flexible Heat Pipe Design
The design of flexible heat pipes is crucial in maximizing their performance in various applications. This section will examine the multiple aspects of flexible heat pipe design, detailing their importance, benefits, and the design considerations that engineers must keep in mind. With the growing demand for efficient thermal management solutions, understanding the intricacies of flexible heat pipes can lead to innovations across industries.
Overview of Flexibility in Heat Pipes
Flexibility in heat pipes allows for greater adaptability in thermal management systems. Traditional rigid heat pipes are limited in terms of installation and application. In contrast, flexible heat pipes can conform to complex geometries. This is particularly useful in aerospace and electronics, where space constraints are common. The ability to bend and twist without compromising thermal performance enhances their usability in constrained environments.
The flexibility of heat pipes is achieved through specific design techniques. Thin-walled structures and advanced manufacturing methods enable the creation of flexible segments. Engineers must ensure that these designs do not adversely affect the heat transfer efficiency.
Key Design Parameters
Several key design parameters influence the performance of flexible heat pipes. These include:
- Bend Radius: A smaller bend radius can provide greater flexibility but may impact thermal performance adversely. Designers must balance flexibility and thermal conductivity.
- Material Selection: The choice of materials affects both the structural integrity and the thermal conductivity of heat pipes. Advanced materials can enhance the performance while maintaining flexibility.
- Internal Structure: The internal wick structure plays a significant role in the capillary action that is essential for heat transfer. The design must accommodate flexibility while ensuring effective fluid movement.
- Operating Temperature: The thermal properties of materials must suit the application's operating temperature range. Flexible heat pipes must maintain performance under varying conditions.
These parameters are not independent; each design decision interacts with others to influence the overall efficiency and reliability of the heat pipe system.
Finite Element Modeling Techniques
Finite element modeling (FEM) is an essential technique in the design of flexible heat pipes. It allows engineers to simulate and analyze how a heat pipe will behave under various conditions. This includes thermal loads, mechanical stresses, and dynamic responses associated with flexibility.
By using FEM, designers can predict potential failure points within the flexible heat pipe. This predictive capability is essential in optimizing designs before physical prototypes are made. Engineers can adjust design elements based on simulations to enhance performance and reliability.
Moreover, FEM can identify the interaction between different materials in composite flexible heat pipes. Understanding how different materials behave in combination is critical for maximizing efficiency.
βFinite element modeling is not just a design tool; it's a strategic advantage in the development of flexible heat pipes.β
Materials Used in Flexible Heat Pipes
The choice of materials used in flexible heat pipes is critical. This aspect not only affects the performance but also the overall efficiency and longevity of the system. Flexible heat pipes rely heavily on their material properties to ensure effective heat transfer. The right materials can help manage thermal challenges, provide durability, and accommodate any design limitations encountered in various applications.
Materials influence the thermal conductivity, flexibility, and operational limits of heat pipes. The flexibility of the pipe allows it to adapt to tight spaces in devices. Thus, the materials used must maintain their performance under different physical conditions while being lightweight and easy to manufacture.
Selection Criteria for Materials
When considering materials for flexible heat pipes, several criteria must be examined. Here are key factors to focus on:
- Thermal Conductivity: This is crucial for efficient heat transfer. Materials with higher thermal conductivity are preferred as they allow for better performance.
- Mechanical Strength: The ability of a material to withstand various physical stresses is vital. This ensures that the heat pipe maintains integrity during use.
- Corrosion Resistance: In many applications, the heat pipe may encounter harsh environments. Corrosion-resistant materials help to extend the life of the system.
- Weight: Lightweight materials contribute to the overall portability of devices, making them suitable for aerospace and electronic uses.
- Flexibility: The capability of a material to bend without breaking is fundamental. Flexible materials enable adaptation to mobile and varied installations.
Commonly Used Materials
Several materials are frequently employed in the production of flexible heat pipes. Understanding their properties can help in selecting the right one for a given application:
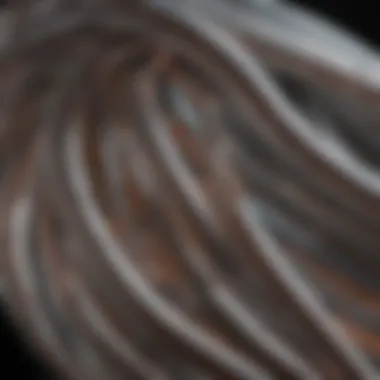
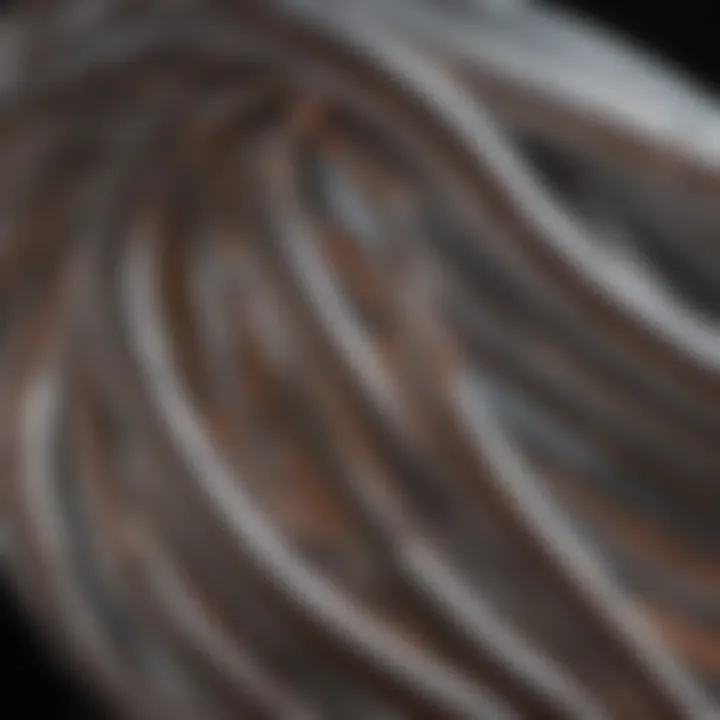
- Copper: Known for its high thermal conductivity, copper is often a preferred choice. Its malleability allows for effective bending and shaping.
- Aluminum: This material is lightweight and also exhibits good thermal conductivity. It is often used in the aerospace sector due to its strength-to-weight ratio.
- Stainless Steel: This material provides excellent durability and corrosion resistance. It is commonly used in environments that demand high reliability.
- Graphite: With excellent thermal dissipation properties, graphite is being explored for innovative designs in heat pipes. It offers good weight reduction compared to metals.
- Polymer Composites: Emerging in recent years, these materials offer lightweight options with adequate thermal performance for specific applications.
Emerging Material Technologies
Research into innovative materials is continuously evolving. New technologies provide opportunities for better performance and additional applications in flexible heat pipes. Some noteworthy advancements include:
- Carbon Nanotubes: These materials have exceptional thermal conductivity and are being examined for their performance in compact heat pipes.
- Phase-Change Materials (PCMs): Integration of PCMs can enhance heat storage capabilities, allowing for better thermal management in time-varying conditions.
- Advanced Metal-Matrix Composites: These materials promise improved strength and lightweight properties, providing enhanced thermal transfer efficiency.
- Graphene: Influential research focuses on graphene application in heat pipes. Its high thermal conductivity can significantly improve performance metrics.
Innovations are crucial for meeting future thermal management demands. These technologies pave the way for broader uses in several sectors, from aerospace to consumer electronics.
"The advancement in materials science will define the next generation of flexible heat pipes, optimizing performance and expanding applications across industries."
Flexibility in heat pipe design is not just about structural properties; itβs about enhancing thermal performance through intelligent material choices.
Manufacturing Processes for Flexible Heat Pipes
The manufacturing processes for flexible heat pipes are crucial in defining their performance and reliability. These processes not only determine the physical integrity of the heat pipe but also influence its thermal efficiency. Understanding the nuances of these methods is essential for engineers and manufacturers who aim to optimize flexible heat pipes for varied applications. By examining these processes, we can appreciate how design choices impact functionality and marketability.
Fabrication Techniques
Fabrication techniques for flexible heat pipes have evolved significantly due to advancements in technology and material science. Traditional methods, such as welding and brazing, have been refined to accommodate the complexities presented by flexibility requirements.
Common techniques include:
- Laser Welding: This offers precision and control, reducing thermal distortion in the materials.
- Brazing: Provides a reliable bond while maintaining the integrity of the heat pipe's structure.
- Sintering: Useful for creating porous structures that can enhance fluid movement within the pipe.
Each method has its pros and cons, influencing factors, like cost, time efficiency, and the environmental impact of the production process. Manufacturers must assess the specific requirements of each application to choose the optimal fabrication technique.
Quality Control Measures
Quality control in the manufacturing of flexible heat pipes ensures that each product meets stringent performance standards. Consistency is key in ensuring that pipelines can withstand operational pressures and thermal cycles without failure.
Quality control measures include:
- Dimensional Inspection: Accuracy in dimensions ensures proper fit and function.
- Leak Testing: Critical for confirming the integrity of the heat pipeβs seal.
- Thermal Cycling Tests: These assess how the heat pipe performs under extreme temperatures over time.
Implementing a robust quality control system not only minimizes the risk of defects but also enhances trust among customers. A detailed tracking system for defects can provide valuable data for continuous improvement in design and processes.
Innovative Production Methods
Innovative production methods play an essential role in advancing flexible heat pipe technology. Approaches such as additive manufacturing and automation are revolutionizing the way flexible heat pipes are produced.
Examples of these methods include:
- 3D Printing: Allows for complex shapes and customizable designs that were previously impossible with traditional methods.
- Automated Assembly Lines: These reduce human error and increase production efficiency, leading to lower costs and higher output rates.
- Robotic Processes: Robotics can handle precision tasks, ensuring consistency and deep accuracy in meddling with the materials.
Adopting these innovative production methods can lead to breakthroughs that redefine flexible heat pipes' capabilities in thermal management solutions. By leveraging such technologies, manufacturers can address the growing demand efficiently while providing high-performance products.
"The production landscape for flexible heat pipes is constantly evolving, emphasizing the need for both precision and adaptability in methods used to manufacture these essential components."
Applications of Flexible Heat Pipes
The discussion of flexible heat pipes is critical in understanding their varied applications in modern technology. These devices offer significant advantages in thermal management across numerous industries, making them essential in areas where heat dissipation is crucial. Their adaptability allows for integration into complex designs that demand both flexibility and efficient thermal performance.
In various applications, flexible heat pipes provide enhanced thermal conductivity, often surpassing traditional methods of heat dissipation. The lightweight nature of these systems also contributes to overall system efficiency. Furthermore, the adaptability of flexible heat pipes to different shapes and sizes broadens their utility, allowing engineers to utilize them in constrained spaces without losing performance.
Aerospace Industry
The aerospace sector benefits notably from flexible heat pipes. These components are vital for managing the heat generated by avionics and other onboard equipment. For instance, the compact design of satellites and aircraft necessitates innovative cooling solutions. Flexible heat pipes can navigate tight layouts, transferring heat efficiently away from critical components. This capability helps prevent overheating, which could lead to system failures or performance degradation.
Moreover, the lightweight properties contribute to the overall fuel efficiency of aircraft, which is an essential consideration for aerospace engineers. Their performance in extreme temperatures, along with resilience against vibrations during flights, makes them indispensable in this field.
Electronics Cooling
Flexible heat pipes are equally significant in the domain of electronics cooling. With the ongoing trend of miniaturization in electronics, devices are becoming denser and producing more heat. Here, flexible heat pipes play a crucial role in thermal management by distributing heat uniformly across components like CPUs and GPUs.
Implementation of these heat pipes leads to enhanced performance and longevity of electronic devices. For example, laptops and high-performance computing systems incorporate flexible heat pipes to keep components operating within optimal temperature ranges. Their integration can result in lower fan speeds and quieter operations, which is an increasing demand from consumers.
Automotive Sector
In the automotive industry, flexible heat pipes are gaining traction, especially in electric vehicles. These vehicles demand effective thermal management for batteries, inverters, and motors. Flexible heat pipes provide a reliable solution by ensuring that components remain within their ideal temperature zones, which directly influences both performance and safety.
Another application lies in exhaust heat recovery systems. By using flexible heat pipes, automakers can capture waste heat and convert it into usable energy, improving fuel efficiency. The reduction in thermal gradients also prolongs the life of sensitive electronic components embedded within various automotive systems.
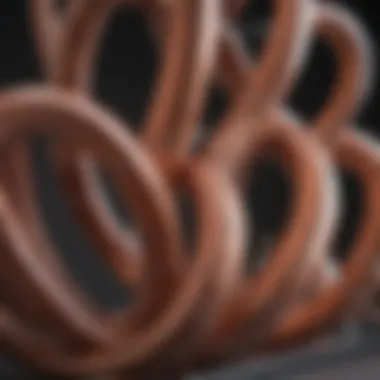
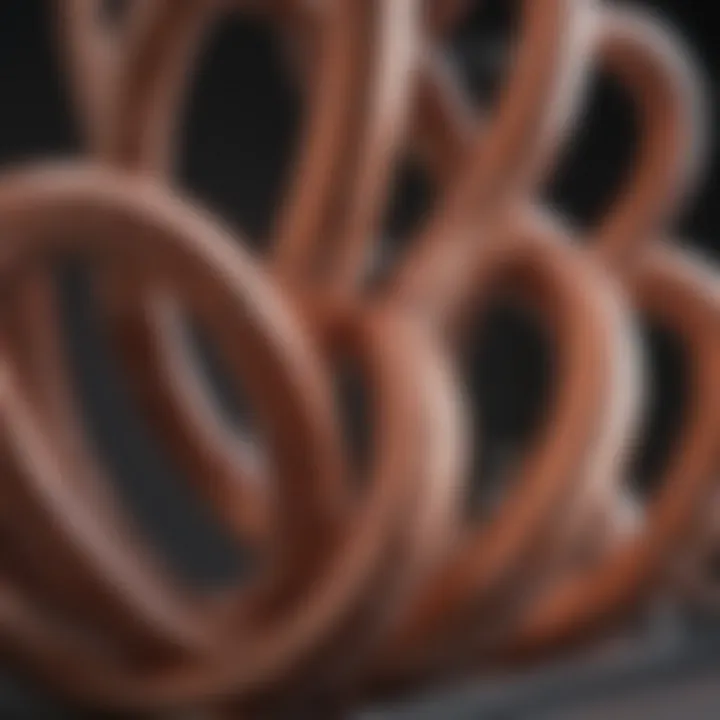
Energy Sector Applications
Lastly, the energy sector utilizes flexible heat pipes in renewable energy systems, particularly in solar thermal installations. These heat pipes facilitate efficient heat transfer from solar collectors to storage units, optimizing energy capture and usage. Their flexibility allows for installation in diverse configurations, adapting to various landscape and layout requirements.
Additionally, in geothermal energy applications, flexible heat pipes can help in heat exchange processes by transferring heat effectively from the earth to the surface systems. This adaptability aids in harnessing renewable energy sources more efficiently, aligning with global efforts for sustainable energy solutions.
"The importance of flexible heat pipes cannot be understated; they are key to modern thermal management solutions across varied industries."
In summary, the applications of flexible heat pipes span crucial industries such as aerospace, electronics, automotive, and energy. The ability to manage heat effectively while maintaining flexibility results in enhanced performance, safety, and energy savings. As technology continues to evolve, the relevance of flexible heat pipes will only grow, emphasizing their integral role in future innovations.
Performance Metrics for Flexible Heat Pipes
The efficient performance of flexible heat pipes is paramount in applications across various industries. Proper evaluation of performance metrics ensures they meet specific thermal management requirements. These metrics provide insights into their effectiveness in transferring heat, reliability under different conditions, and suitability for applications. Understanding these metrics delivers a comprehensive perspective on the capabilities and potential limitations of flexible heat pipes.
Thermal Conductivity Evaluation
Thermal conductivity is a cornerstone property of heat pipes, it dictates how efficiently heat is transferred. For flexible heat pipes, it is vital to assess the thermal conductivity since it directly affects the efficiency of thermal management systems. Evaluating thermal conductivity involves measuring how much heat passes through a material of a specific thickness in a given time. If a flexible heat pipe has low thermal conductivity, it may struggle with heat dissipation, impacting overall system performance.
In practical terms, flexible heat pipes must be analyzed in scenarios that mimic real-world conditions to understand their performance better. Any variations in the material or design can significantly influence outcomes. The effectiveness of flexible heat pipes can be benchmarked against rigid counterparts, while also considering flexibility as a factor that can improve adaptability in intricate designs, especially in aerospace or consumer electronics.
Pressure Drop Assessment
Pressure drop, which refers to the loss of pressure as fluid moves through a heat pipe, is another critical performance metric. A high pressure drop indicates an inefficient system, as it may require more energy to maintain flow. In flexible heat pipes, the assessment of pressure drop is vital since flexible configurations may lead to changes in fluid dynamics compared to their rigid counterparts.
Investigating pressure drop includes considerations of curvature, bends, and material interactions with the working fluid. Researchers often conduct tests under different operational conditions to determine how these factors influence performance. Flexible designs, while offering advantages such as compactness and lightweight, may encounter unique challenges with pressure management that need addressing for effective thermal transfer.
Reliability Testing
Reliability testing ensures that flexible heat pipes maintain performance over time under varying conditions. As they are used in mission-critical applications like aerospace or medical devices, it is essential to test for longevity and durability. Testing procedures often simulate extreme situations, including temperature fluctuations and mechanical stress. This evaluation informs engineers about potential failure modes, leading to better designs equipped to handle real-world demands.
The assessment process involves both accelerated life testing and long-term monitoring strategies. This helps ascertain not only how well the heat pipes perform initially but also how they age with time. Being proactive about reliability can help engineers minimize unexpected failures, thus enhancing the reputation and functional trust in flexible heat pipe technologies.
Comparative Analysis with Rigid Heat Pipes
Comparing flexible heat pipes with their rigid counterparts is essential to understand their unique benefits and challenges. This comparative analysis will draw attention to several key elements such as design differences, performance aspects, and application suitability. Each of these considerations not only highlights the adaptability of flexible heat pipes but also identifies their roles in various industries, helping to distinguish when one may be more suited than the other.
Design Differences
Flexible heat pipes fundamentally differ from rigid heat pipes in their structural design. A rigid heat pipe typically maintains a constant cross-section and shape, providing a stable framework for thermal transfer. In contrast, flexible heat pipes are designed with adaptability in mind. They can bend and conform to various geometries, which enhances their usability in constrained environments. This flexibility permits installation in complex layouts without sacrificing performance.
Key design distinctions include:
- Cross-sectional profiles: Flexible heat pipes may use variable profiles to optimize thermal performance while allowing for bending.
- Joint configurations: Flexible designs often incorporate specialized joints or connectors to accommodate movement without compromising integrity.
- Manufacturing techniques: The fabrication of flexible heat pipes can involve different methods deriving from material choices, such as using soft metals or polymers.
Despite their adaptability, this design flexibility can lead to structural compromises that must be evaluated in different applications.
Performance Aspects
In performance evaluations, flexible heat pipes and rigid heat pipes exhibit contrasting characteristics. The thermal efficiency of both types can achieve comparable performance under optimal conditions; however, flexible heat pipes may experience performance degradation when subjected to extreme bends or twists.
Performance differences include:
- Thermal conductivity: While flexible heat pipes can achieve good thermal conductivity, their effectiveness may decrease if the flexible sections become too sharply bent.
- Dynamic response: Flexible heat pipes can better manage varying thermal loads due to their construction. They are often suitable for applications that experience significant thermal cycling.
- Reliability: The reliability of performance for flexible heat pipes can be further influenced by wear and tear, especially in high-movement applications.
In any scenario, analyzing these performance aspects is vital for ensuring efficient thermal transfer solutions.
Application Suitability
Application suitability serves as a critical point in the comparative analysis of flexible and rigid heat pipes. Each type is tailored to different environments, dictated by design and performance aspects.
Flexible heat pipes excel in applications requiring integration into tight spaces or complex geometries, while rigid heat pipes are preferable in stable, fixed environments where alignment cannot change. Common uses include:
- Aerospace applications: Flexible heat pipes can be integrated in custom aircraft designs, adapting to tight contours where rigid options may fail.
- Portable electronic cooling: Devices such as laptops and smartphones benefit from flexible heat pipes that adjust to varying designs.
- Automotive applications: The ability to fit flexible heat pipes in compact configurations allows for better cooling solutions.
Overall, understanding these application suitability factors ensures that industry professionals can select the most appropriate heat pipe type for their specific needs.
"The right choice between flexible and rigid heat pipes can significantly enhance thermal management systems, optimizing performance in various engineering applications."
Challenges in Flexible Heat Pipe Technologies
The advancement of flexible heat pipes is met with several challenges that need thorough examination. Understanding these challenges is vital. They encompass manufacturing limitations, material constraints, and environmental impact considerations. Resolving these issues can enhance the effectiveness and applicability of flexible heat pipes across various industries.
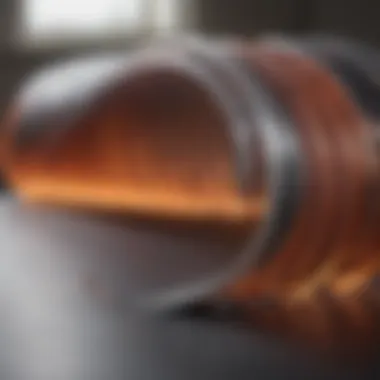
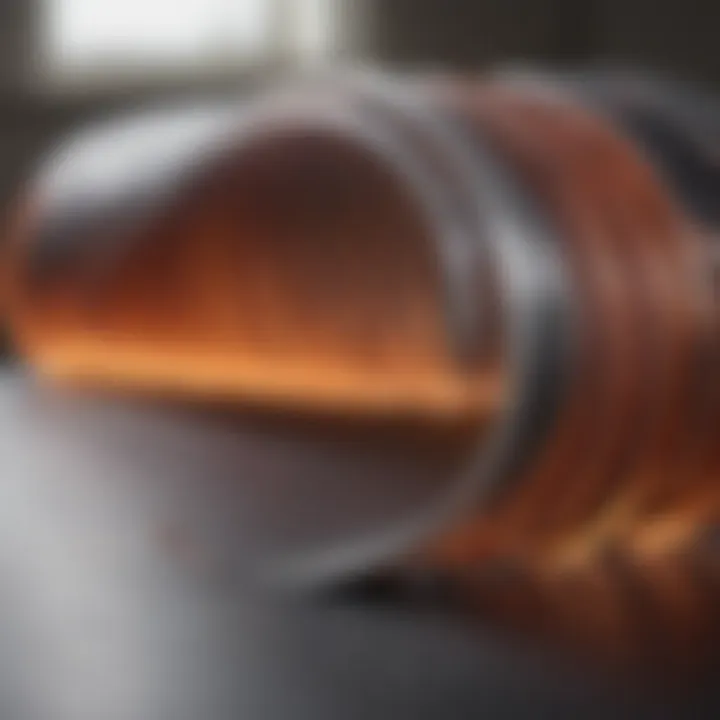
Manufacturing Limitations
The manufacturing process of flexible heat pipes involves precise engineering, which can lead to limitations. One such limitation includes the difficulty in maintaining consistency in the dimensions of the pipes during production. This variability can affect the thermal performance. Additionally, the bending and flexibility might require specialized equipment not commonly found in conventional heat pipe manufacturing setups. Such machinery can be costly and may contain a steep learning curve for workers. Also, ensuring the integrity of the sealed environment, critical for efficient operation, becomes challenging. Any inadvertent leaks during production can lead to a loss of working fluid, severely impacting performance.
Material Constraints
Material selection poses another significant hurdle in the realm of flexible heat pipes. The material must exhibit robust thermal properties while also being flexible enough to allow for bending and twisting. Currently used metals, such as copper and aluminum, may not always meet this dual requirement when subjected to the stress of repeated flexing. Furthermore, the compatibility of these materials with the working fluids is crucial. If the material corrodes or reacts with the fluid, the entire system can fail. Developing new alloys or composite materials is ongoing, yet they often come with high research and development costs, which can deter adoption in commercial applications.
Environmental Impact Considerations
The production and disposal of flexible heat pipes can lead to environmental concerns. The materials utilized in flexible heat pipes, particularly metals, require significant energy to extract and process. This results in a high carbon footprint during their lifecycle. Besides, many working fluids used in heat pipes can be harmful to the environment if released. It is crucial to conduct a lifecycle assessment to understand the environmental impact clearly. As industries lean towards sustainability, finding eco-friendly alternatives for both materials and fluids becomes essential. Continuous research is needed to innovate technologies that reduce environmental harm while still delivering optimal thermal management solutions.
To mitigate these challenges, collaboration between manufacturers, material scientists, and environmental experts is necessary to drive actionable solutions, ensuring the advancement of flexible heat pipe technologies without compromising environmental integrity.
Current Research Trends
Research trends in flexible heat pipes are critical to understanding their evolving role in various industries. Advancements in technology and materials science drive the need for continuous exploration in this field. This section highlights modern innovations, experimental performance studies, and the application of real-world case studies. Each aspect sheds light on the capabilities and future prospects of flexible heat pipes.
Novel Designs and Innovations
Recent advancements in design focus on enhancing the thermal efficiency and flexibility of heat pipes. One notable innovation is the development of composite structures that integrate various materials. This approach leads to improved thermal conductivity and mechanical properties. Researchers also experiment with geometrical configurations to optimize heat transfer rates. Examples include micro-structured surfaces that increase effective area for heat exchange, as well as spiral and wavy designs that enhance the capillary action within the pipes.
In a practical application, NASA has explored multiple innovative designs in aerospace, adapting flexible heat pipes for use in the next generation of spacecraft. These advancements showcase the need for heat management systems that can operate under varying conditions of pressure and temperature.
Experimental Studies in Performance
Experimental research on flexible heat pipes primarily assesses their thermal performance and reliability under real-world conditions. Testing often involves rigorous methods, such as thermal cycling tests, pressure drop assessments, and performance benchmarking against traditional rigid counterparts. The findings provide essential insights into operational limits and long-term durability.
One significant study indicated that flexible heat pipes maintain performance stability even under extreme bending scenarios. This performance is vital for applications in compact spaces, such as in electronic devices, where conventional cooling methods might be ineffective. Furthermore, the knowledge gained from these studies not only validates existing theories but also inspires future design modifications that further enhance performance.
Case Studies and Real-World Applications
The practical implementation of flexible heat pipes can be observed in several industries. In electronics, for example, flexible heat pipes improve thermal management in thin devices like laptops and smartphones. This ensures that components do not overheat, enhancing lifespan and reliability. A case study involving Appleβs MacBook series illustrated how integrating flexible heat pipes allowed for thinner designs without sacrificing cooling capability.
In the automotive sector, flexible heat pipes are gaining traction for use in electric vehicles. Studies have shown that these systems efficiently manage battery temperatures, improving overall efficiency and safety. Additionally, flexible heat pipes are implemented in renewable energy systems, effectively transferring heat from solar panels to storage solutions, thus promoting energy efficiency.
The continued focus on practical applications illustrates the versatility of flexible heat pipes in tackling modern thermal management challenges. Their ability to adapt to various environments and configurations paves the way for innovative solutions in the future.
Future Directions for Flexible Heat Pipes
The exploration of future directions for flexible heat pipes is pivotal in shaping their role in thermal management solutions across diverse industries. As technological advancements continue to evolve, understanding the implications of these developments is critical. This section emphasizes three main areas: advancements in materials science, integration with emerging technologies, and potential market expansions.
Advancements in Materials Science
Material selection is essential for enhancing the performance of flexible heat pipes. Innovations in materials science have made a significant impact on the efficiency and adaptability of heat pipes. Researchers are now investigating new materials that can withstand harsher conditions and offer better thermal conductivity.
A notable advancement is the development of nanostructured materials, which can improve thermal management by increasing surface area and facilitating better heat transfer. Alloy compositions, such as copper and aluminum, are being optimized to provide improved durability while maintaining flexibility. These advances have the potential to revolutionize how flexible heat pipes are utilized in industries like aerospace and electronics.
Integration with Emerging Technologies
The integration of flexible heat pipes with emerging technologies is essential for their future application. For example, in the realm of renewable energy, combining flexible heat pipes with solar technology may improve energy efficiency. Heat pipes can effectively transfer heat energy from solar collectors to storage systems, thus maximizing efficiency.
Moreover, flexible heat pipes are increasingly being integrated into wearable technology, providing efficient thermal management in compact designs. This integration highlights the adaptability of flexible heat pipes and their potential to meet the demands of modern applications.
Potential Market Expansions
As the demand for effective thermal management solutions grows, flexible heat pipes are well-poised for market expansion. Industries such as consumer electronics and electric vehicles are major markets where flexible heat pipes can play a vital role in thermal control, reducing overheating and improving performance.
Future research might focus on customizing flexible heat pipes for specific applications, tailoring their design and functionality to meet the requirements of different sectors. This adaptability opens up possibilities for new applications, driving innovation and addressing unique challenges in various markets.
"The flexibility in design and function not only enhances their applicability but also significantly boosts the efficiency of thermal systems across diverse fields."
Closure
The conclusion serves as a crucial section of this article by summarizing the essential insights regarding flexible heat pipes. It offers a clear perspective on their advantages, challenges, and future scope within thermal management applications. The importance of flexible heat pipes in modern engineering cannot be overstated. As industries increasingly seek efficiency and adaptability in thermal systems, flexible heat pipes emerge as a viable solution, addressing both performance and design flexibility.
In essence, flexible heat pipes provide engineers and designers with the opportunity to innovate in product design. Their versatile nature allows integration into constrained spaces often found in aerospace and electronics industries. The adaptability to incorporate advanced materials further enhances their thermal performance, making them suitable for a wide range of applications.
Summary of Key Points
- Versatility and Adaptability: Flexible heat pipes can be designed to fit various applications that necessitate unique thermal management solutions.
- Material Selection: The choice of materials is paramount in enhancing performance, with emerging technologies offering new possibilities.
- Manufacturing Techniques: Innovations in manufacturing processes ensure that these systems can be produced efficiently while maintaining high quality.
- Broad Applications: From aerospace to electronics, these heat pipes prove beneficial across multiple sectors.
- Future Trends: Ongoing research and development promise to push the boundaries of what flexible heat pipes can achieve.
Final Thoughts
As we conclude our exploration into flexible heat pipes, it becomes evident how integral these devices are to contemporary engineering contexts. By pushing the boundaries of traditional thermal management methods, they not only optimize performance but also foster creativity in design.
Future developments in this field are likely to be impactful, catering to industries that require increasingly sophisticated solutions. The convergence of advanced materials, innovative designs, and evolving manufacturing techniques will keep flexible heat pipes at the forefront of effective thermal management. Therefore, ongoing research and adaptation to new technologies will be critical to unlocking their full potential in future applications.
In sum, flexible heat pipes represent not just an advancement in engineering but a pivotal element in shaping the future of thermal management technology.