Exploring Aluminum 3D Filament: Uses and Benefits
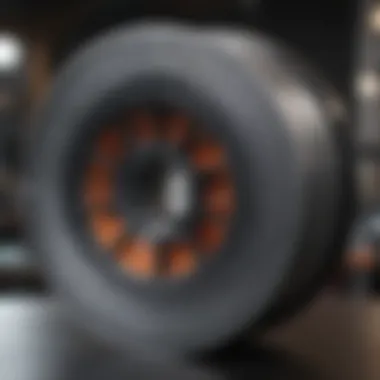
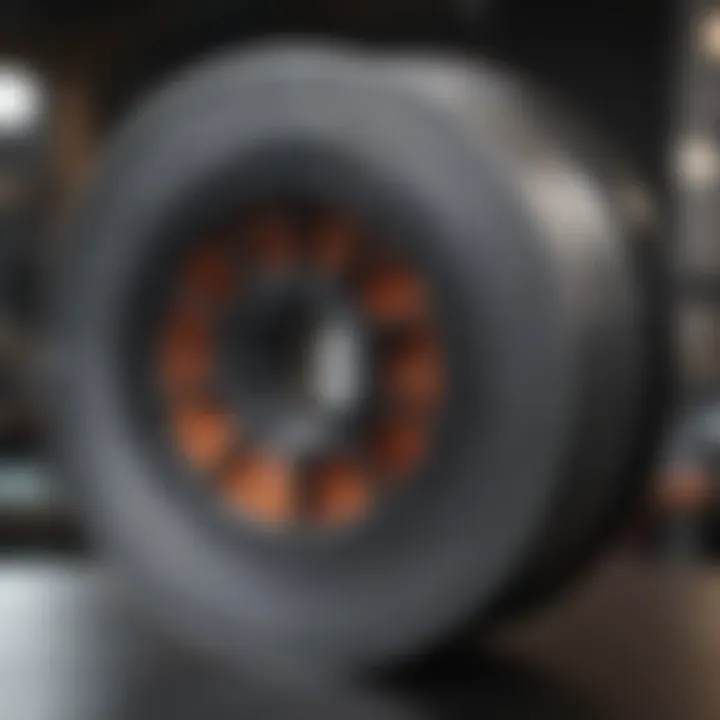
Intro
In the rapidly evolving landscape of 3D printing, aluminum filament stands as a noteworthy player. It is not just another material but a transformative substance that enables various innovations across multiple industries. As technology marches forward, the focus on lightweight yet sturdy materials becomes crucial, and aluminum fits the bill perfectly.
Understanding how aluminum filament works opens up new avenues for designers and engineers. Whether for aerospace components or automotive parts, the versatility it offers is impressive. Despite its advantages, utilizing aluminum filament comes with its share of challenges. From the production process to post-processing, the intricate details of working with this specific material require careful consideration.
By taking a closer look at the properties, applications, advantages, and challenges of aluminum 3D filament, we aim to furnish students, researchers, educators, and professionals with a well-rounded view of the topic. This exploration will shed light on why aluminum filament is becoming increasingly relevant in modern engineering and manufacturing.
Preamble to Aluminum 3D Filament
In a world that constantly seeks innovation and efficiency, aluminum 3D filament emerges as a significant contender in the realm of additive manufacturing. Many industries such as aerospace, automotive, and industrial design are often tethered to traditional manufacturing techniques, but the promise of aluminum filament invites a fresh perspective. This introduction will lay the groundwork, highlighting the unique qualities that distinguish aluminum from other materials while foreshadowing its future potential in various applications.
Definition and Overview
At its core, aluminum 3D filament is a composite material used to create three-dimensional objects through additive manufacturing. The filament typically contains aluminum powders blended with a polymer base, enabling it to be fed through the extruder of a 3D printer. This combination aims to harness the lightweight and corrosion-resistant properties of aluminum while providing the plasticity required for 3D printing. The result is a material that not only retains the beneficial properties of aluminum but also adapts well to 3D printing, making it highly versatile for multiple applications.
In terms of properties, aluminum filament presents an enticing high strength-to-weight ratio, which mirrors some of aluminum's inherent characteristics. This feature is crucial when creating parts that need to be both robust and lightweight, such as components in aerospace machines or automotive frames. Moreover, its thermal conductivity and resistance to high temperatures make it a fitting choice for applications demanding heat resistance. Thus, it is imperative to understand the definition and overview of aluminum filament as it sets the stage for its role in modern engineering.
Historical Context of 3D Printing with Aluminum
The history of using aluminum in 3D printing can be traced back to the broader developments in additive manufacturing. While the initial focus of 3D printing revolved around plastics like PLA and ABS, innovators began recognizing the potential of metals, particularly aluminum, in the mid-2000s. Early attempts were fraught with challenges, mainly due to the difficulty of achieving stable print qualities with metal-based filaments.
As technology progressed, specialized techniques emerged, facilitating the use of aluminum for 3D printing. Researchers and engineers grappled with issues such as thermal deformation and layer adhesion, which plagues many metal 3D printing processes. However, the introduction of advanced alloy formulations and optimized printing parameters began to surmount these roadblocks, allowing aluminum filament to gain traction within various industries.
Today, you’ll find electronics firms, aerospace engineers, and automotive manufacturers employing aluminum filament, reflecting its evolution from a nascent idea to a key player in the manufacturing landscape. With ongoing research and development aimed at refining the material’s properties and printing capabilities, the course of aluminum in 3D printing is on a promising trajectory.
"Aluminum filament brings not only versatility but also innovation, fundamentally changing how we think about material engineering in 3D printing."
In summary, the importance of aluminum 3D filament cannot be overstated. Its unique combination of properties, rooted in a historical context of evolving technology, demonstrates its potential impact across various fields. Understanding the implications of aluminum in additive manufacturing lays a strong foundation as we move forward into its applications, challenges, and advantages in subsequent sections.
Understanding Aluminum as a Material
In the context of 3D printing, aluminum stands out as a material of significant interest. Its combination of properties offers tangible benefits for diverse applications. When understanding aluminum as a material, it's crucial to appreciate its unique characteristics and how they align with the requirements of modern manufacturing. This segment will explore aluminum's physical and chemical properties, and compare them with other materials commonly used in 3D printing.
Physical and Chemical Properties of Aluminum
Aluminum, as an element, is known for its light weight coupled with impressive strength. Being a non-ferrous metal, it boasts excellent corrosion resistance, which is critical for parts exposed to various environmental factors. Its malleability allows it to be formed into intricate shapes without cracking, making it ideal for additive manufacturing where complex geometries are common. The melting point of aluminum is relatively low compared to steel, allowing for easier processing, and its thermal conductivity makes it a good candidate for applications requiring efficient heat dissipation.
In terms of chemical properties, aluminum can form a thin oxide layer on its surface that protects it from further oxidation. This protective layer enhances its durability in many applications. Thus, when evaluating aluminum for 3D printing, both its physical and chemical attributes stand out as essential qualities that contribute to its effectiveness in creating lightweight yet strong components.
Comparison with Other Materials
When comparing aluminum with other materials used in 3D printing, several key aspects emerge.
Strength Ratings
Strength ratings are often a pivotal consideration in any engineering application. Aluminum exhibits a favorable strength-to-weight ratio, making it a popular choice for industries that prioritize performance without the bulk. Unlike materials such as plastics, which may lose structural integrity under stress, aluminum retains strength even at lower thicknesses. This unique feature provides designers flexibility, facilitating the creation of sturdy components that don’t compromise on weight. Components such as brackets or supports can leverage aluminum's reliable strength without the penalty of additional mass.
Weight Efficiency
Weight efficiency can be seen as a game-changer in many sectors, particularly in aerospace and automotive industries where every gram counts. Aluminum's low density allows for significant weight savings while still ensuring robustness. This property not only enhances fuel efficiency in vehicles but also improves overall performance in aerospace applications. For instance, reducing weight can lead to lower emissions and operational costs, making aluminum an attractive choice when optimizing for efficiency.
Cost Effectiveness
Cost effectiveness plays a significant role in the decision-making process for materials selection. Although aluminum can be more expensive than some plastics, its longevity and durability often lead to reduced lifecycle costs. When factoring in the costs associated with repairs and replacements, aluminum surfaces as a cost-effective option in many instances. Furthermore, its recyclability adds another layer of value, as it can be repurposed without significant loss of quality.
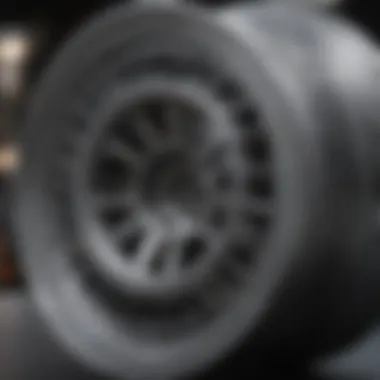
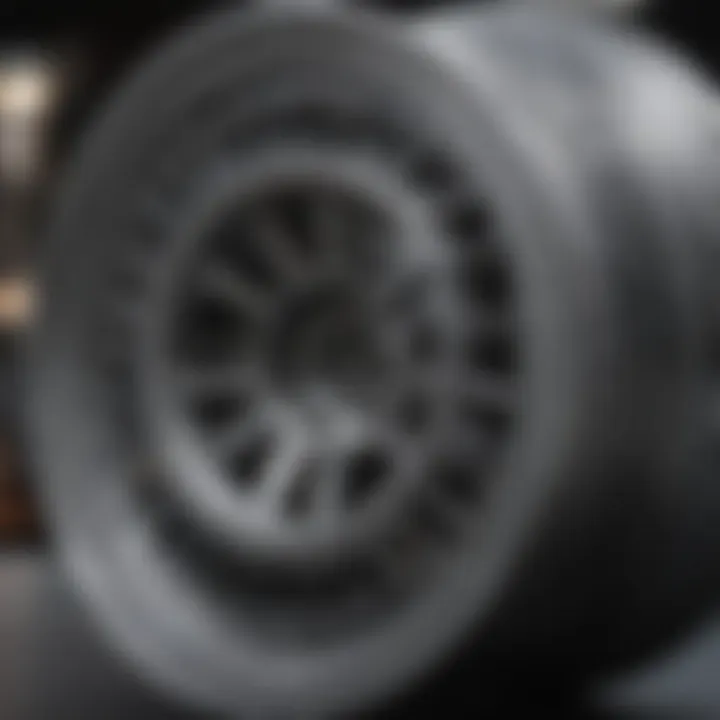
Aluminum's properties provide a compelling case for its use in 3D printing applications, showcasing how its strengths can address specific industry needs. Understanding these comparisons not only enhances our knowledge of this material but also guides decisions in manufacturing processes that rely on optimal material selection.
"In manufacturing, choosing the right material can be as crucial as the design itself; aluminum offers a balance that's hard to ignore."
Overall, recognizing aluminum's physical and chemical properties, along with its advantages over competing materials, creates a foundational understanding that is essential for leveraging this material in 3D printing applications.
Manufacturing Process of Aluminum 3D Filament
Understanding the manufacturing process of aluminum 3D filament is vital to comprehending its potential and limitations in additive manufacturing. This process encompasses several key steps, from sourcing raw materials to producing high-quality filament suitable for 3D printing. The choice of materials and methods utilized in manufacturing directly influences the performance characteristics of the final product, making this section essential for anyone seeking to leverage aluminum filament in industrial applications.
Raw Material Sourcing
When it comes to aluminum 3D filament, sourcing the right raw material is the first and arguably most critical step. The purity and quality of aluminum used in filament production can significantly affect the strength and durability of the printed products. Most producers prefer high-grade aluminum alloys, which offer a combination of strength and plasticity. These alloys must be obtained from reputable suppliers who adhere to strict quality controls to guarantee that the materials meet industry standards.
In addition, sourcing involves not just the quality of aluminum but also environmental considerations. Sustainable practices in mining and recycling aluminum make it a more appealing choice among manufacturers concerned about their ecological footprint. Therefore, the relationship with suppliers and the sourcing strategy is crucial in ensuring the integrity of the final filament product and its suitable performance in various applications.
Filament Production Techniques
Extrusion Methods
Extrusion methods are essential in filament production, as they shape the raw aluminum material into a usable filament for 3D printing. This technique typically involves melting the aluminum and forcing it through a die to create thin strands of filament that cool and solidify as they exit. One major advantage of the extrusion process is its ability to produce consistent filament diameters, which is critical for ensuring reliable 3D printing results.
The most popular extrusion method is the screw extrusion technique, where a screw rotates within a heated barrel, melting the aluminum and pushing it through a die. This method is favored due to its efficiency and ability to handle varying material viscosities. An important characteristic of this technique is its energy efficiency, which can lead to lower production costs. However, its reliance on precise temperature control means that any fluctuation can compromise the filament's quality, leading to potential print failures.
Quality Control Measures
Quality control measures are an indispensable element of the aluminum filament manufacturing process. They ensure that the filament produced meets the required specifications for various applications. Consistent monitoring is crucial, as small deviations in filament diameter or material properties can result in significant issues during printing.
Typical quality control practices include measuring the filament's diameter at multiple intervals and employing non-destructive testing methods to assess its tensile strength. The key characteristic of these measures is that they are proactive rather than reactive, catching potential issues before they lead to failures. One unique feature of modern quality control in filament production is the integration of automated systems that can detect anomalies in real-time. Though the initial investment in such technologies may be high, they often pay off in reduced waste and improved product consistency.
In summary, the production of aluminum 3D filament is a multi-faceted process involving careful material sourcing and meticulous production techniques. It combines the necessity for quality with the demands of efficiency, ultimately contributing to the viability of aluminum as a material in the realm of additive manufacturing.
"Quality begins on the inside then works its way out."
This quote underscores the intrinsic relationship between the manufacturing process and the resulting product, making the importance of the manufacturing methods crystal clear.
The ability to control every step meticulously— from the sourcing of materials to the particles traveling through the extrusion machine— allows manufacturers to produce a filament that stands up against the high-performance requirements in fields like aerospace and automotive industries.
Applications of Aluminum 3D Filament
Aluminum 3D filament represents a significant leap in the evolution of additive manufacturing, weaving itself into the fabric of numerous industries. It serves not only as a material but also transforms the approaches engineers and designers take to development challenges. As industries strive for innovation, the importance of aluminum 3D filament shines through its varied applications. Each application leverages its unique properties, providing solutions to traditional manufacturing limitations. The focus here explores such applications in aerospace, automotive, and industrial prototyping.
In Aerospace Engineering
In the field of aerospace, precision and durability take center stage. Aluminum 3D filament, with its high strength-to-weight ratio, aligns brilliantly with these needs. Components like brackets, housing, and even critical parts of an aircraft can be produced with aluminum filament, significantly reducing the overall weight while maintaining structural integrity.
Moreover, the flexibility offered by additive manufacturing facilitates rapid prototyping. Engineers can quickly iterate designs, minimizing delays in production. This leads to quicker project lifecycles, giving companies a competitive edge. The ability to print complex geometries that aren’t feasible with traditional methods opens a whole new world of design possibilities.
In Automotive Manufacturing
The automotive sector is rapidly adopting aluminum 3D filament for a myriad of reasons. For one, it allows manufacturers to produce lightweight parts that enhance fuel efficiency without compromising strength. From prototypes to end-use components, the filament's application spans everything from intake manifolds to brackets and other support structures. With EV (electric vehicle) technology pushing the envelope, aluminum’s potential in accommodating battery housing systems is particularly noteworthy.
Notably, 3D printing with aluminum material fosters customization. Car manufacturers can tailor components to suit specific vehicle models or even client preferences, drastically reducing inventory needs while promoting sustainability through resource optimization.
In Industrial Prototyping
When it comes to industrial prototyping, aluminum 3D filament often proves invaluable. Companies no longer have to rely solely on metal casting or machining, both of which can be costly and time-consuming. By leveraging aluminum filament, businesses can fabricate prototypes rapidly, allowing teams to test and validate designs in real-world conditions.
The costs involved with creating functional prototypes drop significantly, paving the way for innovation. Additionally, having the ability to produce multiple iterations in a short period accelerates the development cycle.
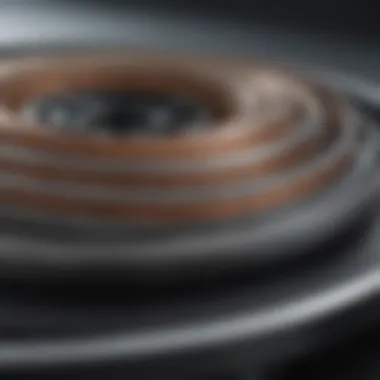
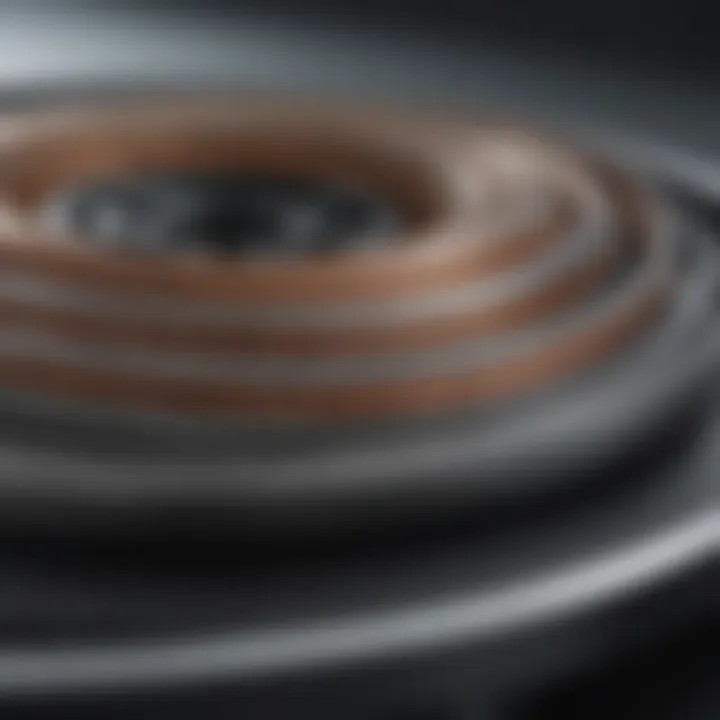
"The unique combination of speed, flexibility, and material properties makes aluminum 3D filament an essential resource in modern manufacturing."
Furthermore, the materials can easily transition from prototype to production, providing a seamless workflow. Organizations can be more agile, adapting designs as needed without the extensive overhead of traditional practices.
In summary, aluminum 3D filament dives deep into three fundamental sectors: aerospace, automotive, and industrial prototyping. Each application not only utilizes its inherent material qualities but also highlights the potential for innovations in manufacturing processes, leading to enhanced efficiency and sustainability.
Advantages of Using Aluminum 3D Filament
Aluminum 3D filament is quickly becoming a game-changer in the field of additive manufacturing. This material brings along a multitude of advantages that make it a preferred choice among engineers and manufacturers alike. Not only does it enhance the performance of printed objects, but it also opens doors to innovative applications. Understanding these advantages is key to exploring how aluminum can reshape industries ranging from aerospace to consumer goods.
High Strength-to-Weight Ratio
One of the standout features of aluminum 3D filament is its impressive strength-to-weight ratio. In simpler terms, it means you get the toughness of aluminum without the bulk. This is particularly crucial in sectors like aerospace, where each ounce matters significantly. Engineers can craft components that are not only durable but lightweight, which in turn translates to fuel efficiency and better performance.
For example, aircraft parts made with aluminum filament help in reducing the overall weight of the aircraft leading to lower operational costs.
Heat Resistance and Conductivity
Aluminum has inherent properties that lend themselves well to high temperatures. The heat resistance of aluminum 3D filament is noteworthy, making it suitable for applications that involve elevated temperatures. This is important for automotive components, for instance, where materials are often exposed to extreme conditions.
Beyond just resisting heat, aluminum is also an excellent conductor of heat. This characteristic allows it to dissipate heat quickly, making it ideal for components that need effective thermal management. Consider engine parts in vehicles; printing them with aluminum filament can lead to more efficient heat dissipation, enhancing the performance of the internal combustion engine.
"Higher conductivity and heat resistance are paving the way for innovations in high-performance applications that demand reliability under stress."
Versatility in Applications
Another feather in the cap of aluminum 3D filament is its versatility. The ability to adapt to a variety of applications gives it an edge over other materials. From creating complex geometries in prototypes to manufacturing parts that bear heavy loads, the scope is vast. For instance:
- Aerospace Components: Used for lightweight structural parts.
- Automotive Industry: Ideal for making components that require a balance of strength and weight.
- Industrial Prototyping: Allows for rapid development of intricate designs.
These varying applications illustrate that aluminum filament is not just a one-trick pony; it has the capability to bridge the gap between traditional manufacturing processes and modern needs.
Challenges and Limitations
Despite the advantages that aluminum 3D filament brings to the table, it’s crucial to acknowledge the challenges and limitations tied to its use. Understanding these aspects is not just academic; it’s a necessity for students, researchers, educators, and professionals navigating this territory. Each of these challenges influences decisions related to material selection, design choice, and overall manufacturing processes.
Printability Issues
One of the primary hurdles in working with aluminum 3D filament lies in its printability. While aluminum is known for its strength and lightness, these characteristics can make it notoriously tricky to print. The filament often requires specific temperatures and settings to ensure a proper build. If the nozzle gets too hot, you risk deforming the material, but if it’s too cool, you may encounter poor layer adhesion.
For instance, you might find that when using a 1.75mm aluminum filament on some printers, the extrusion can become inconsistent, leading to a decrease in dimensional accuracy.
To tackle these issues, users often turn to:
- Specialized nozzles: Hardened steel nozzles are commonly recommended to withstand the wear from aluminum particles.
- Proper calibration: This involves fine-tuning the printer settings, including the temperature and layer height, to suit the specific filament.
- Environmental factors: Conditions such as humidity can significantly affect print quality.
"Correct filament handling and printer settings can be the difference between a successful print and a frustrating failure."
Cost Implications
Navigating the costs associated with aluminum 3D printing can be a daunting task. Generally, aluminum filaments are more expensive than their plastic counterparts due to the manufacturing process involved. This increased cost doesn’t just affect the material price; it also ties into the machinery and setup needed to effectively work with aluminum.
When evaluating the cost implications, consider:
- Initial investments: High-quality 3D printers capable of handling metal filaments often come with a steep price tag. Users need machines that can achieve high temperatures and handle the material’s unique properties.
- Operational costs: Beyond the material itself, the ongoing expenses like maintenance and energy consumption can add up. It’s essential to weigh these costs against the benefits that come from using aluminum in terms of product lifecycle and performance.
- Opportunity costs: Often, companies might hesitate to invest in aluminum printing due to fears that it may not yield a sufficient return on investment.
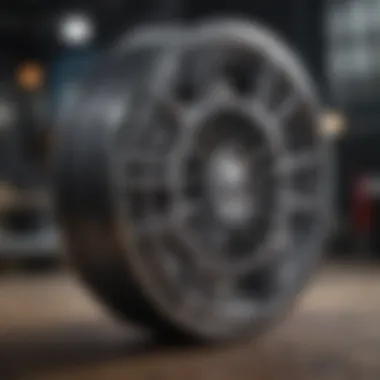
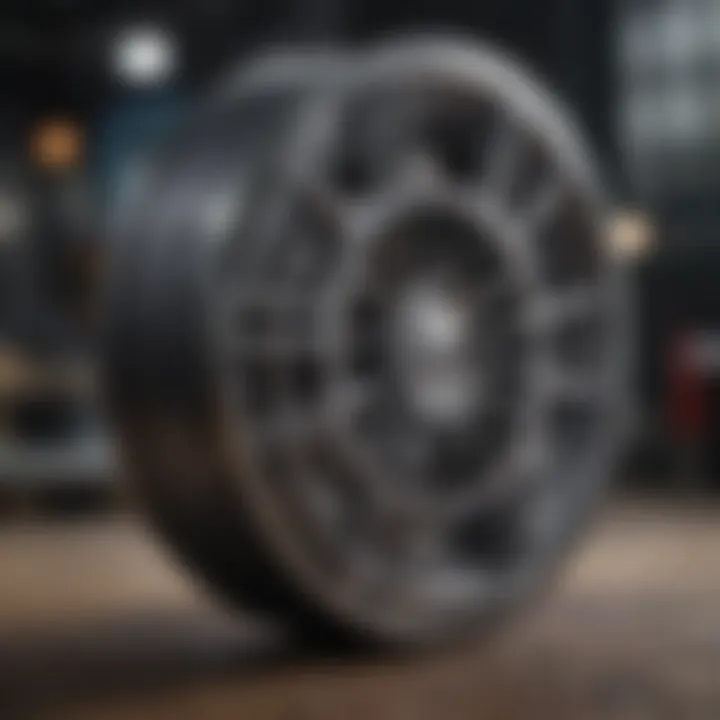
Material Properties Over Time
Lastly, the material properties of aluminum filament can change over time, impacting durability and performance in unforeseen ways. This means that printed parts may not retain their desired characteristics if they are exposed to varying environmental conditions. Factors such as temperature changes, humidity, and even UV exposure can lead to degradation, weakening the material’s structural integrity.
Aspects to consider regarding material stability include:
- Aging: Aluminum may oxidize, affecting surface properties and potentially leading to brittleness.
- Temperature fluctuations: Parts used in high or low temperature conditions may experience unexpected stress and strain.
- Long-term usability: Understanding how printed items will fare over time helps in assessing their long-term applications in various industries.
Future Trends in Aluminum 3D Printing
The exploration of aluminum 3D printing isn't just a fad; it's a critical component of modern manufacturing that is poised for significant transformation. The importance of this topic goes beyond mere production techniques; it deals with innovation, sustainability, and technological integration across various industries. As the landscape of additive manufacturing evolves, understanding these future trends can help stakeholders—engineers, researchers, and manufacturers—prepare for the changes that lie ahead.
Advancements in Alloy Composition
The composition of aluminum alloys is undergoing changes that promise to enhance performance and usability. Traditionally, aluminum used in 3D printing was limited in terms of its mechanical properties. However, manufacturers are now experimenting with varied alloy compositions that blend aluminum with elements like magnesium and silicon. These adjustments can lead to stronger and lighter materials which can cater to specific applications.
- High-Performance Alloys: Research into high-strength alloys is ramping up. These formulations are designed to withstand greater stress while maintaining lightness—a key requirement in industries like aerospace.
- Improved Thermal Properties: New alloys are also being developed with better thermal properties, allowing for improved heat dissipation. This is essential for applications that deal with high temperatures, such as parts for engines and aerospace components.
The significance of these advancements lies in their ability to broaden the scope of feasible applications for aluminum 3D printing. They pave the way for innovations in parts that could not have been reliably produced before.
Innovations in Printing Techniques
As alloys evolve, so do the printing technologies that utilize them. Innovations in printing techniques are improving the efficiency and quality of aluminum 3D printed parts. Techniques such asSelective Laser Melting (SLM) are gaining traction, providing finer control over the printing process.
- Laser Beam Refinement: One trend is the advancement in laser systems used in SLM. More precise lasers result in better layer adhesion, which minimizes defects and enhances the overall structural integrity of the printed object.
- Hybrid Manufacturing Systems: There's also a movement towards hybrid systems that combine traditional manufacturing with additive processes. This integration allows parts to be finished quicker and with better tolerances by utilizing tools that traditional processes have honed over decades.
- Real-Time Monitoring: Finally, innovations in monitoring systems, using sensors and machine learning, can detect anomalies during the printing process. This capability ensures quality control in real-time, increasing the reliability of printed components significantly.
"The combination of advanced alloys and innovative printing techniques holds the key to unlocking new possibilities in aluminum 3D printing, making it a truly transformative element in manufacturing."
The focus on these areas shows promise in overcoming existing limitations of aluminum 3D printing and enhancing its role in various sectors. Stakeholders must stay informed and adapt to these trends, as they are likely to revolutionize the capabilities of products made from aluminum in the near future.
Finale
In the realm of modern manufacturing, the journey into aluminum 3D filament showcases both a profound understanding of materials and a visionary approach towards innovation. As we wrap up our discussion, it becomes clear that aluminum filament is not merely a trend; it is a pivotal component shaping the future of additive manufacturing. Different industries are recognizing the immense potential of this material, considering its unique properties, diverse applications, and the real challenges it poses.
Summary of Key Points
- Applications of Aluminum 3D Filament: Its use spans across various sectors, from aerospace to automotive, enabling the production of lightweight yet robust components that are crucial for efficiency and performance.
- Advantages: The filament stands out due to its high strength-to-weight ratio and excellent heat conductivity, making it an ideal choice for high-performance applications. This versatility in application is a substantial benefit, paving the way for innovative designs.
- Challenges: Despite its merits, aluminum 3D filament presents challenges such as printability and cost considerations. Understanding these limitations is essential for effective implementation and future advancements.
- Future Trends: Continued exploration in alloy compositions and improvements in printing techniques indicate that the dialogue surrounding aluminum filament will evolve, paving the way for robust and refined solutions in manufacturing.
"The evolution of aluminum 3D printing not only challenges traditional manufacturing methods but also invites a new breed of creativity and functionality."
- Continued Research: As the material science field progresses, ongoing research is necessary to tackle existing issues and unlock new potential uses of aluminum filament.
The Importance of Continued Research
The necessity for ongoing exploration in aluminum 3D filament cannot be overstated. As industries evolve, the demands on materials become increasingly complex. Further research allows not only for resolving current challenges but also for anticipating future needs and developing innovative solutions. A collaborative approach involving researchers, manufacturers, and educators is critical. This collective effort can lead to unlocking advanced processing techniques, enhancing material properties, and creating new applications that have yet to be imagined.
With aluminum 3D filament positioned at the forefront of additive manufacturing, it is imperative that all stakeholders engage in the journey of exploration. As we navigate this landscape, the synergy between research and practical application will determine the trajectory of both aluminum filament and the broader realm of 3D printing. The horizon is vast, and the potential for groundbreaking advancements is palpable, underscoring the importance of maintaining momentum in research efforts.
Cited Works
- W. J. S. Williams, "Aluminum-Based Filaments in 3D Printing: A Review," Journal of Advanced Manufacturing Technology, 2022.
- L. Chen, et al., "Additive Manufacturing of Aluminum: Properties and Applications," Materials Science Review, 2023.
- H. Robinson, "Exploring Composite Filaments: Strength and Stability," International Journal of 3D Printing, 2021.
These works illustrate the advancements being made in aluminum filament technology. They also help frame discussions around the nuances of printability and materials comparison that are crucial to comprehending garmenting practices.
Further Reading on Aluminum and 3D Printing
For those interested in expanding their knowledge beyond the confines of this article, a wealth of resources is available. Here are a few recommended reads:
- "3D Printing in Engineering: Applications, Technologies, and Future Trends" by A. T. Kumar—provides insights into broader trends in additive manufacturing.
- "The Handbook of Aluminum: Composites and Alloys" by D. M. Stroud—focuses on various aluminum alloys and their performance metrics.
- Articles from websites like Wikipedia, which often offer brief overviews of concepts and historical developments in 3D printing.
- You can also check forums like Reddit for community discussions concerning practical applications of aluminum filaments, past challenges faced by users, and troubleshooting tips they have gathered.
Engaging with these sources not only builds a comprehensive base of knowledge but also connects theory to practical application, which is key in evolving fields like 3D printing.