Mastering the Expected Delivery Date Formula
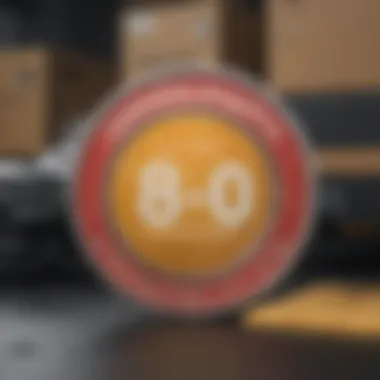
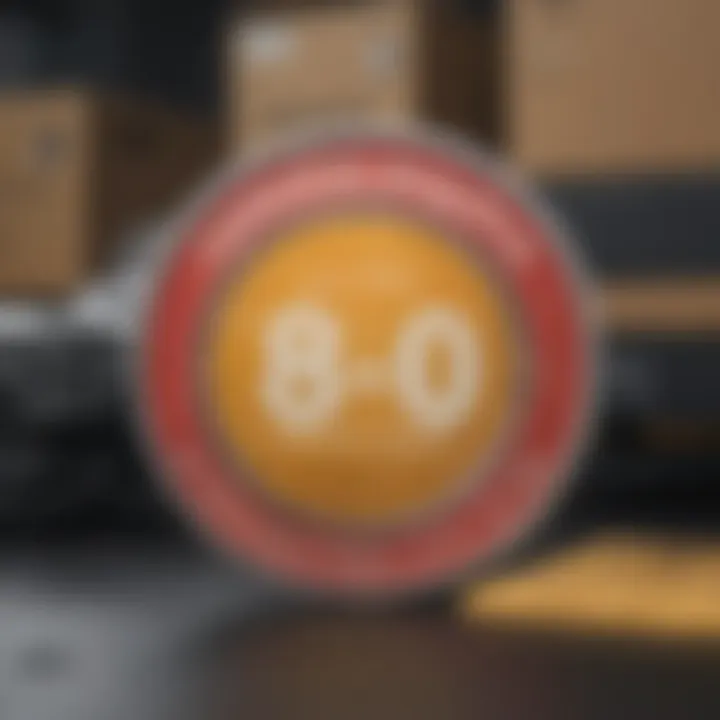
Intro
In the realm of logistics and supply chain management, the expected delivery date formula serves as a crucial instrument in determining when items will reach their intended destination. Understanding this formula is not only essential for efficiency but also plays a vital role in customer satisfaction. In today's fast-paced market, where demand for speed and accuracy is ever-increasing, a grasp of the expected delivery date can significantly impact business operations.
Research Overview
The exploration of the expected delivery date formula encompasses various components. This research aims to shed light on how these components interact, their applications in real-world scenarios, and the potential challenges faced by practitioners. By delving into the mechanics of the formula, we seek to uncover insights that can aid businesses in refining their logistics processes.
Summary of Key Findings
- Components of the Formula: The formula primarily involves factors like processing time, transit time, and safety stock. Each of these variables contributes to calculating an accurate expected delivery date.
- Applications: Companies across sectors such as retail, manufacturing, and e-commerce utilize this formula to optimize their supply chains and enhance service levels.
- Common Challenges: Despite the usefulness of the expected delivery date formula, obstacles such as inaccurate data and unforeseen disruptions can hinder effective implementation.
Research Objectives and Hypotheses
The objective of this article is to provide an in-depth understanding of the expected delivery date formula. The hypotheses guiding this research posit that a clear comprehension of the formula will lead to more efficient logistics operations and heightened customer satisfaction.
Methodology
This study employs a comprehensive approach to analyzing the expected delivery date formula. Data was collected from various industries to validate the application of the formula in practical settings.
Study Design and Approach
The study was designed to gather qualitative insights along with quantitative data. This mixed-methods approach allows for a robust understanding of how businesses apply the expected delivery date formula in real-life scenarios.
Data Collection Techniques
Data was obtained through surveys and interviews with logistics professionals. This method provided firsthand accounts of challenges and successes in using the expected delivery date formula, enriching the overall analysis.
Overview of Expected Delivery Date Formula
In the realm of logistics, the expected delivery date formula stands as a cornerstone for planning and operations. This formula aids businesses in estimating when products will reach their destination. An accurate expected delivery date can optimize supply chain management and enhances customer satisfaction. It also helps in resource allocation, allowing companies to better manage inventory levels and transportation schedules.
Definition of Expected Delivery Date
The expected delivery date is a predicted time frame in which a product is anticipated to arrive at a certain location. This date takes into account various factors, such as production schedules, shipping times, and potential delays. It serves as a predictor, enabling businesses to set realistic timelines for both themselves and their customers. Accurate delivery dates are essential for maintaining trust and transparency in the customer relationship.
Importance in Logistics
The calculation of the expected delivery date is crucial for several reasons. First, it aids in setting proper customer expectations. When buyers know when to expect their orders, they can plan accordingly. Second, logistics companies can optimize their operations. By understanding when deliveries are due, they can allocate resources more efficiently, such as transportation and workforce management.
An accurate expected delivery date is not just a number; it is a commitment to the customer.
Moreover, the formula can help identify potential bottlenecks in the supply chain. If delays are anticipated, companies can proactively address them before they become larger issues. In a competitive market landscape, the ability to provide reliable delivery information can differentiate a company from its rivals, thus enhancing customer loyalty and confidence.
Components of the Formula
Understanding the components of the expected delivery date formula is crucial for achieving precision in logistics and supply chain management. This section will explore the fundamental elements involved and their implications. Each of these components plays a significant role in shaping the efficiency and reliability of delivery estimates. They are not only important for operational success but also for maintaining customer satisfaction.
Understanding Lead Time
Lead time is the total time required from the initiation of an order to the arrival of the product at its destination. This timeframe encompasses various stages, such as manufacturing, processing, and shipping. Knowing the lead time helps businesses anticipate when a product will be available for delivery. It is essential to account for lead time reservations so that planning is both realistic and effective. Variations in lead time due to supplier delays or unexpected demand spikes can significantly impact the expected delivery date.
Role of Production Time
Production time specifically refers to the duration required to manufacture a product. This component can differ based on factors like the complexity of the product and the efficiency of the production process. High production times can delay overall delivery if they are not factored into the expected delivery date formula. Therefore, understanding how long it takes to produce each item is vital for accurate delivery scheduling. For example, custom orders typically take longer to fulfill compared to standard stock items.
Impact of Shipping Time
Shipping time measures how long it takes for goods to be transported from one location to another. It varies based on distance, carrier, and transportation mode. Factors like weather conditions and carrier capacity can lead to fluctuations in shipping time. For an accurate expected delivery date, businesses must use reliable estimates for shipping times. This not only helps businesses plan effectively but also sets correct expectations among customers regarding delivery.
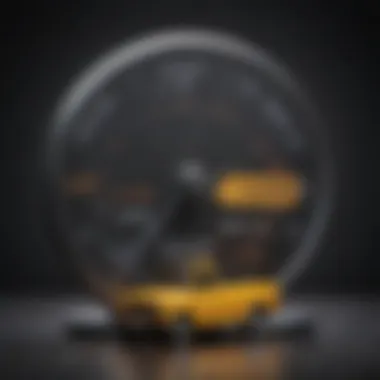
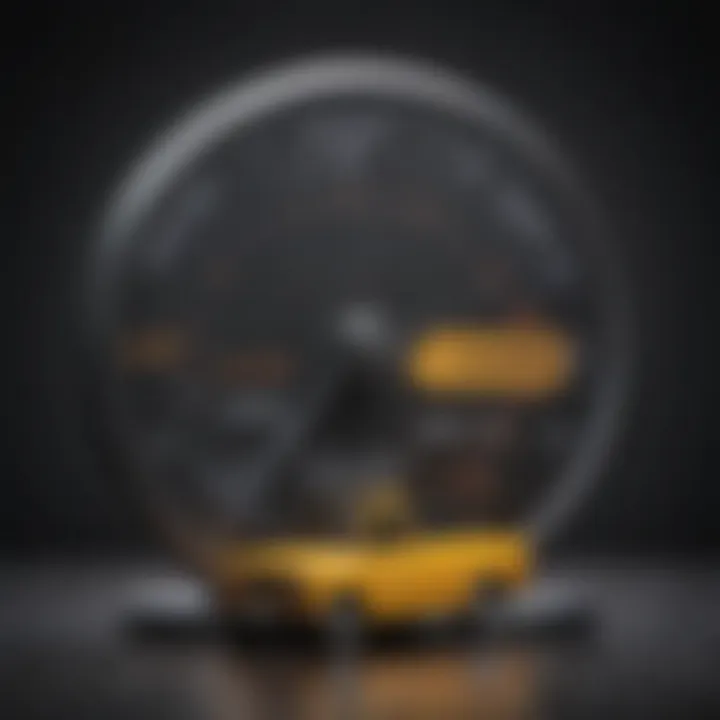
Influence of Handling Time
Handling time involves the duration it takes to prepare an item for shipment. This includes picking, packing, and labeling processes. Often overlooked, handling time is crucial for ensuring that goods are shipped correctly and efficiently. Reducing handling times can directly improve the overall delivery timeframe, allowing businesses to provide better service. Efficient handling practices can minimize delays and shorten the time it takes between order and delivery.
Calculating the Expected Delivery Date
Calculating the expected delivery date is crucial in logistics and supply chain management. An accurate expected delivery date allows companies to align their operations effectively, enhance customer satisfaction, and manage expectations. This date ensures that both the customers and the organization have a clear understanding of when goods will arrive, thus reducing confusion and improving service quality.
Accurate calculations consider various factors, such as lead time, shipping time, and handling time, discussed earlier.
These elements together create a framework that businesses rely on to ensure timely deliveries. Implementing a systematic approach to calculate the expected delivery date helps organizations mitigate risks associated with delays, enabling them to maintain a competitive edge.
To facilitate this understanding, letβs explore the steps involved in the calculation process.
Step-by-Step Calculation Process
The calculation of the expected delivery date can be understood as a sequential process. Each step involves specific actions that build on the previous one. The steps include:
- Gathering Data: Collect all relevant data, such as production time, lead time, shipping routes, and any other relevant metrics.
- Calculating Total Time: Sum up the lead time, production time, shipping time, and handling time. The formula to follow is:
- Determining Start Date: Identify the order placement or manufacturing start date.
- Establishing Expected Delivery Date: Add the total time calculated previously to the identified start date. This will yield the expected delivery date.
This structured approach to calculating the expected delivery date ensures that all variables are taken into account.
Utilizing Technology for Calculations
In today's digital age, technology plays a vital role in optimizing the calculation process. Companies utilize various software tools and platforms that enhance accuracy and efficiency. These solutions often offer:
- Integrated Systems: These systems combine inventory, order management, and logistics data, enabling real-time tracking of all elements involved.
- Predictive Analytics: Programs capable of analyzing historical data can provide estimates based on trends and patterns, offering organizations a more accurate prediction of delivery dates.
- User-Friendly Interfaces: Many platforms come with graphical user interfaces that allow users to input data without deep technical knowledge.
Such technology not only improves the calculations but also reduces the potential for human error, a frequent source of disruption.
Manual vs. Automated Methods
When it comes to calculating expected delivery dates, businesses often face a choice between manual and automated methods. Below are some comparisons:
- Manual Methods:
- Automated Methods:
- High dependency on human input and oversight.
- Easier for small-scale operations, where the complexity is low.
- Tends to be time-consuming and prone to errors if not monitored closely.
- Designed to handle large datasets quickly and efficiently.
- Integrate with other systems to provide comprehensive insight.
- Regular updates and adjustments ensure accuracy, adapting to changing conditions.
In summary, while manual calculations may still have their place, the precision and efficiency of automated methods often make them the preferred choice in today's fast-paced logistics environment.
Applications Across Industries
The expected delivery date formula serves as a crucial tool across multiple sectors. Understanding its applications enhances logistical efficiency and improves customer satisfaction. Each industry brings its own unique nuances and demands, making the mastery of this formula essential for success. This also means tracking various variables that influence delivery schedules. The benefits stem from using this formula effectively, which can lead to optimized operations, better supply chain management, and ultimately, stronger customer relationships.
Retail Sector Utilization
In retail, the expected delivery date formula helps in managing customer expectations effectively. Retailers often deal with a high volume of orders, making it necessary to provide accurate delivery timelines. Using the formula allows retailers to analyze lead times, shipping times, and potential delays. This ability to communicate realistic delivery time frames directly impacts customer satisfaction. When customers are informed about their orders, it decreases anxiety regarding product arrivals, leading to a more positive shopping experience. Additionally, having a reliable way to calculate delivery dates can streamline operational decisions related to inventory and reorder cycles.
Manufacturing Insights
In manufacturing, the expected delivery date formula plays a key role in production planning. Through careful calculation, manufacturers can predict when products will be ready for shipment. This ensures that raw materials are sourced correctly and production schedules align with delivery deadlines. The formula helps in balancing production times with capacity, preventing bottlenecks. Moreover, an accurate expected delivery date can enhance communication with suppliers and clients, ensuring a smooth operational flow. Overall, this formula is an integral part of maintaining production efficiency and meeting market demand.
E-commerce Considerations
The e-commerce sector relies significantly on the expected delivery date formula for its success. Online shoppers prioritize fast and accurate deliveries. By implementing the formula, e-commerce businesses can provide precise delivery estimates and streamline fulfillment processes. This not only aids in customer retention but also in attracting new customers. E-commerce platforms can analyze historical data to fine-tune their delivery estimates continuously. As the delivery dates remain a key selling point, consistently meeting or exceeding these expectations can greatly enhance brand reputation and competitiveness.
Healthcare Applications
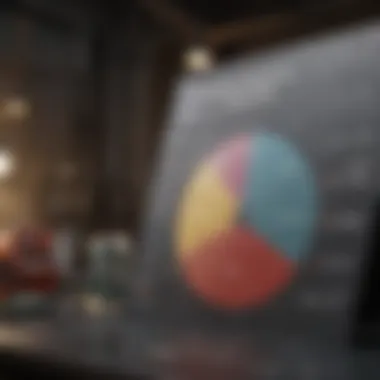
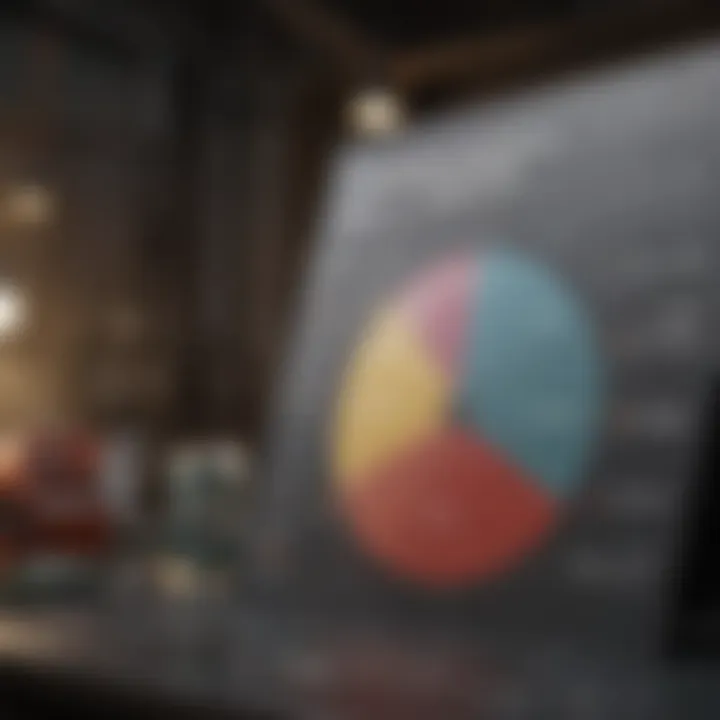
In healthcare, the expected delivery date formula has far-reaching implications. Medical supplies and equipment must arrive on time to ensure patient safety and effective treatment. The formula assists healthcare facilities in managing supply chains critical to patient care. By precisely calculating delivery dates, hospitals can better coordinate their inventory levels with patient demand. This leads to a reduction in wasted resources and ensures that treatment is administered without unnecessary delays. Furthermore, understanding these timelines helps healthcare providers maintain clear communication with suppliers as well as stakeholders.
Challenges in Using the Expected Delivery Date Formula
The expected delivery date formula serves as a vital tool for logistics professionals, facilitating the management of shipping times and enhancing overall operational efficiency. However, its practical application is often fraught with challenges that can undermine the accuracy and reliability of delivery estimates. These challenges span various dimensions, including variability in lead times, disruptions occurring in the supply chain, and issues stemming from inaccurate data inputs. Understanding these specific challenges is crucial for businesses seeking to optimize their supply chain processes and maintain high levels of customer satisfaction.
Variability in Lead Times
Lead times are the duration between the initiation of the production and the completion of the product delivery. One major challenge faced by logistics teams is the inherent variability in these lead times. This variability can result from a wide range of factors such as fluctuating demand, production delays, or unexpected machine failures. For instance, if a supplier typically delivers materials within five days but experiences a sudden delay due to technical issues, it can lead to a ripple effect, disrupting the entire delivery schedule. Such inconsistencies make it difficult for businesses to provide accurate expected delivery dates.
To address this, companies can enhance their inventory management systems to account for possible lead time fluctuations. By implementing a buffer period in their timelines, or using tools that enable the monitoring of production metrics, firms can improve their forecasting and better manage customer expectations.
Disruptions in Supply Chain
Supply chains are complex networks influenced by numerous external factors, making them susceptible to disruptions. Events such as natural disasters, geopolitical tensions, or even a pandemic can severely impact supply chain efficiency and, consequently, the expected delivery dates. For instance, consider the consequences of the COVID-19 pandemic: many manufacturers faced shutdowns, while logistical bottlenecks arose, delaying shipments considerably.
Businesses must adopt agile strategies to mitigate the impact of such disruptions. Building strong relationships with multiple suppliers and diversifying sourcing strategies can serve as a safeguard against reliance on any single source. Additionally, organizations should leverage digital platforms to gain visibility into their supply chain, facilitating quicker responses to unforeseen changes.
Inaccurate Data Inputs
Another significant challenge lies in the accuracy of data inputs used to calculate the expected delivery date. Inaccurate or outdated information regarding inventory levels, production schedules, or shipping times can lead to misleading estimates. This can create problems in customer service, as clients may receive unrealistic expectations regarding when they will receive their goods.
To improve data integrity, companies should invest in robust data management systems that consolidate information from various departments and sources. Regular audits and validations of data inputs are essential to maintaining accuracy, and training staff on the importance of data entry can further reduce errors. By prioritizing data accuracy, firms can strengthen the reliability of their expected delivery date calculations, resulting in greater customer satisfaction.
"Accurate data is the cornerstone of efficient supply chain management. Without it, even the best strategies will falter."
In summary, while the expected delivery date formula is instrumental in logistics, it is imperative to acknowledge and navigate the challenges associated with it. Addressing lead time variability, managing potential supply chain disruptions, and ensuring data accuracy are crucial components of maintaining effective delivery estimates. By implementing targeted strategies, businesses can overcome these challenges and enhance their operational efficiencies.
Best Practices for Reliable Calculations
Reliable calculations of the expected delivery date are critical in logistics and supply chain management. These calculations help businesses manage customer expectations, optimize inventory levels, and enhance overall efficiency. By following best practices, organizations can minimize errors and increase the accuracy of their delivery date estimates. This section outlines essential practices to ensure reliable calculations.
Data Accuracy and Consistency
Data accuracy plays a fundamental role in calculating expected delivery dates. Inaccurate data can lead to misleading results that may frustrate customers and disrupt logistics. Maintaining high levels of accuracy involves regularly verifying and updating the data entered into the calculation system. This includes information related to lead times, production schedules, and shipping routes.
Consistency in how data is collected and used across the organization is equally important. When all stakeholders adhere to the same standards and methods for data entry and processing, the likelihood of errors is significantly reduced. To achieve this consistency:
- Establish clear data entry protocols.
- Train employees on the importance of data integrity.
- Conduct regular audits of the collected data to identify discrepancies.
By ensuring strong data accuracy and consistency, businesses can rely on their expected delivery date calculations with greater confidence.
Regular Review and Adjustment
The dynamic nature of logistics means that various factors can affect delivery dates. Regular review and adjustment of calculations are crucial to adapt to any changes. Variables such as supply chain disruptions, seasonal fluctuations, and alterations in customer demand necessitate continuous monitoring.
Organizations should implement a systematic process for reviewing delivery date calculations. This process can include:
- Monthly or quarterly assessments of lead times and shipping durations.
- Meetings among supply chain personnel to discuss any new challenges or updates affecting delivery dates.
- Updating the calculation model based on historical performance data.
By being proactive in reviewing and adjusting calculations, companies will better position themselves to meet customer expectations and maintain service quality.
Leveraging Historical Data
Historical data serves as a valuable resource in enhancing the reliability of expected delivery date calculations. Analyzing past performance helps organizations identify patterns and make informed predictions about future deliveries. The importance of historical data can be summarized as follows:
- Identification of Trends: Trends in lead times, production delays, and shipping times can be recognized and accounted for in future calculations.
- Improved Estimations: By relying on real data from past experiences, businesses can refine their formulas to produce more accurate estimates.
- Risk Assessment: Historical data can also highlight potential risks in the supply chain, allowing for better contingency planning.
To effectively leverage historical data, businesses should:
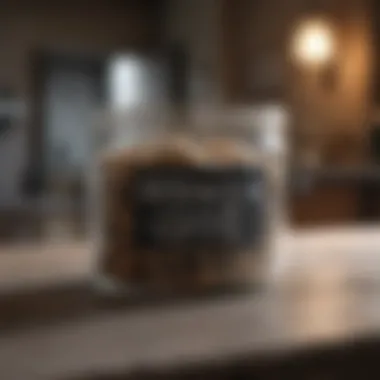
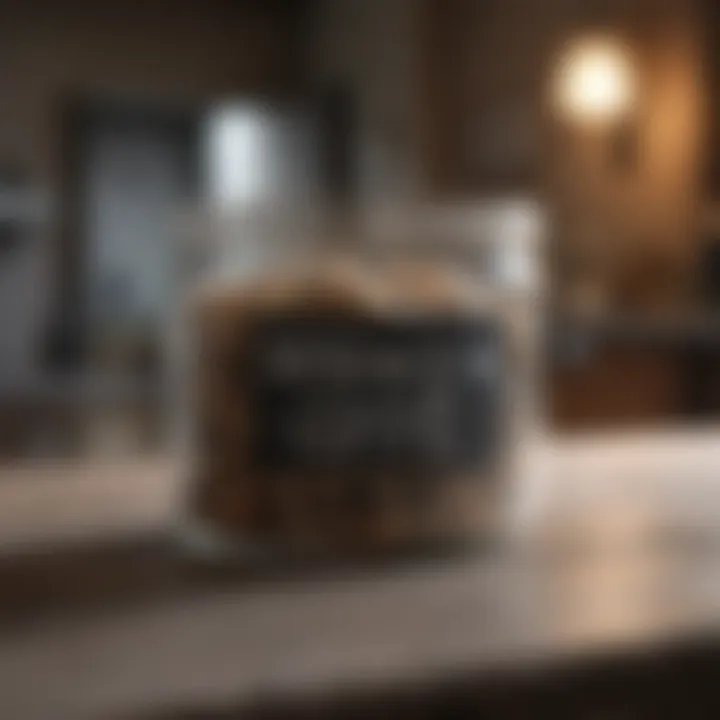
- Collect and archive relevant data systematically.
- Use data analysis tools to evaluate historical trends.
- Integrate this data into calculation processes as a base for future predictions.
Overall, best practices in calculating expected delivery dates help organizations navigate the complexities of logistics effectively. By focusing on data accuracy, regular reviews, and leveraging historical insights, businesses can improve their operational efficiency and enhance customer satisfaction.
"Reliability in delivery calculations can define the success of a logistics operation."
For further reading, you may refer to resources like Wikipedia or Britannica.
Impact on Customer Satisfaction
Accurate delivery estimations hold several key benefits:
- Enhanced Customer Experience: Customers feel valued when they receive their orders on time. This fosters loyalty and can lead to positive reviews.
- Reduced Complaints: Delivering on time minimizes grievances that may arise from misunderstandings about delivery timelines.
- Competitive Advantage: Businesses that consistently meet or exceed delivery expectations distinguish themselves in a crowded marketplace.
Companies must consider various elements that play into the impact on customer satisfaction when using the expected delivery date formula.
Meeting Customer Expectations
In logistics, meeting customer expectations goes beyond simply delivering products on time. It involves clear communication about potential delays and fostering realistic expectations right from the outset. Customers appreciate transparency. If a company is able to provide an accurate date and manage expectations effectively, it enhances customer satisfaction significantly. This can lead to an increase in customer loyalty and future business.
Here are some strategies to meet those expectations:
- Communicate clearly and promptly with clients regarding any changes affecting delivery.
- Utilize data from previous orders to provide more accurate delivery estimates.
- Present clear timelines on websites or order confirmations, which include possible delays.
Building Trust Through Transparency
Transparency in business operations is essential for fostering trust among customers. By clearly outlining how delivery estimates are calculated, companies can demystify the process and empower customers with knowledge. This transparency invites a stronger relationship between the business and its clientele. Customers are more likely to trust businesses that openly communicate potential issues or delays, further enhancing satisfaction.
To build trust through transparency:
- Share methodologies behind the expected delivery date formula openly. This might include sharing factors like production time or lead time.
- Maintain open-lines of communication, informing customers of any potential changes.
- Provide real-time tracking for shipments, allowing customers to stay updated about their packages.
Transparency not only keeps customers informed but also allows for better management of their expectations. It reflects a commitment to quality service and fosters a sense of reliability.
Overall, the impact of the expected delivery date formula on customer satisfaction cannot be overstated. By effectively applying this formula and adhering to best practices such as clear communication and transparency, businesses can significantly enhance their customer experience, ultimately driving growth and loyalty.
Future Trends in Delivery Date Calculation
The landscape of logistics and supply chain management is evolving rapidly. Future trends in delivery date calculation will greatly influence how organizations manage their operations and enhance customer satisfaction. As technological advancements reshape the industry, understanding these trends becomes crucial.
Adoption of Artificial Intelligence
Artificial intelligence (AI) is transforming various sectors, and delivery date calculation is no exception. With AI, businesses can analyze vast amounts of data to predict expected delivery dates more accurately. This technology helps in optimizing lead times by processing historical delivery performance, real-time traffic conditions, and potential disruptions. For instance, machine learning algorithms can improve prediction accuracy over time by learning from past data patterns.
Moreover, AI can automate many processes involved in calculating delivery dates. This efficiency reduces manual errors and speeds up the decision-making process. Not only does this lead to more reliable delivery estimates, but it also allows companies to focus on strategic initiatives rather than everyday calculations. AI-driven systems can even adapt in real-time to sudden changes in orders or shipment volumes, maintaining accuracy under varying conditions.
"The integration of AI in logistics can redefine the efficiency of delivery date calculations by minimizing human error and maximizing adaptability."
Integration of Real-Time Data
The use of real-time data is another emerging trend in delivery date calculation. Businesses are increasingly relying on live data streams from various sources, such as GPS tracking, weather conditions, and traffic updates. By integrating these data points, logistics teams can make informed decisions that impact delivery schedules.
This integration provides a more dynamic approach to calculating expected delivery dates. For example, if a shipment is delayed due to traffic, real-time data can immediately update the estimated delivery window, informing all stakeholders. Companies that leverage real-time data can enhance transparency and trust with their customers, as they provide accurate and timely updates on delivery status.
The implementation of Internet of Things (IoT) devices can significantly contribute to this trend. These devices can provide valuable insights into the logistics process and help track shipments accurately. The combination of IoT technology with artificial intelligence and machine learning will lead to more advanced data-driven decision-making.
Closure
The conclusion of this article serves to consolidate the importance of the expected delivery date formula within the logistics and supply chain landscape. Understanding this formula is crucial for various reasons. It provides a structured approach to determining delivery dates, which can significantly impact operational efficiency.
An effective expected delivery date formula minimizes uncertainty and helps businesses plan their operations better. Accurate calculations enable companies to allocate resources effectively, preemptively address potential delays, and enhance customer communication. Furthermore, a reliable predicted delivery date can lead to improved customer satisfaction as clients gain confidence in the company's ability to meet their expectations.
Summary of Key Points
To summarize the main points discussed:
- The expected delivery date formula is central to the logistics field, ensuring streamlined processes.
- Key components include lead time, production time, shipping time, and handling time, which collectively inform delivery predictions.
- Errors in data input or inconsistencies can jeopardize the accuracy of calculations.
- Adopting best practices such as leveraging historical data can enhance reliability in delivery estimations.
- Future trends like the use of artificial intelligence and real-time data integration promise to optimize delivery date calculations further.